New logistics business model at switchgear and controlgear manufacturer Fritz Driescher GmbH & Co. KG – market-synchronized value stream and streamlined production
by Stefan Bünger, Manfred Bürger1, Andreas Gillessen, Prof. Dr. Andreas Kemmner
Increasing market fluctuations and variant diversity as well as shorter delivery times with delivery dates that cannot be postponed caused a lot of extra work and unrest in production and final assembly at Fritz Driescher GmbH & Co. In addition, there was a great deal of manual control effort in scheduling, with the resulting loss of efficiency. Together with the experts from Abels & Kemmner, the management redesigned the logistics business model and established a market-synchronized value chain from component production to final assembly. As a result, production has been greatly reduced, capacity bottlenecks have been resolved, throughput has been increased and throughput times have been shortened. Today, the final assembly department has both Kanban items and components manufactured to order with a very high delivery readiness. The provision of materials for final assembly by the central warehouse was significantly optimized by the introduction of “supermarket shelves”. As a result, DRIESCHER.WEGBERG was able to reduce inventories despite strong sales growth.
Fritz Driescher GmbH & Co. KG in Wegberg is a medium-sized company specializing in the development and construction of switchgear and switching devices for the energy supply industry. The product range includes medium-voltage switchgear (SF6 gas-insulated and air-insulated), medium-voltage switches (outdoor and indoor), transformer stations, low-voltage switchgear and high- and low-voltage fuse-links.
Production is characterized by a very high level of vertical integration, with order-related component production supplying the components required for the final assembly of switchgear and controlgear. Component production consists of machining, the sheet metal processing center, the robot welding center, the powder coating plant, small assembly and support production (second plant). The final assembly department then uses the components manufactured in-house to assemble the switchgear and switching devices to order.
Initial situation:
For DRIESCHER.WEGBERG, being the only medium-sized company in its sector to be able to survive on the market requires not only technically and qualitatively outstanding products, but also a high degree of flexibility in meeting customer requirements – with extremely short delivery times and adherence to deadlines. Although the on-time delivery of the switchgear and switching devices assembled to order has largely been met (the delivery dates are fixed and cannot be postponed), the deadline situation has become increasingly critical in recent years. Delivery deadlines could only be met with a great deal of friction and commitment from everyone involved. The previous logistics business model took the form of order-related component production and order-related material provision for final assembly. Due to market fluctuations, the increase in the number of variants and shorter delivery times, this logistical business model has now reached its limits. Furthermore, the order center had to compensate for the lack of detailed capacity planning and partial scheduling of component production dates in the past through manual prioritization. As a result, constant coordination was required between component production, the central warehouse, final assembly and the order center; an almost impossible task due to the complexity of the products and the variety of parts.
As a result, components were constantly missing in final assembly, which led to the temporary storage of parts and systems that could not be fully assembled. Component production, particularly machining, struggled with high order backlogs and long throughput times. Thanks to the great flexibility of the working time accounts in component production and the relatively high proportion of manufactured standard parts, it was still possible to meet delivery deadlines at high cost and with large inventories. In order to continue to manufacture, assemble and deliver economically, quickly and on time, a new optimized logistics business model was required, which would also give DRIESCHER.WEGBERG new competitive advantages.
Good conditions for 80/20 leveling
Before designing and implementing the optimized logistics business model, a detailed analysis of the current situation was carried out. A portfolio analysis of the individual parts made it clear that a large proportion of production capacity utilization (approx. 69%) is accounted for by only around 10% of the parts that are required on a fairly regular basis and are therefore well suited to so-called pull control based on the supermarket principle. The remaining approx. 90 % of parts to be manufactured occupied the remaining third of the production capacity. The core element of the new logistics business model was therefore an 80/20 leveling in production. However, in order for this 80/20 leveling to function smoothly, a number of prerequisites had to be checked or created.
For example, it had to be ensured that an appropriate production capacity was kept free in the medium term for order-specific parts so that these parts could be produced without a queue if possible.
It also had to be checked,
- how the XY and Z articles are distributed to the various machines in the different production areas,
- how evenly the capacity load with XY parts on the one hand and Z parts on the other is over time,
- whether the material flows can be physically separated to some extent by assigning separate machines to the Z parts,
- whether line production can be set up for different material numbers.
As the results of the analyses showed, the existing capacities in the various production areas were sufficient over time to produce both the XY items to be stockpiled and the Z items to be produced to order on schedule.
A separation of the material flows between XY and Z articles or line production on different material numbers was not necessary or sensible.
Full production hoppers had to be emptied
However, a throughput time analysis in component production showed that despite a balanced inflow and outflow of production order hours, there were excessively long order queues in front of the various capacity units in production, which were the main reason for the long throughput times. The work backlog averaged 21 working days and led to major problems in meeting deadlines in component production.
In order to correctly position component production logistically and focus on short throughput times and high adherence to delivery dates, the work in progress in component production had to be reduced with the following direct measures:
- The production work in progress was reduced to the new required target level by temporarily increasing production capacity through additional and ghost shifts and the outsourcing of orders.
- A personnel capacity management system was developed and installed, which shows the short-term personnel capacity requirements for the various areas of component production. With this tool, production management was and is able to shift employee capacities in line with current production requirements and precisely schedule temporary work capacities in terms of time and quantity
- Production orders were only loaded on time and no longer prematurely.
- As a matter of principle, production orders were no longer scheduled back in time. Over the course of six months, these measures made it possible to reduce production order throughput times to an average of four days.
Furthermore, as part of the as-is analysis, the planning and control in scheduling with the Baan 5 system as well as the work organization in final assembly and component production were analyzed in detail and evaluated in terms of data technology.
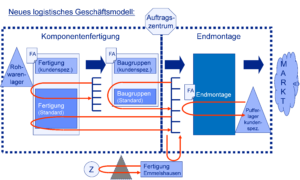
New logistics business model:
Once a production situation has gotten out of hand, the situation can only be rectified by correctly balancing the production chain in terms of capacity and orders. Based on the results of the as-is analysis, the consultants defined and designed the new logistics business model and the necessary fields of action. The aim was to adapt the logistics business model to market requirements and establish a market-synchronized value chain.
The fields of action and packages of measures associated with the new logistics business model are defined accordingly:
- Final assembly:
- Two-bin Kanban for XY and some Z parts on the supermarket shelves in final assembly.
- Component production:
- Systematically reduce throughput time for component production,
- operational capacity management,
- 80/20 leveling of production capacities for standard (XY) and order-specific (Z) parts,
- Pull control for some of the standard components (XY parts),
- Push control for order-specific parts (Z parts).
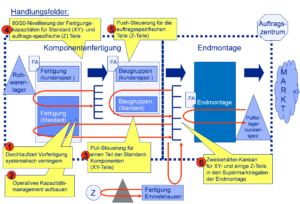
“Rabbit” and “hedgehog” strategy in component production:
As the as-is analyses underpinned, the article structure was ideally suited to an 80/20 leveling. Whereas previously all items were manufactured to order and only stored in batches, the AB/XY items (“hedgehog” items) are now stored in the central warehouse or on the supermarket shelves in final assembly under the new logistics business model using pull control (via Kanban). The major advantage is that capacity utilization is now more continuous.
Despite this new stock level for the AB/XY articles, stocks have been reduced! All items to be produced on an order-related basis can thus be prioritized with short throughput times and fast availability (“rabbit” items) (push production via production order in the Baan 5 system).
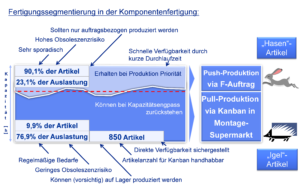
Pull control via Kanban:
A pull control system was set up via Kanban for items that are regularly consumed. For this purpose, a corresponding extension for Kanban control had to be programmed in the Baan 5 system. This was also necessary for the two-container kanban system in the final assembly.
Today, the Kanban cards of the empty containers from component production are scanned in the central warehouse and the yellow and red areas of the Kanban board are monitored electronically in Baan. If the red zone is reached, component production must start production; if the yellow zone is reached, it can do so. This has created additional flexibility in component production via the yellow area in order to optimize capacity utilization.
Operational capacity management:
A simple Excel Access application also helps to set up capacity planning based on Baan 5 data for all production capacities. Capacity requirements (machines/personnel) are now monitored on the basis of the production requirement dates for each production stage. This means that current and future bottleneck situations are immediately visible and can be actively dealt with and thus avoided in most cases.
Two-bin Kanban for XY and some Z parts on the supermarket shelves in final assembly:
In the past, the central warehouse provided all components for the order-related assembly of switchgear and controlgear for final assembly. Due to the large number of items required for a switchgear system and the problems in component production, final assembly often had to contend with missing components. As a result, the employees were unable to finish building the partially assembled switchgear and had to store components temporarily, which led to space problems and frequent searches for materials.
Under the new logistics business model, all XY and some Z items are stored in a two-bin Kanban system in the final assembly area. To this end, the final assembly area was converted so that each of the eight assembly areas could have its own Kanban racking and pallet spaces. If a container is empty today, a stock transfer order is generated in the central warehouse by scanning the corresponding barcode. The empty container must be refilled within two working days. During this restocking time, the employees help themselves to the required components from the second Kanban container. This system makes it possible to supply final assembly with standard components with a delivery availability of over 98% in some cases. An enormous reduction in stock removal processes also relieved the burden on the central warehouse in particular. Like component production, this now prioritizes order-related components in the transfer processes from the central warehouse to final assembly, which in turn has led to high availability of all components in final assembly. In final assembly, a total of 3,176 items have so far been converted to the two-bin kanban system for the eight assembly areas.
In order to avoid the problem of switchgear that cannot be assembled to completion and its interim storage with subsequent material search, the material provision (picking reports) for the order-related manufactured articles was reorganized in the Baan 5 system in such a way that stock transfer orders to final assembly now only take place if 100% material availability of all components for an assembly order is given.
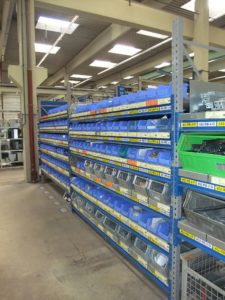
Rules, scheduling parameter optimization, monitoring of production segmentation:
In order to efficiently carry out push and pull control for component production and the two-bin kanban system in final assembly, the planners and schedulers regularly adjust the planning, control and scheduling settings in the Baan 5 system for specific items. The “operating point” is always readjusted so that the value chain functions at minimum cost. In order to achieve this, it was necessary to develop a set of rules for optimizing the system settings (technical jargon: scheduling parameter optimization). The parameter settings for the individual article classes (ABC/XYZ/ELAN/etc.) such as push/pull control, degree of readiness for delivery, safety stock, ordering method, etc. were defined in the rules.
The entire range of articles managed by the order center is structured as follows
- components with reasonably even requirements, and
- Components with a low degree of repetition, sporadic demand behavior or customer-specific parts.
While the first group of parts is managed via Kanban organization, the second group continues to be managed conventionally in order to avoid unnecessary stocks while still meeting delivery deadlines and further reducing delivery times. The application of the rules to all articles and the determination of the parameter settings to be changed in the Baan 5 system can no longer be done manually. The effort required for this would be far too great. Due to the variety of system settings to be changed, this is now being done with the help of the DISKOVER SCO simulation software, which has already been used to analyze the current situation and simulate various scenarios.
With the help of DISKOVER SCO, planners and dispatchers can also perform three other important tasks regularly, efficiently and semi-automatically in addition to scheduling parameter optimization:
- checking the push/pull items for component production as well as for the two-bin Kanban items on the supermarket shelves in final assembly.
DISKOVER determines which items need to be removed from the Kanban system and which need to be converted to Kanban and provides them in the form of a report. This regular maintenance is necessary to ensure that the right parts are controlled in the Kanban system and the right parts in the push system in the future. Without this care, the entire production system would lose its balance in the medium term. - the readjustment of the 80/20 leveling.
In order to keep the 80/20 leveling in balance, DISKOVER calculates how much production capacity must be kept available for customer-specific push orders and which capacities can be used on average for Kanban production. Depending on the available Kanban capacity, the following then takes place - the re-dimensioning of Kanban articles.
This involves determining and simulatively checking how large the item-specific circulating stocks and therefore the number of Kanban cards per Kanban item must be. Too many cards lead to unnecessary stocks, too few cards lead to problems with availability.
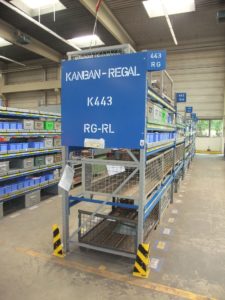
Practical experience:
At DRIESCHER.WEGBERG, the new logistics business model and the market-synchronized value stream have led to a great deal of calm in component production, the central warehouse and final assembly. The high readiness to deliver in final assembly, the high adherence to delivery dates and the increase in throughput in component production – without increasing capacity – as well as the high level of acceptance and satisfaction among employees are evidence of this.
The kanban-controlled items have become so-called self-runners that only need to be checked and readjusted at regular intervals; the order center, production, central warehouse and final assembly can concentrate on the components to be manufactured for specific orders.
With the implementation of the new logistics business model, DRIESCHER.WEGBERG has significantly strengthened its competitive position in the market, which is impressively reflected in the disproportionately high growth in incoming orders.
1 Stefan Bünger is an authorized signatory and Manfred Bürger is head of the order center at Fritz Driescher GmbH & Co KG, Wegberg.
Further information on this topic can be found here:
- Production segmentation, material flow optimization and Heijunka control in the gold spring manufactory
- Ongoing upswing complicates the planning and scheduling process
- Supply chain optimization for retailers