by Götz-Andreas Kemmner and Gerrit Sames[1]
Although scheduling is a central function of a company, even today, in “Factory 3.0”, it is still underdeveloped. Without a more efficient scheduling system, it will not be possible to realize an integrated Factory 4.0. However, the foundations for a more modern, efficient and further automatable scheduling system have been laid and are already being used by technology leaders. So rescue is near.
We are on the cusp of Factory 4.0 and most companies are trying to push the level of digitalization even further. Material planning, both in procurement and in production, will remain a central function in Factory 4.0. At a superficial glance, one might get the impression that scheduling has already come a long way in terms of IT technology; who still plans by hand today? ERP systems, merchandise management systems or PPS systems are used everywhere. However, if you take a closer look at the scheduling processes, you realize that in many companies scheduling is still done “by hand”, disguised to a certain extent by an IT system.
In some cases, “MRP lists” are still taken from the ERP system and the dispatchers decide on order dates and quantities themselves. Although the scheduling suggestions often come from the ERP system, the users overwrite the suggested order dates and quantities massively.
The main reason for this shortcoming is the data quality of ERP systems, which is expressed in two dimensions. On the one hand, master data is missing, incorrect or outdated and, on the other hand, the scheduling systems are not parameterized correctly.

Although many managers recognize that the data quality in the ERP system is not satisfactory, they still doubt that much can be achieved by readjusting scheduling parameters. However, the correct or at least improved setting of the disposition parameters is not about tuning an engine that is already sufficiently powerful and then trying to tease the last bit out of it, but about getting an engine to run properly in the first place. The following practical example from an international production company may illustrate this (see below).
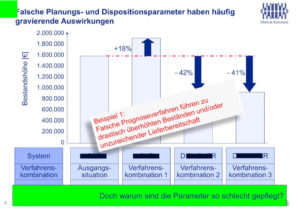
This example shows how drastically different process settings can affect stocks and delivery readiness. The aim of the division was to ensure 95% delivery readiness to the market. The stocks required for this should be kept as low as possible. As the figure shows, by adjusting the ERP system’s scheduling parameters appropriately (process combination 1), it was possible to adequately ensure delivery readiness, albeit at the cost of an 18% higher inventory level. Thanks to further optimizations, supplemented by extended scheduling and forecasting functionality, the required delivery readiness was ultimately achieved with 40% less stock (process combination 3).
It doesn’t take much vision to realize that the challenges facing scheduling will continue to grow. The time available to dispatchers for data maintenance will inevitably become less and less; demographic trends alone will lead to an increasing shortage of the necessary personnel. But what is probably even more decisive is that users’ understanding of the effects of dispensing parameters is very limited, especially as even proven experts can no longer reliably understand their complex interaction. Ultimately, ERP systems generally do not provide suitable tools for optimizing scheduling parameters.
Let’s take a closer look at the barriers to digitization in scheduling:
Obstacle 1: Conventional maintenance of scheduling parameters is far too time-consuming.
A simple calculation example makes this clear: An MRP controller is responsible for (only) 1000 articles and concentrates on maintaining the 10 most important MRP parameters. This should be checked four times a year, i.e. every three months. It is certainly no exaggeration to assume a test duration of at least 60 seconds per MRP parameter, as each material number must be called up, the masks with the required parameters must be loaded and the correct setting must be considered or looked up. These specifications result in a required maintenance effort of 666 hours per year. This corresponds to approx. 40 percent of the annual work capacity of one person.
The complete maintenance effort is even greater: in powerful ERP systems, far more than just 10 scheduling parameters can be set for each material number. In the SAP system, for example, over 130 parameters can be defined for each material if required; this does not even include settings for historical values, quotations, scheduling agreements and contracts. Of course, nobody needs that many settings for an article at the same time, but in practice there are always far more than 10.
Obstacle 2: Conventional maintenance of scheduling parameters does not deliver reproducible scheduling results.
Every practitioner is aware of this effect, but most companies do little to counteract it. Every user weighs facts differently, behaves differently and only has an overview of part of what is happening. With every vacation or sick leave replacement, with every change of personnel, the disposition world of the affected articles changes, which in turn has an impact on all subsequent disposition levels.
Obstacle 3: Conventional maintenance of scheduling parameters does not deliver economically optimized results.
Economically optimized scheduling results cannot be achieved by gut feeling, because the interaction of the various scheduling settings is extremely complex. Ultimately, it is about statistical effects and statistical correlations between parameter settings and economic results that even specialists can no longer foresee in all their implications.
At first glance, it seems difficult to achieve correctly set disposition parameters under these circumstances.
Smart data analytics opens up broad opportunities for scheduling 4.0
Heinrich von Pierer, the former CEO of Siemens, is credited with the bon mot: “If Siemens knew what Siemens knows”. The same applies to our ERP systems. Most companies are not even aware of what their ERP system knows; what an enormous pool of knowledge can be drawn from the collected data pool to optimize scheduling if you only have the right tools.
One such analysis tool is the DISKOVER SCO system. The system is able to use the extensive databases of an ERP system to determine optimized parameter settings by means of simulation and to continuously readjust certain scheduling parameters. Simulation approaches are used in many areas today. Vehicle bodies are ‘crashed’ in the CAD system during development and optimized based on the simulation results. The same applies to the development of molds for shaping production processes such as casting, forging or injection molding. In these cases, too, the flow of the material is simulated during injection into the mould in order to optimize the shaping.
Using simulation to optimize scheduling parameters and master data is therefore an obvious approach. If you don’t want to settle for kitchen scheduling, it’s practically the only way to get to the bottom of the complex interaction of scheduling parameters.
Simulations are used to check how certain combinations of scheduling parameter settings affect the efficiency of the scheduling results. The system ‘crashes’ the scheduling in the computer, so to speak, before the parameter settings are implemented in practice.
Although DISKOVER SCO can already optimize some parameter settings automatically. The simulation process does not yet replace the expert who has to interpret the simulation results and draw conclusions from them. However, optimization processes are drastically accelerated, risks are significantly reduced and far better quality results are achieved. On the one hand, the simulation results can be mapped in scheduling rules and, on the other hand, particularly dynamic parameter settings, such as safety stocks or forecast values, can be directly readjusted using simulation processes.
It is also very interesting that it is possible to check directly for each individual item and material whether the required delivery readiness levels can be met in practice and what average stock levels can be achieved.
The basic data analysis and simulation process can be divided into four steps:
By transferring extensive master and transaction data from the ERP system, the entire value stream and the planning and scheduling process are mapped in the simulation system (step 1).
Simulations can now be used to compare different combinations of MRP parameter settings and scheduling strategies according to logistical and economic criteria such as achievable delivery readiness, average stock levels or inventory and ordering costs (step 2).
In order to simulate the effects of alternative scheduling settings for different article groups, scheduling parameter settings or entire sets of rules to be tested are transferred to scenarios in the DISKOVER system and fed into the simulation process. The results can be viewed directly in DISKOVER as an overall result for all articles as well as for each individual article in order to obtain information for optimization approaches. In this way, different alternative courses of action can be played through and compared with each other (see below).
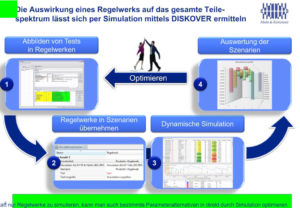
The result of the data analyses is not only information on the correct parameter settings in the ERP system, but also strategic insights and organizational rules, which will not be considered further here, although they can be of great importance for a company’s logistics business model.
Of direct importance for scheduling 4.0 is how the knowledge gained on the correct setting of scheduling parameters can be applied effectively and efficiently in practice:
The findings, with which settings, under which boundary conditions, optimized stock heights, ranges of coverage resp. The levels of readiness for delivery achieved are stored in decision tables and sets of rules (step 3).
“Dispo manuals” or simple work instructions do not do justice to these regulations. This is not only because it would be far too time-consuming for users to look up the rules in order to maintain the data. More importantly, the regulations are based on a large number of different material classifications that have to be constantly recalculated and without which the regulations would not work.
The DISKOVER system therefore optimizes and feeds the results back into the ERP system automatically on a daily basis or at selectable times (step 4).
Systems that specify the current scheduling parameter settings to the ERP system and thus optimize logistics performance can be regarded as “ERP performance management systems” or simply referred to as “scheduling 4.0 systems” (see below).
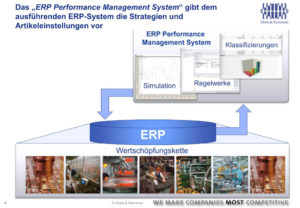
the strategies and article settings
Such an ERP performance management system / Dispo 4.0 system readjusts the parameter settings in the ERP system. It must
- transfer a wide range of master and transaction data from the ERP system;
- carry out numerous item classifications and key figure determinations;
- rules and decision tables;
- have extensive simulation functions, and
- return the setting specifications to the ERP system.
There are already various solutions on the market for classifications and simple sets of rules. Today, the wheat is separated from the chaff when it comes to simulation functions.
The procedure presented eliminates the need for manual maintenance of scheduling parameters and improves the quality of the scheduling proposals. If the dispatchers are less frequently forced to adapt the IT system’s dispatching suggestions, dispatching results become more reproducible and, since the dispatching parameters have been specifically optimized for the most economical value chain possible, more effective dispatching results are achieved. Ultimately, this increases the degree of automation in replenishment, as the proportion of items that can be replenished automatically increases significantly.
How far automation can be taken depends mainly on the level of detail of the scheduling rules developed.
Even if the market is still thin on the ground, ERP performance management based on “Smart Company Data” has arrived in practice and is already being used by technology leaders. This is shown by the examples of three companies that have made great progress in this area:
- Hansaflex AG, one of the world’s leading suppliers of hydraulic systems, manages around 400 regional warehouses practically fully automatically. Demand forecasts, warehousing and scheduling strategies are specified to the SAP system by DISKOVER using automatic simulation and a differentiated set of rules.
- TROST Fahrzeugteile, a brand of WM SE, one of the leading automotive parts wholesalers in the independent aftermarket in Germany and Europe, uses the planning and scheduling rules also defined in the DISKOVER system to control the scheduling of its central warehouse and the approximately 150 branches in Germany, Austria, the Czech Republic, Slovakia and Romania.
- The STO Group – a leading international manufacturer of paints, plasters, varnishes and coating systems as well as external thermal insulation composite systems – uses the DISKOVER 4-0 system to control the replenishment of its branches in Germany and Europe in order to specify optimized replenishment strategies to the SAP® system using rules and simulations under economic efficiency criteria.
In all three cases, significant inventory reductions, improved delivery readiness and more efficient scheduling processes were achieved. All three companies see the introduction of the Dispo 4.0 system as a strategic investment in increasing their competitiveness and profitability.
A powerful Dispo 4.0 system can be seen as the CNC control of the machine tool ERP system. Just as production quality, accuracy and efficiency have increased massively as a result of the leap from manually operated machine tools to CNC machines, the control of the ERP system by MRP 4.0 systems will significantly improve scheduling quality, accuracy and efficiency and make scheduling ready for Factory 4.0.
[Gerrit Sames is a professor of general business administration, in particular organization with a focus on ERP systems at the THM Business School in Giessen. He previously held management and board positions at the Monier Group, Schott AG and Buderus Heiztechnik GmbH.
Image by THAM YUAN YUAN on Pixabay