In order to resolve capacity bottlenecks in production, switchgear manufacturer Fritz Driescher has established a market-synchronized value chain from component production to final assembly.
Medium and low-voltage switchgear, transformer stations and high- and low-voltage fuse-links are part of the product range of Fritz Driescher GmbH & Co. According to its own information, the family business is now the only medium-sized company in its sector. This requires high product quality, a high degree of flexibility with regard to customer requirements, short delivery times and adherence to delivery dates.
The components for the order-related final assembly of the switchgear are provided by Driescher’s central warehouse. The previous logistics business model provided for order-related component production and material provision for final assembly. However, in view of increasing market fluctuations, a growing number of variants and shorter delivery times, it was increasingly reaching its limits.
The order center had to compensate for the previous lack of capacity planning by prioritizing orders manually. In some cases, the schedulers scheduled the production dates in the past. There was an ongoing need for coordination between component production, the central warehouse, final assembly and the order center. However, components were often missing during final assembly. Employees were unable to complete partially assembled switchgear and began to store components temporarily, which led to space problems and frequent searches for materials.
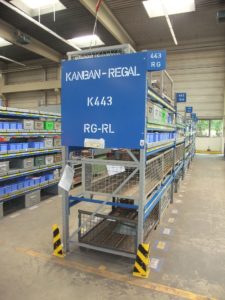
Throughput times too long
At the same time, component production was struggling with high order backlogs and long throughput times. “The delivery dates could only be saved with high costs, large inventories, great flexibility in working time accounts and a relatively high proportion of standard parts,” recalls Manfred Bürger, head of the Driescher order center.
Finally, Driescher recently decided to establish a market-synchronized value chain. The management consultancy Abels & Kemmner GmbH, Herzogenrath near Aachen, initially carried out an analysis of the current situation with the help of advanced planning and scheduling software (APS). It revealed that 69 percent of the production capacity was utilized by only ten percent of the parts. The remaining 90 percent or so occupied a third of the production capacity. In component production, the average worklist was 21 working days. This led to long throughput times and problems with meeting deadlines.
In order to increase production capacity, orders were temporarily outsourced. A personnel capacity control system was installed in order to adjust employee capacities to current production requirements at short notice. Orders were no longer placed in the past or loaded prematurely, but only on time. Over the course of six months, these measures made it possible to reduce throughput times to an average of four days.
Today, Driescher works according to the “hare and hedgehog” strategy. It is based on an 80/20 leveling of production capacities – differentiated according to standard (XY) and order-specific (Z) parts. “Hare” articles (Z-parts) continue to be prioritized in a production order with short throughput times and fast availability (push production). In contrast, “hedgehog” items – these are AB/XY items and some Z parts – are stored in the central warehouse using pull control (via Kanban) or in a two-bin Kanban system in so-called supermarket shelves in final assembly. It was converted so that each of the eight assembly areas could have its own Kanban racking and pallet spaces. If a container is empty, a transfer order is generated in the central warehouse via barcode scan. The box must then be refilled within two working days. During this stock transfer time, the employees help themselves from the second Kanban container.
This system makes it possible to supply final assembly with standard components with a delivery readiness rate of over 98 percent in some cases. So far, 3,176 items have been converted to the two-bin Kanban system for the eight assembly areas. Interesting detail: Despite the additional storage level, inventories fell.
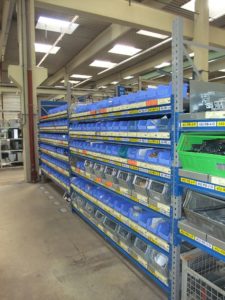
An extension was programmed in the ERP system “Baan 5” from Infor GmbH, Friedrichsthal near Aachen, for pull control via Kanban. A simple Excel Access application also helps to set up capacity planning based on Baan 5 data for all production capacities.
Self-running Kanban articles
The capacity requirements for machines and personnel are now monitored on the basis of the requirement dates for each production stage. In addition, material provisioning (picking reports) for order-related manufactured items was reorganized in the Baan 5 system so that stock transfer orders to final assembly now only take place if 100% material availability of all components for an order is given. The planners regularly adjust the planning, control and scheduling settings in the Baan 5 system using the APS software on an item-specific basis.
Result: The new logistics business model increased throughput in component production without increasing capacity. “The Kanban-controlled items have become self-runners that only need to be checked and readjusted at regular intervals,” summarizes Bürger.
Fritz Driescher
Fritz Driescher GmbH & Co. KG, based in Wegbergis, specializes in the development and construction of switchgear and switching devices for the energy supply industry. In 2008, the family-run medium-sized company generated sales of EUR 40 million and employed 384 people.