High availability and automated dispensing parameters
By Dr. Bernd Reineke, Abels & Kemmner GmbH, Christian-Hans Bültemeier and Michael Meier (HANSA-FLEX)
HANSA-FLEX is Europe’s leading system provider in fluid technology and a value-added partner for companies of all sizes. The importance of fluid technology is growing worldwide and with it the benefit expectations of HANSA-FLEX customers in all sectors of the economy, in Germany and worldwide.
In addition to individually assembled hydraulic hose lines, HANSA-FLEX offers a comprehensive range of connecting elements for hydraulics. All products are usually available or on site within 24 hours. HANSA-FLEX’s principle for success is system partnership: it is the breadth and depth of the product range and services that make the company a valued partner, both in the after-sales sector and increasingly in the original equipment sector. HANSA-FLEX is able to operate close to its customers and deliver quickly and competently, particularly thanks to its close network of branches and service vehicles. HANSA-FLEX products are needed wherever machines, systems or heavy equipment are used. Customers’ systems have to run – securely, reliably, around the clock. Availability counts, downtime costs money. And this is one of HANSA-FLEX’s core competencies: maximum availability in all products and rapid assistance directly on site.
To review the supply chain processes, HANSA-FLEX commissioned Abels & Kemmner with the project to uncover potential in the processes and develop proposals for action to improve them. In particular, the planning and scheduling methods and the use of the ERP system (SAP) were to be reviewed.
A quick action plan with a proven approach
To review the planning and scheduling processes, the A&K consultants apply their tried-and-tested approach in four subsections:
- Process analysis
In the process analysis, the planning and scheduling processes are closely scrutinized. The focus here is on the consistency of the planning chain and the targeted use of methods, procedures and parameters. The degree of system support is also recorded. - Article and inventory analysis
In this step, only data and facts that are provided from the ERP system, if possible, count. Abels & Kemmner’s tried-and-tested tools are used to determine the potential in inventories and availability. As HANSA-FLEX uses the SAP ERP system, providing the movement and master data was not a problem. With the powerful A&K data pump, even the large volume of data at HANSA-FLEX (several million master data records) could be extracted within a short time and transferred to the DISKOVER SCO analysis tool. - Evaluation workshops
Following the process and data analysis, the specialists from A&K were already able to uncover initial potential. The evaluation workshops with the planners and dispatchers clarify in detail whether there is actually potential to the extent identified. Individual cases are discussed and clarified down to article level. Uncovering many details brings up the restrictions that planners and schedulers have to deal with on a daily basis and take into account in their planning results. Quick wins can often be achieved during the evaluation workshops. For example, incorrectly maintained parameters such as delivery or throughput times are detected and corrected immediately. Safety stocks or safety times that were once justified can be uncovered, questioned and corrected in the workshop. After these workshops, the input parameters of the analyses and simulations are adjusted and the potential is recalculated so that realistic, reliable figures are available as a basis for further activities. - Concept and measures
Measures must be defined and implemented in order to actually leverage the potential. In this phase, proposals are therefore developed with the following focal points:- Methods to be used for scheduling and batch size calculation
- Suitable methods for forecasting and safety stock determination
- Optimized process flows and task distribution
- Targeted use of IT systems for more efficient processes
When defining and designing the measures, the sustainability of the solutions is of the utmost importance. Developing solutions and changes is one thing, but designing these solutions and changes in such a way that they react dynamically to changes and adapt to changing influencing factors is another.
Results
The process and data analysis at HANSA-FLEX revealed high potential in the area of the two central warehouses of approx. 16 % inventory reduction. The achievable availability also reaches a good level of over 98% in the central warehouses. The number of branches can also be reduced by around 15 %. However, the realizable availability here is somewhat lower due to demand. The reason for the low availability is the strong sporadicity of demand in the branches. Here, the proportion of Z and Z2 articles, i.e. articles that are sporadically or very sporadically requested, is very high at over 80% (see chart). These items are often ordered in quantities that were not available in the past (see chart on the right). In this case, the forecast and safety stock are not sufficient to be able to deliver from stock.
Against this background, we can be satisfied with the result of availability in the branches. If customer demand cannot be met directly, it is possible to fall back on replacement items, which the specialists and fitters in the branches make use of in these cases. Or the central warehouse delivers the item overnight, which is usually tolerable.
Measures
In order to actually leverage the identified potential in the long term, the concept of an end-to-end planning chain was developed as the main measure (see illustration).
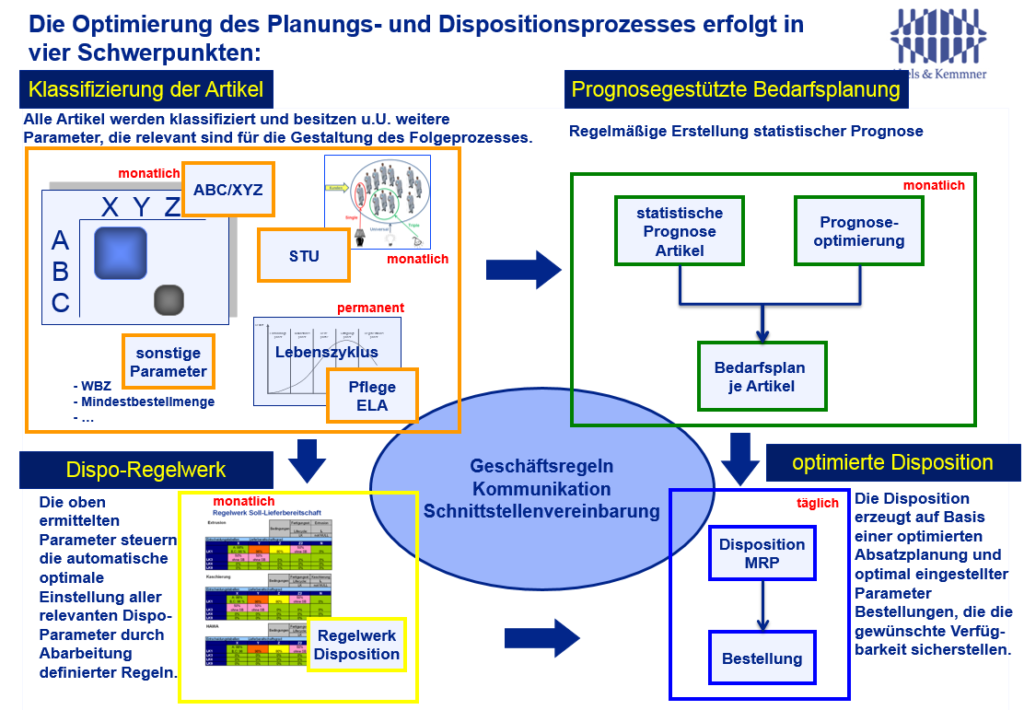
The concept consists of five building blocks:
- the regular classification of articles,
- forecast-based demand planning,
- the rules and regulations for disposition (disposition rules and regulations),
- optimized disposition and
- the regulated exchange of information.
As part of the classification process, various properties of the items are determined and assigned. The most important features are the ABC classification, which determines the value significance of an item. The XYZ analysis, which determines the regularity of demand, and the life cycle analysis, which checks which phase each individual item is in (e.g. start-up or discontinuation phase).
In the MRP system, these properties form the basis of the decision tables that determine, for example, whether an item is in stock or not, whether it receives a forecast or a safety stock or with which lot size the item is reordered. The items in stock are regularly recalculated forecasts and safety stocks. The results are then transferred to the ERP system so that the MRP or MRP run in the SAP system always calculates with the currently correct settings.
As items can change their properties, the classification is carried out regularly (at least once a month) and the rules are applied. The same applies to the optimization of forecasts and safety stocks, which are optimized and fine-tuned using a monthly simulation. The regularity of these processes is the basic prerequisite for the sustainability of the solution.
The fifth building block contributes to better communication and passing on of information. Among other things, business rules define which escalation mechanisms are to take effect. In addition, supplementary information from the market or customer area can be stored so that this can be incorporated into scheduling via sales planning.
Another package of measures is the implementation environment for the end-to-end planning and scheduling process. The following scenarios were evaluated as implementation alternatives:
- Manual implementation through the diligence of dispatchers and planners
- Implementation through programming in the SAP system
- Implementation in an AddOn system
The first scenario with manual implementation was rejected immediately, as this scenario is neither sustainable nor realistic. The second scenario was also rejected, as the SAP development team did not have the capacity or the costs were too high. The decision was therefore made in favor of the third scenario, the implementation in an add-on system. The choice fell on the DISKOVER SCO optimization tool from SCT GmbH, which had already proven its efficiency in data analysis. The license rental model for this system also keeps financing costs and investment risk very low.
Start of implementation in the branches
The measures should first be implemented in the branches. The reason for this was not only the potential mentioned above, but also the expectation that the automated set of rules would greatly relieve the branch office staff of scheduling and administrative tasks.
The activities to implement the concept were started quickly. The optimization system was implemented immediately and the standard interfaces to the SAP system were set up.
Initially, the project team concentrated on implementation in three branches as a pilot area. The regulations were set up with the involvement of the branch managers so that important additional information could be taken into account. These were, for example, the available storage space in the branches, which restricts the storage of large-volume items. Accordingly, the articles were also divided into volume classes and taken into account in the regulations.
With the start of the new system, the logistics department was faced with a certain amount of work, as the stocks in the branch were redistributed. This means that some items had to be stocked higher than before and vice versa. The “higher stockpiling” was associated with corresponding transportation to the branches, and stocks were reduced in line with demand for the articles. Items that were no longer in demand were returned to the central warehouses.
Even after training the branch staff, there was a great deal of skepticism as to whether A&K’s concept would actually work. However, once the first branches had been converted, the advantages of the solution were quickly recognized. By automatically setting the replenishment parameters for each individual item in the branches, it was possible to automate replenishment. This means that nobody has to edit BANFs or maintain master data anymore. Supplies now roll in automatically as if by magic. In addition to the inventory effects, the following point in particular had a positive impact: The availability of items is now significantly better than before. The right stocks are now stored at the right level in the branches. This not only leads to a high level of customer satisfaction, but also to a significant reduction in the workload of staff, who now have to reorder and follow up much less.
Summary
The project results were realized after a short time, and in some cases even exceeded expectations. More than 250 stores in Germany and abroad are now using the new planning concept. The DISKOVER SCO optimization tool has also already proven its worth. Helpful additional functions are also very welcome among users: The powerful and very flexible reporting is used on a daily basis. Integrated logistics controlling also provides up-to-date figures on a daily basis and can display key performance indicators over time.
The next step is now to convert the central warehouses to the new concept of end-to-end planning and scheduling processes.