Meissen optimizes scheduling with DISKOVER from SCT
Manufactory with state-of-the-art production control
By Andreas Capellmann and Sophia Strathmann et al.*
While large industrial series manufacturers are currently preparing to use Industry 4.0 technologies to move towards batch size 1 in line with customer requirements, this has been the program at manufactories such as Meissen for centuries. Meissen is now working on significantly accelerating throughput times and increasing delivery readiness across the entire portfolio. The use of SCT Supply Chain Technologies’ advanced planning and scheduling software DISKOVER has already enabled major progress to be made.
Porzellan-Manufaktur Meissen, Europe’s first porcelain manufactory, has stood for unique craftsmanship and exclusive aesthetics since it was founded in 1710. MEISSEN® is one of the oldest and internationally best-known German brands, unmistakably recognizable by the hand-painted crossed blue swords that can still be seen today. The creations embody a special beauty and sensuality beyond purely functional designs and thus become an expression of a special attitude to life. And those who love this attitude to life even benefit from a demonstrably high intrinsic value and top-class service: almost every product that has been manufactured since 1710 can still be ordered today.
Mastering economic challenges
Despite this outstanding market position, Meissen has had to overcome major challenges in recent years. In the context of a strategic reorientation, scheduling should now also be optimized. The aim was to reduce throughput times and increase availability in order to ultimately increase sales potential and customer satisfaction.
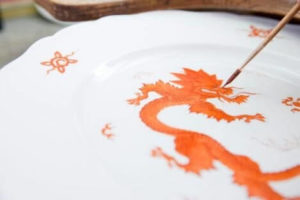
Optimize material flow to reduce throughput times
The starting point for the organization at the time was an order processing system based on Oracle. It allowed the process organization of the manufactory to be managed very efficiently. However, it was not possible to control the associated material flow and the associated throughput times and storage levels. The effect was that the throughput times for products were very high; and if you wanted to achieve a high level of delivery readiness, this inevitably led to a large stocked range with high stocks of finished goods. Order-related production had to be managed in parallel with the stocked product range. Customer needs have changed considerably over time. Today, online retail educates customers to the effect that products can be delivered within 24 hours. This places completely new demands on manufacturers in particular, because a high level of delivery readiness with short waiting times is a demanding challenge for their production processes.
Highly complex production processes
Consequently, a solution had to be found to efficiently organize the material and goods planning and its storage stages. The requirements were high. On the one hand, Meissen has a very large, active, historically grown product range that needs to be managed efficiently. It is therefore necessary for the system to automatically create production proposals for individual products according to defined rules, even across product clusters. On the other hand, Meissen also has very complex processes. Every product has individual requirements. In addition to at least two firing processes, there are various types of painting and finishing, which involve several work processes. However, the required scheduling system had to be able to transfer the progress of production unfiltered from the Oracle system and manage it efficiently. At the same time, the system should also be able to handle several intermediate storage levels in order to better balance the production loads. It also had to provide interfaces for sales in order to incorporate the order system and sales forecasts into scheduling.
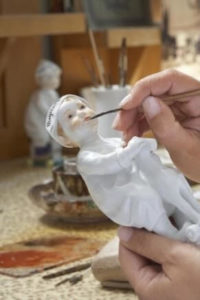
© State Porcelain Manufactory Meissen
APS system halves throughput time
Today, the Advanced Planning & Scheduling (APS) system DISKOVER from SCT Supply Chain Technologies is used, with which Meissen has managed to roughly halve throughput times within a year, reduce stocks in the finished goods warehouse accordingly and still increase delivery readiness across the entire stocked range. Customer orders are now also processed more quickly, as the material flow can now be planned much more transparently.
For example, APS tools offer much finer, range-oriented forecasting functionalities than ERP systems for improved planning and can therefore predict actual demand much more accurately. The functional scope of DISKOVER SCO includes, for example, range-oriented forecasting procedures as well as functions for portfolio analysis and the integration of sales forecasts. It can therefore map reliable and comprehensible planning processes. However, APS solutions not only help with such planning processes. They also support dispatchers in their daily work. SCT’s APS tool is characterized by extensive simulation mechanisms that run automatically in the background and continuously optimize planning and scheduling settings and decisions. In this way, even technically and professionally less experienced users benefit from the high forecasting accuracy and planning precision – and the companies benefit from sustainably reduced inventories while at the same time ensuring the necessary readiness to deliver. Overall, dispatchers can therefore plan better with less effort, which in itself is an advantage of APS solutions.
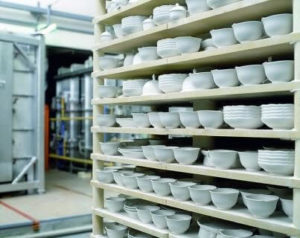
Further detailing of the production control system
The live connection of DISKOVER SCO took around a year for the stocked items due to the highly complex interface and the many special features that had to be mapped in the process. After a further six months, order-related production was also mapped. During this time, all products were recorded with all their master data and scheduling parameters, the interfaces to the Oracle and order system were adapted and the process organization was optimized so that real intermediate storage levels were also created to take the pressure off the material flow chain and reduce the costs of products in stock. Once the introductory phase is over, the next step would be to dovetail capacity planning even better with scheduling. The varying complex processes of the current orders must also be taken into account here. The matching of available personnel and product-related production capacity should already be plannable during scheduling. to be able to calculate delivery times as accurately as possible.
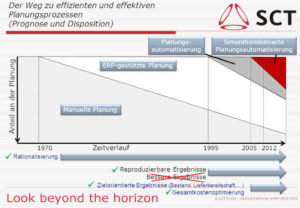