The ‘Solutions’ division at Serag Wiessner manufactures infusion solutions, products for wound treatment, special solutions and customer formulations. The majority of products are supplied from stock. This requires the control of a complex production process with specific restrictions – a task that can hardly be accomplished by hand.
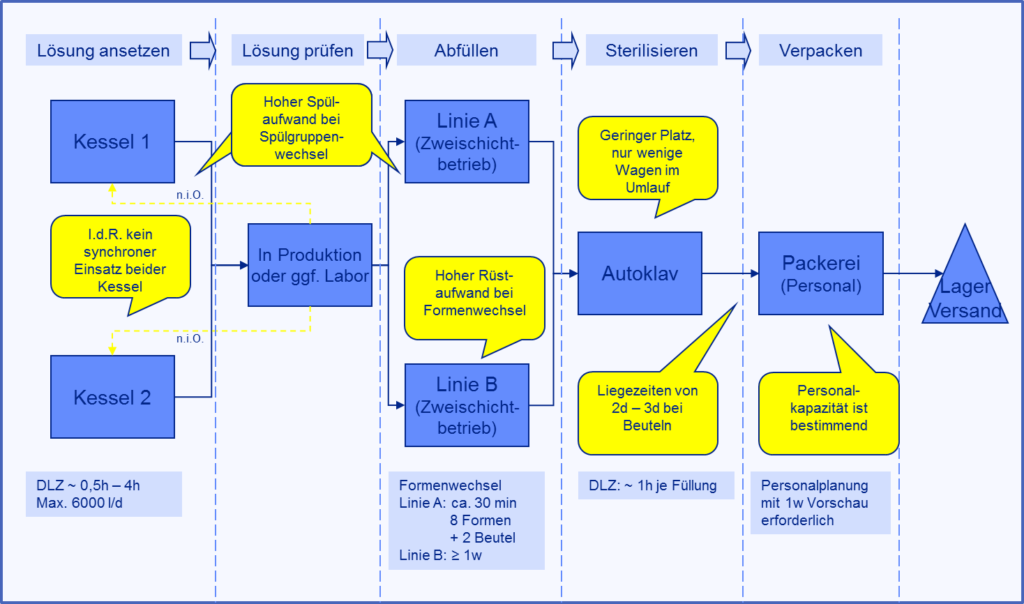
With the aim of reducing throughput times, lowering inventories to the necessary level and at the same time maintaining delivery readiness at a high level of 93 percent, Serag Wiessner set about scrutinizing processes in the ‘Solutions’ segment. The company manufactures surgical suture material and sterile liquid dosage forms. The Enterprise Resource Planning System (ERP) already provided simple forecasts for sales and demand planning of the finished products. On this basis, the schedulers worked out planned and production orders. As delivery readiness is of great importance, securities were found in inventories and throughput times. In the production area, there are also many influencing factors to consider, which together lead to a very high level of complexity. In addition, there were numerous ad hoc orders due to insufficient stocks, which resulted in short-term rescheduling processes and affected the efficiency of the processes. The aim of the project was therefore to enable optimized production planning and control based on system-supported sales planning. As a result, a resource-saving production sequence should be presented, taking into account relevant criteria according to agreed rules.
Filling process: From the kettle to the bottle
The filling process starts when the solutions are prepared in two vats. After checking the specification and product requirements, the filling process takes place in bags or bottles. Two lines are available for this purpose: one for pouch products and one for bottled products. After filling, the sterilization process takes place in the autoclave. This process is discontinuous, i.e. the autoclave is filled to capacity and then the temperature-controlled sterilization process takes place over several hours. The products are then fed into the packaging. The following restrictions must be taken into account when planning and controlling this process:
- High set-up and cleaning times sometimes have to be taken into account in capacity planning and scheduling. The set-up time for filling the bottles is around one week, so the system was only converted twice a year.
- The space between filling and autoclave is cramped. With large-volume products, this can lead to a backlog in front of the autoclave.
- Filling is the bottleneck for small-volume products; the autoclave and packaging are not used to capacity.
- The filling process must be completed on the same day until sterilization in the autoclave. A new filling process can only start with a pre-run so that the filled goods can be sterilized by the end of the shift.
- The system for filling the bottled products does not change the setup status over a longer period of time.
Products that require the current setup status must be in stock at the time of the changeover to such an extent that their availability can be maintained until the next changeover.
Calculation of the EPEI as a basis for planning
To manage the complex planning process, planners and production controllers should be supported by suitable software. In addition to determining the correct production quantities, an optimized sequence of production orders should also be determined. As a result, a suitable product mix should ensure the best possible capacity utilization and keep set-up costs to a minimum. At the same time, it was necessary to build up stocks of bottling products to bridge the duration of the set-up cycle. The main questions were which batch sizes are the right ones and how many set-up processes can be carried out. The ‘Every Part Every Interval’ (EPEI) principle was used to answer the question. This is the shortest possible period of time in which each product can be manufactured in sufficient quantities. This approach enables optimum utilization of resources through machining and set-up processes. This also showed that the filling line can be set up more frequently than twice a year. Taking into account small time buffers, the number of set-up processes could be doubled and the batch size halved.
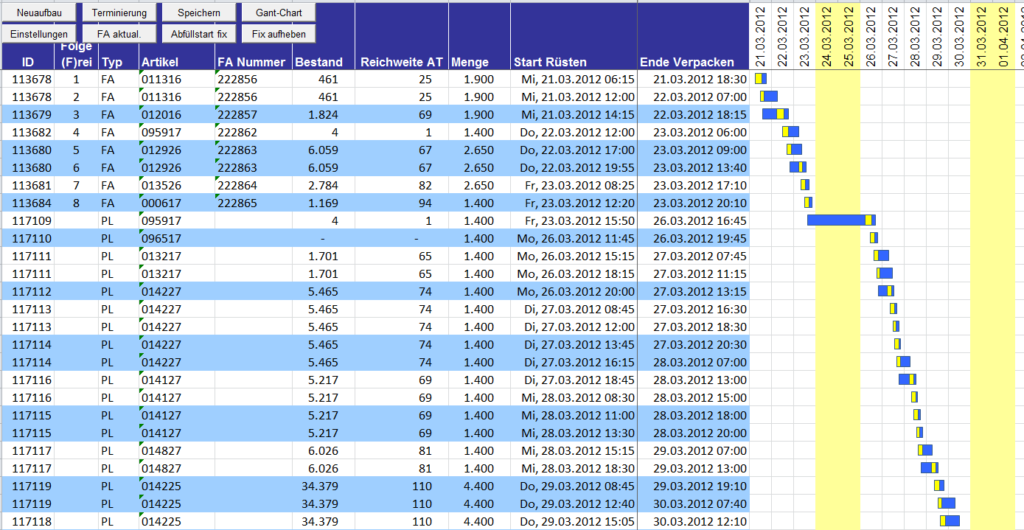
By using the new production planning solution, Serag Wiessner was able to reduce inventories in the PL production segment by 23 percent after two months. In addition, planning tasks can also be taken over by other employees after a brief introduction to the tool.[/]
Important input variable: the forecast
A key input parameter for planning is a reliable demand forecast. This is determined during operation using the DISKOVER SCO software optimization system already in use in another product segment. The software provides demand figures to fulfill the desired delivery capability as well as production proposals, taking into account demand and the procurement situation. These are now picked up by the production control system, sequenced and scheduled. This is based on a set-up matrix that contains the set-up times for possible product changes in the filling process. The algorithm takes into account the production progress and the setup status of the filling system. Taking shift and break times into account, the orders are scheduled at work process level and displayed in tabular form and as a Gant chart. The production controller can now convert the orders and transfer them to the ERP. The solution also offers the option of fixing, splitting or changing the sequence of orders. After two months of use, inventories in the PL product segment were reduced by 23 percent. At the same time, the delivery situation has improved significantly. Much more important, however, are the high level of overview and the rapid completion of the planning task.
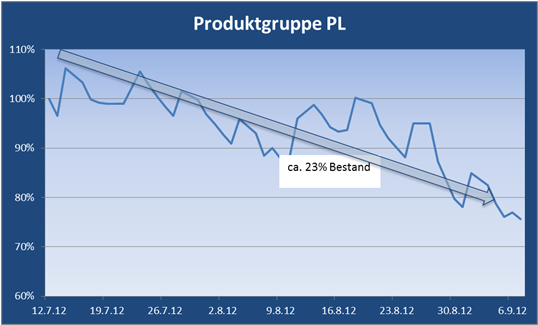
The authors: Steffen Schwippl is Head of IT at Serag-Wiessner KG, Dr. Bernd Reineke is Managing Partner of Abels & Kemmner GmbH.