How to successfully align the logistics strategy with the corporate strategy
How can you align your logistics strategy with your corporate strategy and develop the right logistics business model to stay one step ahead of the competition? What are the typical deficits in the logistics strategy, which fields of action do we have to deal with and which starting points for optimizing the logistics strategy are neglected in practice? I would like to explore these questions in this article.
Our project experience regularly shows that in many companies there is still great productivity and market potential lying dormant, as the logistics business model has usually developed “organically” through numerous isolated divisional measures and has not been developed consistently.
The typical deficits in companies’ logistics concepts
A company’s logistics business model determines how the five layers of a company’s internal and external value chain and the supply capability of its product portfolio are structured.
In our projects, we repeatedly come across the same hotspots where there is a need for action. These focal points are the
- Design of the planning and control model,
- the architecture of the value chain and
- the delivery capability of the product portfolio.
The delivery capability of the product portfolio
Of course, it is not up to logistics to decide on the product portfolio. However, the structure of the product portfolio in terms of sales distribution and the regularity of demand for items has a major influence on the efficiency of the value chain. In order to be as competitive as possible, supply chain management must play its part in the logistical balancing of the product portfolio. In a typical product portfolio, 20-40% of the items account for 60-80% of sales; this part of the product portfolio is unproblematic from a logistical point of view. At the other end of the portfolio, 30% to 50% of the items generate only 2-3% of sales, but require 20% to 30% of the total stock. This is where we need to start in order to keep the logistical effort to a reasonable level.
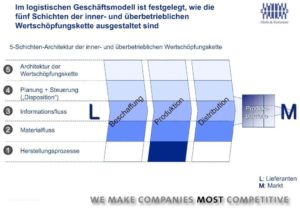
The architecture of the value chain
From a logistics perspective, the ideal value chain is one in which material with a high level of readiness for delivery is stored at a few storage levels and can be restocked with short replenishment times. The smaller the production and procurement lot sizes and the shorter the procurement, production and transportation times from the supplier’s supplier to the availability of goods in the company’s own warehouse, the closer you get to this goal. For cost reasons at least, neither batch size “1” nor suppliers around the corner can be realized.
However, many companies are not yet making sufficient use of the opportunities to reduce batch sizes and replenishment times.
The design of the planning and control model
Many companies still lack an end-to-end planning chain – from determining market requirements to production control and procurement. Work is often based too much on the original annual plan and too little on the actual emerging market requirements. For this reason, planned requirements are often overridden in production and procurement planning. You don’t follow the planned values, which you don’t really believe, and therefore don’t follow the suggestions of the ERP system, but plan manually “against the system”.
And even where the planned requirements are properly determined or provided by the customer, work often bypasses the ERP system’s scheduling suggestions because the ERP system is not set up correctly.
Ultimately, too much planning freedom at the individual levels of a multi-level distribution system leads to excess stock and an avoidable whip effect.
What building blocks can be used to create an optimal logistics strategy?
Certain regularly required solution modules crystallize in the various fields of action. These differentiate in part according to whether a company only trades or also produces, the sector in which it operates and whether it supplies directly to end consumers (B-to-C) or to business customers (B-to-B). Below you will find the building blocks, which are largely universal. Of course, not every measure is useful or necessary in every company.
Selected modules for the logistical optimization of the product portfolio
- Quarterly streamlining of the product portfolio.
- Contribution margin-oriented product adjustment
To this end, realistic contribution margins should be determined in which overhead costs are not simply allocated according to sustainability, but are based on the actual process costs. - Uncertainty-oriented product adjustment
The more uncertainty there is in an item, the lower the availability of the item should be. The uncertainty of an item can be assessed well via the required stock ranges for safety stocks. Items with high safety stock ranges should be procured on an order-related basis, sorted out or reduced in their delivery capacity. - Targeted price differentiation to support the streamlining of the product range.
Selected building blocks for optimizing the architecture of the value chain
- In production:
- Economical batch sizes:
Consistent determination of economic production lot sizes, whereby only the variable costs should be taken into account and not full costs. - Group Technology
For AB/XY parts, consistent machine allocation according to setup groups. For all other parts, procure equipment that is as flexible as possible in terms of setup, not necessarily equipment that is efficient in terms of unit time - Systematically identify and eliminate bottlenecks
- Consistent logistical positioning
Depending on the desired compromise between throughput time, capacity utilization and average adherence to delivery dates at a plant, the required average stock level must be determined statistically and consistently adhered to. To achieve this, any necessary adjustments to production capacities or the flow of parts must be recognized and implemented in good time. - Consistently compensating for uncertainties in the value chain.
Identified uncertainties should be eliminated where possible, otherwise buffered by safety stocks or production flexibility. - 80/20 leveling
Differentiated adjustment of the logical end coupling points for regular and irregular parts. Regular parts can be buffered via warehouses and thus occupy lower-ranking capacity, which is then available for irregular parts that are not stored but are quickly produced.
- Economical batch sizes:
- In procurement:
- Clean coordination of technical and organizational processes between customer and supplier.
Sometimes even slight technical modifications to a product requirement are enough to reduce costs and replenishment times. - Consistent VMI:
Introduction of VMI processes to give suppliers more flexibility while improving their ability to deliver. - Consistent reduction in replacement times
Coordination of prefabrication stages and advance procurement with the suppliers; selection of more expensive but close substitute suppliers for a small part of the basic requirements and the peak requirements.
- Clean coordination of technical and organizational processes between customer and supplier.
In this article, I could only touch on the building blocks for optimizing the logistics business model and thus improving competitiveness, and had to concentrate on the more general aspects.
Overall, we often find that many companies do not pay the necessary attention to logistical aspects. Logistics services are expensive, are not paid for sufficiently by customers in most cases and can quickly eat up a company’s earnings. If you look at the developments in online retail, you get the impression that the battles are won with the product portfolio, but the war is sometimes lost due to the cost of logistics. Initial improvements can be achieved quickly. A supply chain check-up quickly identifies the key solution approaches. Then they have to be worked through systematically; but those who start today will finish faster than the competition, who will sleep until tomorrow.