A case study by Armin Klüttgen1 and Thomas Körfer2
When investors buy companies, they also look for the liquid funds required for the restructuring that is often necessary in the new company. There is often great liquidity potential in excess inventories. Reducing them creates interest-free liquidity, promotes market orientation and also optimizes the company’s net asset value. Abels & Kemmner carried out a corresponding potential analysis for an investor in the automotive supply industry within 14 days. The result: around 20 percent of the planned investments can be raised by the company itself through inventory reductions alone. This free financial subsidy is now being raised.
The rapid scan carried out at Alpha GmbH* – an automotive supplier with several internationally distributed production sites and country representatives – differed from a classic logistics potential analysis in that the project was carried out at an unusually high speed and intensity. Within 14 days, the value chain, logistics business model, customer structure, sales planning and product structure had to be analyzed. The market situation, the planning and scheduling processes and the quality of the data sources were also analyzed. Just thirteen calendar days passed between the start of the project and the day of the final presentation. In order to carry out such a project with around twelve thousand articles in such a short time, a particularly high level of methodological and project management expertise is required. Basically, every single detailed process in such short-term projects is on a critical path and milestones with decisions on how to proceed are reached virtually every hour. In order to achieve reliable and detailed figures for the entire article master in such a short time, suitable data analysis and simulation tools are indispensable.
Objective: Release as much liquidity as possible
The existing requirement of the project was to present a concept in the short term with which the existing inventories could be significantly reduced by the end of 2010 in order to be able to use these liquid funds to finance as much of the investment as possible from the company without interest. In addition, suitable short-term measures were to be implemented in the final weeks of 2009 to initiate a corresponding development and achieve initial reductions in inventories in order to finance an expiring credit line without interest. In addition to the sustainable improvement of planning and scheduling, special measures have therefore been developed for items that have experienced a structural break in consumption behavior due to the current economic crisis.
Portfolio reduction: interest-free investment financing
There are many types of investment financing. But no matter what calculation you make: The best way to do it is from your own resources. If you look at the potential in companies, it is often only the inventory that can be reduced across the entire value chain without any side effects. This not only creates liquidity, but also saves costs.
Investors need highly accurate results in the shortest possible time
In order to be able to provide all the necessary data in a correspondingly short time, the data and process analysis were parallelized. In addition, several inventory driver workshops were held at short notice in order to be able to quickly and effectively counter the sometimes very high individual inventories. This type of parallel implementation of all relevant measures would not have been appropriate in a normal company situation, as it produces a lot of work at certain points and, with normally regulated processes, also disruption in the company. In reorganization processes, however, it is necessary to create new structures quickly. This requires consultants to be proficient not only in inventory management but also in reorganization processes, as these involve quick top-down decisions that often lead to parallel project steps and decisions and demand a high level of skill and sufficient routine from the responsible project manager. With its two pillars in both the refurbishment and portfolio management business, A&K was therefore an ideal partner for this project.
The result
Defensive calculations of the rapid scan showed 26% sustainable inventory reduction potential that can be achieved within one year. Liquidity potential of around EUR 100 thousand was also identified during the portfolio driver workshops. Euro and released on the same day. The expiring credit line could thus be cushioned completely by the company itself. All in all, a successful project that has provided valid figures for the investor’s further financial planning.
Rapid Scan Day 1
On the first day of the project, the DISKOVER SCO simulation software was connected to the productive SAP system within a few hours, enabling all relevant and current data to be recorded for the analyses to be carried out. At the end of the day, the results of an ABC and XYZ analysis were already available and initial findings on consumption regularities and the ability to plan individual items as well as existing stock structures were revealed. Parallel to the preparation of the first data analyses, the process analysis also began on the first day, which provided an overview of the situation as well as specific tasks and problems “upstream” through the entire value chain, starting from the market and ending with the suppliers.
Rapid Scan Day 2-8
The parallel data and process analysis practiced in the project from the outset was consistently continued. While complex simulations were parameterized and carried out on the basis of the productive data to determine the inventory reduction potential, the project team worked out the causes of excess inventories in the context of inventory driver workshops. Despite the short project duration, this project step also included a visit to the Czech production site in order to obtain as complete a picture as possible across all sites. The inventory driver workshops explored the story behind each individual item, with preliminary data analyses in SAP and DISKOVER SCO identifying the items that require closer examination. These articles were then scrutinized in detail in the workshop. Possible measures to reduce excess stocks and avoid such situations in the future were also developed. Questions that come up in portfolio driver workshops are, for example:
- How can a stock trend be explained?
- Why was an initial filling so high?
- Why were quantities procured although stock ranges were still significantly higher than the replenishment time?
- Why are safety stocks held with a range of one year or more?
Key portfolio drivers at Alpha GmbH were, for example:
- Backlog of open orders with long replenishment times for items with structural breaks
- partially incorrect disposition methods
- Incorrect preliminary planning and no monitoring of the preliminary planning
- No end-to-end planning process from sales planning to purchasing
- No monitoring of start-up phases for new articles
- Customer-supplier relationship between own locations with bull-whip effect
- Wide range of variants with early definition in the specified customer material
- No harmonized batch sizes
- Restart process not clearly regulated
- Data quality in the ERP system
- Rudimentary use of existing possible system support
- Project business in which promised start dates are postponed or quantities are reduced or withdrawn completely
Overall, these and other inventory drivers had led to unsatisfactory stock turnover rates and inventory ranges in the past. The need for action in the short and medium term became clear.
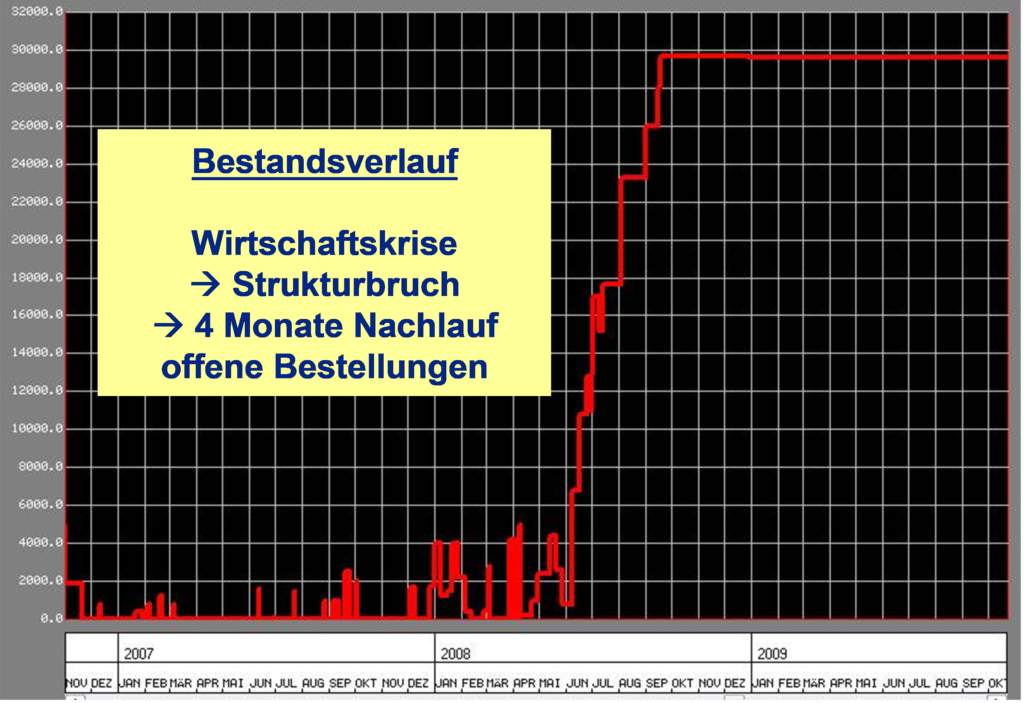
Rapid Scan Day 9-12
In the last third of the rapid scan, the aim was to translate the results of the simulations and the findings from the process recordings and inventory driver workshops into recommendations for action and measures as quickly as possible. The simulation showed an overall reduction potential of approx. 26%. However, reducing the stock through normal consumption alone would have taken too much time, as the simulations showed. In order to achieve the overall reduction in inventories by the end of 2010, the concept therefore provided for an extensive catalog of short-term special measures in addition to improved planning strategies and scheduling methods with a medium-term effect. The examination of conversion options for existing products was particularly important here. With the appropriate system support, it is possible to analyze the use of components via a bill of materials breakdown to see which high-quality components have the best chance of regular consumption in which end product. In the case of sets in particular, there was clear potential to accelerate the flow of material. In addition to the special measures, further activities were initiated to achieve a sustainable reduction in inventories. The main topics were:
- Strategic measures -> Review and optimization of the logistics business model
- Process optimization -> Improvement of sales planning and scheduling
- Method and parameter optimization -> Structure of decision tables for dispo parameter optimization
- Products -> Logistical optimization of the product range
- Effort and process efficiency -> Improvement in system support and knowledge of correct system handling
- Employee qualification and motivation -> Expansion of employees’ planning and management expertise
Rapid Scan Day 13: The concept
The packages of measures listed were incorporated by A&K into the overall concept of a sustainable, lean solution for releasing unnecessarily tied-up cash and cash equivalents. This encompasses all three directions of systematic inventory management (see illustration).
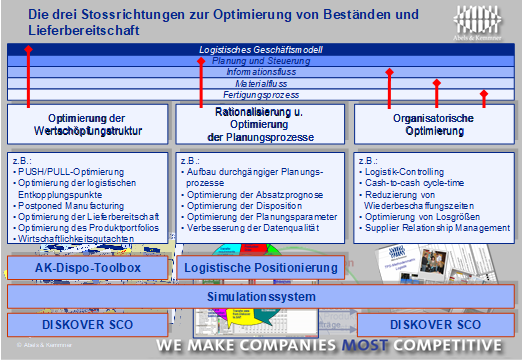
Conclusion
The impetus for implementing measures to optimize inventories and delivery readiness can be of a very different nature. A&K often carries out projects in which customer satisfaction is to be increased by optimizing the degree of delivery readiness without causing inventories to skyrocket. However, a significant proportion is also made up of projects in which inventories are to be reduced in order to create liquidity and improve the company’s return. Sometimes, and especially in these times, the existence of a company or the success of an investment depends on a rapid reduction in inventory. By combining its experience in reorganization and restructuring with its expertise in portfolio management, A&K is able to implement such projects, which under “normal conditions” would possibly take three months, within 14 days. 26% inventory reduction potential and an immediate €100,000 reduction also speak for themselves. If you would like to know exactly what measures Alpha will take to achieve these inventory reductions and what the new logistics business model looks like, please request the relevant documents personally at alpha@ak-online.de.
*The name of the company was changed to Alpha GmbH to protect legitimate expectations.
1ArminKlüttgen is Principal at Abels & Kemmner GmbH.
2ThomasKörfer is a consultant at Abels & Kemmner GmbH.