Best practice rules for the production kanban, part 2:
Plan layout and handling
In part 1 of the best practice article on the production Kanban, we gave you an introduction to the topic:
- When does it make sense to integrate a production Kanban into your own production processes?
- At what point should you do this?
- What basic requirements must be met in advance?
We will now move on to the practical factors that need to be considered when introducing Kanban and start quite mundanely with
Basic principle 10: More kanban types give a better picture of the demand situation
The circulating stock of parts in a Kanban system is determined by:
- average consumption per unit of time,
- the regularity of demand,
- the required degree of delivery readiness and
- the required production lot size.
The number of Kanban containers required then depends on the number of parts that fit into one container. You need fewer large containers and more small containers.
Each container requires handling effort. This seems to speak in favor of using the largest possible containers. However, as the weight of a container increases, so does the force required and the technology to be used, and therefore the handling costs, which ultimately argues in favor of several small containers rather than a few large ones.
Another criterion speaks in favor of using smaller containers, which is at least as important as the aspect of container weight and handling effort:
The more containers circulate in a Kanban control cycle, the better the “preview effect” for the supplying area.
The supplying area can estimate when the yellow and red areas will approximately be reached by looking at the growth of the card stacks in a collective kanban system. This helps to document the order sequences at the production capacities with foresight.
Ideally, around five kanban containers are grouped together in the collective kanban to start a production order.
In practice, however, you often have to adjust to the reality of the available container sizes. And if the production batch sizes can be continuously reduced through set-up optimization measures, then it is not possible to continuously replace the Kanban containers or reduce the physical fill level of a container further and further. The parts per container must also fill it to some extent, otherwise too much storage volume is wasted.
Many companies fear having to circulate too many kanban types with smaller kanban containers. You don’t need to worry about this: the number of kanban types in a control circuit is not critical. More critical can sometimes be the number of kanban-controlled items that the supplier has to re-produce. If there are too many material numbers, the overview in a physical kanban board can be lost. An electronic Kanban can handle a large number of Kanban parts better than traditional solutions.
Best Practice Module 10: In a professionally designed production kanban system, the circulating stock of the kanban control cycle is distributed to as many kanban containers as possible. Rule of thumb: Five well-filled Kanban containers are ideal for one production batch.
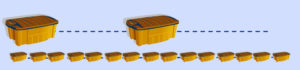
Basic principle 11: A material flow digests small batches better
Production batches are congestion levels in the material flow that need to be ground consistently and continuously. With a batch size of 1, the material flow would be much more even and the whip effect in the production chain would be significantly reduced.
Even if batch size 1 is not feasible in many manufacturing processes for economic reasons, the pressure to reduce batch sizes should be maintained.
The production kanban system can make a contribution here that successful companies cannot do without: the standard production lot size should always be set to the “red area” and not to the beginning of the “yellow area”. If production is already started in the yellow area for reasons of sequence planning or capacity balancing, the corresponding batch size is below the standard batch size. The compromise of being allowed to start production before the actually defined replenishment threshold of the red zone is reached should be “paid for” with the batch size compromise. This creates a certain amount of pressure to further reduce the economic batch size.
If you take the opposite approach and set the standard batch size to the beginning of the yellow area, this allows production to increase the future average production batch size.
Best practice module 11: In a production Kanban, the red area is at the economic batch size and the yellow area is below.
The right kanban concept
Basic principle 12: A picture says more than a thousand tables
The original Kanban mechanism consists of a purely manual cycle without a connection to an ERP system, which works with cards and Kanban boards into which the cards are mechanically inserted. A clear advantage of this mechanism is the simple and clear visualization of the demand situation for the supplying agency. However, a purely mechanical kanban system has one major disadvantage: it leaves no “electronic traces” in the ERP system. It can therefore neither be synchronized with other ERP-controlled scheduling processes nor can the Kanban control loops be monitored centrally.
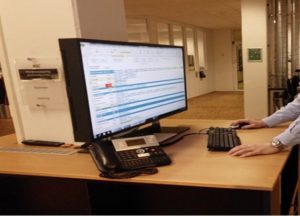
The digital version of a Kanban solution is an electronic Kanban. The entire Kanban control loops are managed in the computer here. Corresponding solutions are available as modules or functions of various ERP systems.
Normally, electronic kanban systems also work with physical cards, as each kanban container must be labeled. The status of the container, e.g. whether it is full or empty, is communicated to the electronic Kanban system by scanning a barcode or reading RFID information. In the electronic kanban system, the cards and their “operating states” are managed in the computer. When a collective kanban is triggered, the cards are printed. Later, the cards of empty containers are scanned again and then destroyed, as they can now be found in electronic form in the Kaban software. Some companies also keep the blank scanned cards and retrieve them from the drawer when the yellow or red area has been reached instead of printing new cards.
The electronic Kanban eliminates the disadvantages of purely manual Kanban solutions. It simplifies the management of the control loops and enables central monitoring of the Kanban control loops using key figures. When re-sizing control loops, nobody in production has to remove surplus cards from kanban boards or insert new cards.
However, an electronic Kanban also carries the risk of inadequate visualization if a graphical replica of a physical Kanban board is not used.
A key success feature of a kanban system is the visualization of the demand situation for the supplying point of a kanban control cycle. You cannot achieve this visualization with number tables. Only graphically prepared electronic kanban charts provide a clear overview. Solutions that actually display cards and stack them on the screen come closest to the original idea.
If you want to do without a mechanical kanban board and prefer a display on the screen, please do not save money in the wrong place. A 15-inch screen does not enable meaningful visualization. For the price of a physical planning board, you can afford at least a 70-inch flat screen!
Best Practice Module 12: Large-scale visualization beats convenience: Experienced Kanban companies attach great importance to the large-scale visualization of the demand situation in a Kanban system. It is better to manually insert cards than to comfortably wander around in the information fog of electronic solutions without graphic Kanban visualization.
Basic principle 13: Modern leadership takes place at the scene of the crime.
In the Toyota production system, the term “Gemba” is used. This Japanese term is perhaps best translated as “crime scene”. As avid crime readers and watchers, we know that investigating crime scenes is essential for the detective. The detailed documentation of the crime scene by forensic technology can never replace the inspection of the crime scene. A lot of additional information is recorded at the crime scene, which completes the impression. Even with the most careful documentation, only part of the information that makes up the crime scene can be recorded.
The same applies to a decentralized control system, such as that created by a Kanban system. The people on the ground, the people at the scene of the crime, know and grasp many connections that are difficult to make out from a desk. This also – and already – applies to the desk of the foreman or production controller. A kanban board belongs at the place of action of the supplying, post-production location and not in the foreman’s office, regardless of whether it is a physical kanban board or an electronic version.
In any case, the board must be large enough and positioned in such a way that it is visible to the public. The secret knowledge of the foreman or production controller is a thing of the past – Kanban takes place in public. This publicity is part of the checks and balances that help to ensure that the system functions reliably and that the rules are adhered to.
Best practice module 13: A kanban board – both mechanically and electronically designed – belongs in production and not in the foreman’s office.
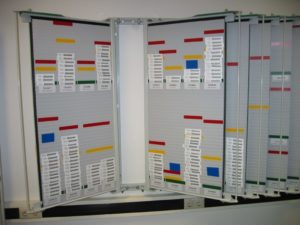
Basic principle 14: It is rarely economical to separate kanban parts and conventional parts in terms of production technology.
In companies with a typical product structure, 40% to 80% of production capacity is occupied by 10% to 30% of regular production parts (AB/XY parts). The remaining 70% to 90% of the material numbers only have irregular requirements and occupy the remaining production capacity. If you convert the AB/XY parts to Kanban and continue to control the remaining parts conventionally, you will hardly succeed in assigning separate production areas and systems to the two groups of parts.
Separating the production of kanban parts and conventional parts would require overcapacity in both segments and would therefore not be economical. We regularly come across companies that assume that kanban parts must be manufactured in separate kanban production. As this is not economically feasible, they unnecessarily forego the introduction of Kanban.
Although the operation of a kanban system ideally requires reserve capacity or, alternatively, supplementary leveling measures, it does not require the physical separation of production areas in kanban and the rest of the world.
Best practice module 14: In efficient Kanban solutions, kanban-controlled and conventionally controlled articles largely use the same capacities
Basic principle 15: If nothing is pulling, nothing is being pushed.
The magic of a kanban system lies in market-synchronized production. Nothing should be produced in advance if there is no demand.
However, absolutely consistent, demand-synchronized production requires great flexibility in production in order to cope with fluctuations in demand. This flexibility costs money, as it can usually only be achieved through reserve capacity or additional shifts in the production facilities and a higher number of permanent staff and temporary workers.
As far as personnel are concerned, a certain degree of flexibility can be achieved by assigning employees to other workplaces and using flexitime and working time accounts.
The yellow area in a production kanban and the leveling of production using a heijunka mechanism also allow the demand side to be smoothed out somewhat.
However, it happens from time to time that all these balancing mechanisms are not enough and there is a risk of idle time for employees and underutilization in production. The company then quickly calls for pre-production. However, a professionally designed kanban system must be able to withstand temporary idling by employees. Pre-production beyond a clearly defined leveling mechanism is not an adequate response. It leads to overstocking, can at best postpone underutilization, because at some point the excess stock has to be reduced again, and carries the risk that fluctuations in capacity utilization in production will continue to increase. There is therefore no way around it in professional kanban systems:
Best practice building block 15: A consistent kanban system must be able to withstand occasional idling by employees.
Correct introduction
Basic principle 16: Convince before force.
The introduction of a kanban system will not only be met with enthusiasm. The reservations about a pull system are manifold and deeply rooted. We have repeatedly found that foremen in production in particular are wary of kanban systems. Behind this is the doubt as to whether such a pull system can actually work and is so much more effective than a classic control mechanism.
Sometimes there is also the uncertainty of “having to” decide on the next order to be produced within the framework of decentralized control and no longer being given instructions by a production controller.
If we encounter such reservations in the preliminary discussions, we recommend conducting a business game to prepare for the Kanban introduction.
Various business games are offered on the market. We like to use a business game in which, over the course of two days, we simplify the production processes step by step based on a planned production according to sales specifications and change the control principle.
While the participants do not fulfill the specified production plan at the beginning despite great stress, by the end of the planning game they succeed remarkably quickly and easily using Kanban.
Best practice module 16: A simulation game can be the beginning of a wonderful friendship between users and a kanban system.

Basic principle 17: The master is always right.
When designing a kanban system, you eventually reach the point where you need to discuss the calculated control loops with the foremen or area managers of the various production areas. The contact persons often doubt that the control circuits are sufficiently dimensioned. What happens if several parts that have to be produced on the same machines turn “red” at the same time? The abstract statement that this rarely occurs in practice and can be intercepted by the defined yellow areas and the safety stocks in the individual control loops is often not enough to dispel reservations.
In these cases, agree a lead time with the foremen by which you extend the replenishment time of the control loop and which is defined in such a way that the foremen are convinced that they will be able to produce the parts on time. Record this lead time separately from the actual replacement time. The lead time does mean that you need to build up a little more stock than your control cycle actually requires. But you have the master on your side. By negotiating a lead time, sometimes like at a bazaar, the master has committed himself to ensuring that the kanb shares in the supermarket/kanban shelf can be replenished in good time.
If the kanban system is running, you will be able to tell from the monitoring of the replenishment time whether the lead time is required. If it is not necessary, you can continuously reduce it in consultation with the masters. If, exceptionally, it should actually be necessary, you will have benefited from the master craftsman’s experience. The aim must be to continuously eliminate unnecessary lead times.
Best Practice Module 17: Better “lead times” than reservations: A successful Kanban introduction takes the reservations of the foremen who will later have to live with the Kanban system seriously. Additional security in the control loop in the form of a “lead time” can dispel reservations. The lead time must be documented separately and must not be hidden in the replacement time in order to precisely separate clean control loop calculation and subjective safety perception.
Basic principle 18: Reducing inventory is good, but readiness to deliver is better.
Decide spontaneously: In the first four weeks since the go-live of a kanban system, how do you measure its success: by the availability of parts or by the reduction in stock? If you’re like most, you’ll initially prioritize parts availability over inventory reduction. The fact that it takes time for stock to run out is more readily accepted than the fact that it takes time for sufficient stock to be built up in a new kanban control cycle.
To avoid any doubts about the potential success of a new kanban system in the first place, you should never start “from an undersupply”. If possible, only convert a part to Kanban once you have built up the necessary supermarket stocks. If a kanban control cycle is not able to deliver as planned, doubts quickly arise about the reliability of the entire system.
Kanban control cycles with initial overstocks are not a major problem. If you have selected the right range of parts for your kanban system, the excess stock will flow out quickly.
Best practice module 18: Front water against Kanban haters: Companies that have experience with the introduction of Kanban systems always start their control loops with sufficient stock or from excess stock.
Despite the focus on delivery readiness, a kanban system is rightly expected to be able to significantly reduce stocks. This is almost always correct, because
Basic principle 19: 30% is usually possible.
Experience shows that a well-established kanban system can save 30% on stock. At first glance, this may seem surprising. A properly structured, plan-controlled scheduling system should actually be able to manage with fewer stocks than a kanban system.
This consideration is essentially correct. Provided that parts with regular demand are properly planned and all disturbance variables have been eliminated, a stock level can be realized that cannot be achieved with a kanban system. Just-in-time production represents such a precisely designed, plan-controlled disposition. Since not all disturbances can be avoided in practice with reasonable effort, empirical evidence shows that significant stock reductions can be achieved with kanban systems.
Two further effects also contribute to the inventory benefits of a kanban system:
- Kanban systems are insensitive to booking errors, because a kanban system is controlled according to the physical stocks. If a box is empty, the kanban card is returned to the supplier; inventory differences between book stocks and physical stocks do not interfere with a kanban system.
- Kanban systems also generally do not suffer as much from the dubious inventory limbo that takes place in many companies at the end of the financial year or even quarterly. On the one hand, because it is more complicated in kanban systems to reduce stocks in numerous control loops in order to massively increase them again shortly afterwards, and on the other hand, because kanban control loops are more sensitive with regard to their ability to deliver.
Best practice module 19: In order to fully exploit the potential of inventory reduction, successful Kanban companies attach great importance to a careful and sustainable Kanban introduction. A key success factor here is the consistent elimination of disruptive factors.
Basic principle 20: Think first, then act.
When Filippo Brunelleschi began building the dome of Florence Cathedral in 1420, he did something radically new for his time and became a pioneer of modern work organization: he separated planning from execution. This was the only way he was able to realize the most massive dome construction since antiquity.
The principle of first thinking things through to the end and then implementing them has since established itself in the world – and also among good craftsmen.
So why do many Kanban implementation projects start by selecting an initial pilot control loop and diligently laminating cards? There seems to be a great fascination with laminating the kanban types.
Even if a Kanban introduction is not a millennium achievement, it makes sense here too to separate planning and execution.
The first step in designing a kanban system is to check and correct the master and movement data required to calculate the control loops. After that, the first step is to dimension the entire control loops.
The calculation of the control loops is the starting point for the design of the entire Kanban infrastructure: starting with the required size of the supermarkets, the required area of manual Kanban boards and the determination of suitable container sizes, through to the calculation of the required number of Kanban containers and the verification of capacity utilization
Best practice module 20: Study before laminating: A successful Kanban introduction initially has a lot to do with calculation and thinking and little to do with laminating cards.
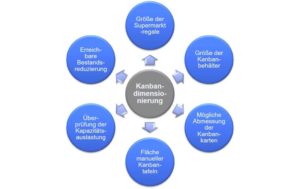