Consolidation of the disposition
by Andreas Capellmann (SCT GmbH) and Dr. Reiner Schmitz (WM SE)
If you want to plan millions of products efficiently today, you no longer need hundreds of employees to look after individual suppliers or product groups. What is needed are management systems that enable largely automated scheduling. WM SE relies on DISKOVER from SCT across all locations and ERP systems.
WM SE supplies independent garages, authorized workshops, specialist dealers and franchised dealerships in seven countries from around 250 locations. The customer satisfaction of the approximately 60,000 active customers is the top priority for the approximately 6,500 employees of the Osnabrück-based group of companies. To ensure this customer satisfaction, WM SE must guarantee its customers same-day delivery. This is no easy task with over 250,000 items available daily and several million SKUs (Stock Keeping Units)!
High delivery readiness
Customer expectations are very high. “A delivery availability of 24 hours is far too little; anyone can do that,” explains Dr. Reiner Schmitz, Head of Central Scheduling South at WM SE. “If a car is on the lift in the garage and a spare part is missing, same-day delivery is essential, preferably within 1-2 hours. So we drive to our customers around three to five times a day.” As far as possible, all items that are needed on a daily basis must therefore be stocked at each location. However, it is also important not to store too much, as this ties up capital and costs money to maintain capacity – from the purely physical space and administrative requirements to insuring the assets and financing the inventory. But how do you manage to keep these immense numbers of items for hundreds or even thousands of vehicle models in stock so that you only have what is needed at any given time?
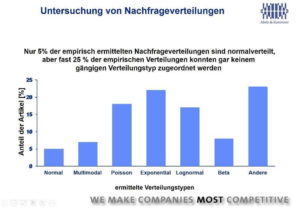
Big database and dashboard in one
An immense amount of data has to be processed every day and then used efficiently. First and foremost, dispatchers need access to all warehouse movement data. Ideally in real time, which currently means “daily” for central scheduling. However, the flood of information must also be appropriately filterable in order to be able to manage the largest possible number of articles as efficiently and automatically as possible. With several million SKUs, a dispatcher cannot look at every single item in detail. Nevertheless, he always wants to be able to do this in case of doubt. It must therefore be possible to jump directly from any level of aggregation to the viewing level of an individual article. Complete access to this “big data” of scheduling is therefore absolutely essential. Solutions that only provide aggregated data in management dashboards are nothing for Schmitz: “Dispatchers must be able to evaluate and subsequently process the data of millions of products in one go. Jumping back and forth between different systems or doing it manually makes no sense. We work with special consumption figures and key performance indicators, which we evaluate regularly and from which we then derive our action requirements. A break in the system would be an absolute hindrance here.”
Comprehensive ERP system use
Some of these tasks can also be implemented with extended function modules of ERP systems. The company WM SE, which operates many locations and distributed warehouses, has also historically grown a heterogeneous ERP landscape. Schmitz was therefore looking for a solution for the scheduling management system that could be integrated into a wide variety of company structures and could manage data exchange with the installed heterogeneous ERP systems. Implementing the entire central scheduling tasks with heterogeneous ERP systems with just a few schedulers would be a much more complex undertaking. The same problem would arise as with separately operated operational and analytical scheduling solutions: Data from different systems would have to be compiled and harmonized in order to then evaluate it and ultimately process it further in the respective system – and, if possible, with the aim of achieving an overall optimum. With a single integrated scheduling management system for analysis and operational scheduling that harmonizes transparently with all ERP systems in use, which are currently being installed step by step at all of WM SE’s more than 250 locations, scheduling is much easier.
30% increase in efficiency
“The functional scope of the DISKOVER scheduling management system from SCT, which has been in use at WM SE for some time, is comprehensive. We save around 30% of the effort that we would have if we only had one ERP system with the associated supplementary reporting and analysis tools, as we can go directly into individual processing from a bird’s eye view of the KPIs. However, as we have three ERP systems, the efficiency gains achieved are even greater,” explains Schmitz. DISKOVER is therefore also ideal for companies that have a heterogeneous system landscape as a result of mergers and acquisitions.
With DISKOVER, Schmitz has succeeded, for example, in automatically comparing all data with all distributed ERP systems on a daily basis and almost completely dispensing with external evaluation programs. Extensions to individual functions can also be proposed to SCT for provision. Thanks to DISKOVER’s modern program technology, they can be implemented quickly and are also useful for other users if they are implemented as part of DISKOVER’s continuous delivery model. The Java-based structure of the program is modern and practical: data can be sent from the program as an e-mail, for example, and it is also possible to download evaluations in Excel format, so that even the last 5% of special evaluations can be run using such simple functions.
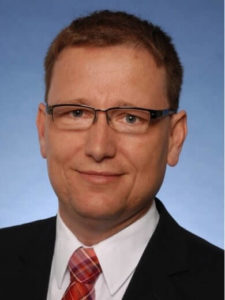
“We use DISKOVER to consolidate our scheduling for over 250 locations with three different ERP systems and enable largely autonomous scheduling via rule sets. DISKOVER is also an excellent reporting tool that enables us to drill down from the KPI to the individual item level, even with more than 10 million stock-keeping units. This is extremely efficient,” explains Schmitz.
Internal benchmarking completed
DISKOVER was already in use at TROST Fahrzeugteile, which was acquired by WM SE in 2016. With the integration of Trost into the WM SE group of companies, the question has arisen in recent months: Is the tool also good for WM SE or should WM SE’s MRP system be used? It was decided that Trost’s ERP landscape would be consolidated and that scheduling at WM SE would be handled uniformly via DISKOVER in future. In addition to the 140 Trost warehouses to date, 110 more warehouses have now been added, of which around 70 locations are already equipped with DISKOVER. “We carried out comprehensive benchmarks internally and the SCT GmbH solution was chosen because of its really convincing features,” explains Schmitz, who is visibly happy with his decision to choose DISKOVER around six years ago. After all, the results are what counts in the end.
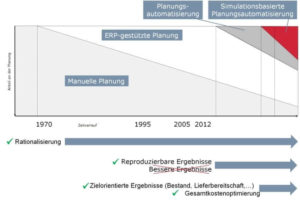