The need to integrate hierarchical planning
In day-to-day supply chain management, a large number of individual planning decisions are constantly being made – sometimes with far-reaching consequences. If these decisions are depicted in a hierarchical planning model, it can be seen that they are made at different levels. The scope of the analysis and its level of detail vary considerably depending on the level. However, in order to achieve an overall planning optimum, the integration of the different planning levels and their planning processes is a decisive factor in increasing the quality of the entire supply chain.
The correct planning and control of the material flow in the supply chain is the indispensable basis for successful supply chain management. Such planning is not a one-step process, but takes place in several stages, which progress from sales planning to program and product planning to detailed planning and differ in their time dimension: A company’s strategic sales planning is the most long-term and at the same time the roughest planning level. These strategic decisions include, in particular, all those that define which markets are to be served with which products.
The finest and most short-term level is the immediate implementation level. Here, for example, decisions on machine control and system operation are made as part of detailed planning and measured values are recorded as part of production data acquisition (PDA), which can be used to adapt process models in production and for other controlling purposes. This level also includes the ‘real-time decisions’ that are made, for example, as part of order approval, workshop and transportation management or customer order management. The one – strategic sales planning – obviously has little to do with the other – machine control. And yet everything is connected. That is why we need integrated planning processes. Let’s start with sales planning.
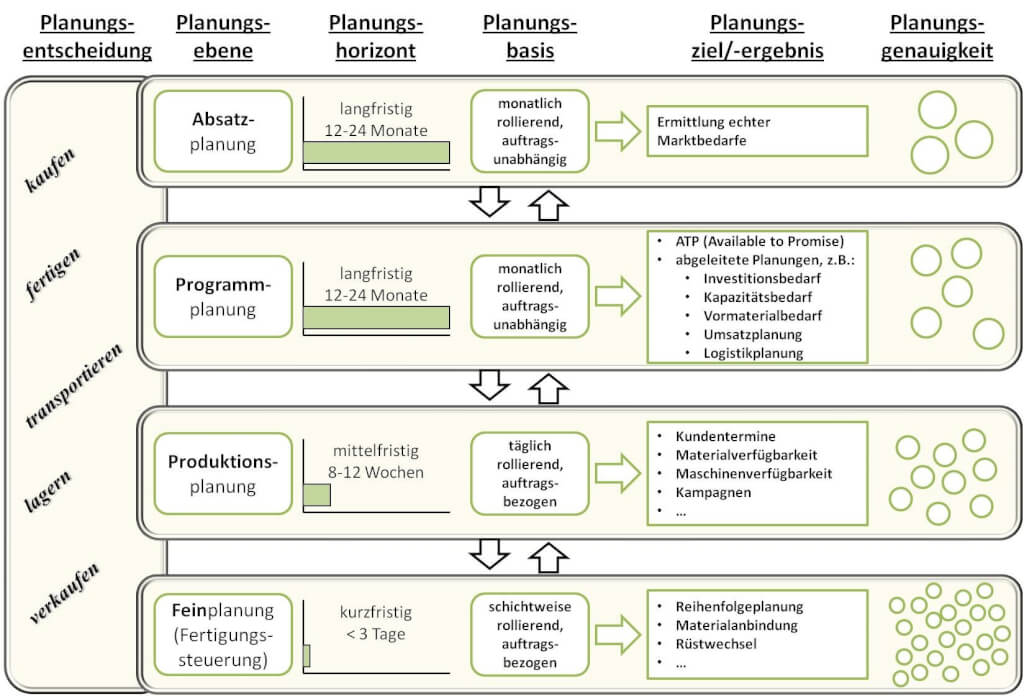
Sales planning
The aim of sales planning is to create an ‘unrestricted’ market requirements plan (with ‘real market requirements’). Such a forecast is not yet subject to any restrictions. It merely answers the question of what quantities and demand times for a product or product group a supplier should be prepared for in order to meet anticipated market demand.
The forecast is created as an integrated forecast, which usually consists of the best possible combination of a wide variety of information. Technical and statistical forecasts based on past consumption are combined with information from the sales department, e.g. on ramp-ups, run-outs, campaigns, projects, new / lost customers, regional market changes, etc., as well as information from customers. The unrestricted market requirements plan from sales planning represents the input for program planning.
Program planning
The main objective of program planning is to create a plan that optimally balances production possibilities and forecast market demand. Decisions to be made can be summarized as follows: What, when and how much must be produced, taking into account customer agreements, capacity and material restrictions as well as inventory and capacity utilization principles?
The result of these considerations is a company-wide coordinated and communicated limited sales plan, which is then made available to the sales planning level. Only then can sales, production and detailed planning be created as further key derived planning figures.
Production planning
Program planning is followed by production planning and detailed planning. They differ greatly in the length of their planning horizon and the level of detail of their planning statements: production planning looks at a horizon of 8 to 12 or more weeks, while detailed planning often only looks 2 to 3 days ahead.
Production planning creates ‘time pots’ (day, week) and fills these with jobs (orders, planned orders). The utilization per time bucket is specified. If necessary, production planning can also plan against limited capacities. The comparison between capacity requirements and available capacity can generally be carried out using simple mechanisms or manually by the planner.
Detailed planning
In detailed planning, the solution approaches are divided into two basic philosophies: deterministic detailed planning and stochastic production flow control.
Deterministic detailed planning is intended to generate a detailed sequence of production orders and operations, if necessary down to the individual piece of a material. This sequence is intended to maximize the efficiency of resources. The resulting production plan is based on detailed rules / specifications and production conditions.
Key decisions that frequently have to be made are based on the current and planned availability of the required materials, the existing production restrictions and the scheduling strategy specifications derived from the target hierarchy, such as minimized setup time, maximized delivery readiness per work process or maximized throughput. The key outputs of detailed planning are scheduled start and finish times for each work process of a production order per material and the comprehensive visibility of detailed planning problems in the short-term horizon.
The system-supported automated creation of detailed schedules can be very complex, depending on the industry, as the production restrictions that influence the production sequence can be very diverse.
The number of determining factors in the sequence formation can be very large and the interdependencies of these factors can be very diverse. Companies often shy away from the effort involved in system modeling or question the planning result due to the complexity of this topic. Deterministic detailed planning not only struggles with the multitude of influencing variables, which can never be fully captured, but also with their dynamic changes. These two factors mean that detailed plans are often out of date by the time they are completed.
If deterministic detailed planning is to be supported by a system in such a way that good and feasible plans are created automatically, particular attention must be paid to two aspects:
Firstly, the rules for sequencing, which are stored in the system, should be as lean as possible. The key influencing factors need to be determined and their interaction defined. It should not be forgotten that a large part of the rules already exist anyway, namely in the minds of the planners. This knowledge must therefore be collected, structured and stored in the system.
The second point concerns the way in which system-supported detailed planning is introduced. During implementation, the planning steps that generate the detailed plan should be carried out quasi-automatically. The planner initiates each planning step manually and can observe the result of his actions. This serves to verify the stored rules and creates the necessary confidence in the planning results for the user at the time when the detailed plan is generated fully automatically and thus the necessary acceptance of the system.
The second detailed planning philosophy, stochastic production flow control, is based on the realization that production is a process that cannot be planned in detail, in which capacity utilization, adherence to schedules, throughput time and work in progress are only statistically related to each other.
The task of stochastic production flow control is to keep a defined circulating stock as constant as possible, especially at bottleneck workstations, by means of suitable short-term control of the order inflow or the available capacity. While it is rarely possible to regulate the inflow of orders, production companies with discrete manufacturing usually have the option of a certain degree of capacity flexibility.
Certain restrictions, such as setup sequences or a product mix, can also be taken into account in stochastic production flow control. Keywords here are Heijunka boards, sequencers and EPEI values. Numerous studies and projects have shown that a stable production control situation is achieved in the medium term if the FIFO rule (first in, first out) is consistently adhered to as the overriding priority criterion for individual production orders. Stochastic production flow control is significantly less complex than deterministic detailed planning.
Integration of the planning levels
The way in which the different planning levels are integrated is decisive for the quality of the plan. In practice, it is not uncommon for production planning to act completely independently and more or less ignore sales planning. The reason for this is often that the results of sales planning are simply unsuitable for the purposes of production planning, e.g. if they represent pure budget planning that has nothing to do with real “market demand planning”. In such a case, there is a hard cut between sales planning and the underlying planning levels. Coordination between the levels only takes place again during the order confirmation process, when Sales requests the desired delivery readiness and Production Planning has to explain why the required quantity is not available on time for a specific customer order.
In a basic planning run that is consistent across the levels of the planning hierarchy, information must be communicated in both directions of the hierarchy.
Sales planning transfers the market requirements plan against infinite capacity to program planning. Based on this information, this in turn carries out a capacity analysis at a rough level against limited capacity, which then influences various derived plans in the next step, e.g. personnel or sales planning. The results of this planning step are made available to the sales department as a plan.
Conclusion
In some industries, fully integrated hierarchical planning to achieve the greatest possible economic success is not necessarily a “must”! However, it is crucial that a company identifies and undertakes the planning effort that is necessary and justifiable in order to be able to achieve the formulated corporate goals with sufficient planning quality. The greater the number of variants – especially within a series – and the more networked the upstream production and supply chain processes, the more important an integrated planning process is.