5 steps for safely dealing with uncertainties in your supply chain
by Prof. Dr. Götz Andreas Kemmner
Inventories generate costs, but also guarantee security. But how much safety stock does your company actually need in order to be protected against economic loss? Most companies have the wrong safety stock of the wrong items in the wrong places – not to mention a general excess of stock. Our five steps to safely managing uncertainty in your supply chain will help you get a grip on your safety stock and continuously work to reduce inventory and costs.
How much safety stock is hidden in your warehouses? What uncertainties would you like to protect yourself against? How much residual risk remains? These three simple questions demand precise answers, especially in this day and age when we want to be as ready to deliver as possible but cannot afford to have excess stock. Do you have the answers? Probably not. You could now ask your logistics manager, your supply chain manager, your dispatchers or your production planners. However, they will probably not be able to answer your questions either. These three questions are extremely important. Safety stocks protect your company against economic damage such as loss of image, loss of sales or loss of profit. Despite these advantages, the safety stock is an important part of your overall portfolio and should therefore be planned precisely.
In our experience, there are three main reasons why not only the supply chain manager, but also the management level itself should be familiar with the safety stock and its costs:
- Although safety stocks absorb all major uncertainties, they should not be too high.
- The remaining statistical residual risk should be known.
- The safety stock is a precise statistical indicator for estimating the uncertainties in the company’s supply chain. It should therefore be recorded and checked regularly.
But what does it take to set your safety stocks at the right level across the entire supply chain? The following five steps will help you on your way to your goal:
5 steps to professional management of your safety stocks1. review your current strategy |
Step 1: Review your current strategy
Start by taking a close look at your ERP system. Virtually every ERP system enables the determination of safety stocks at material or item level. We will see later that this type of safety stock is intended for special circumstances and not as a hedge against general uncertainties. Ask your IT department for a list of all SKUs with the required basic requirements per item and the corresponding safety stock levels for all stock and warehouses. The basic requirement corresponds to the amount of stock you need to cover the average consumption of an item during the replenishment period. Ask for both numbers in units of quantity and value.
While IT takes care of this analysis, you can check the various departments for their security inventories. The quest for security is a human reflex and affects every aspect of our daily lives – including our work. Accordingly, every employee naturally has their own tricks for building security buffers into their part of the supply chain. Perhaps the sales department has manually set the safety stocks in the ERP system, just as the scheduling, production planning and purchasing departments may have done. However, safety stocks can also be hidden elsewhere. Increasing the minimum order quantities or the production lot sizes in the ERP system are other popular tricks to hide safety stock. In addition to changes in material quantities, the dates for production orders, purchase orders or requirements are also often simply brought forward. Longer opening horizons are also very popular, as are the “adjustment” of safety times and additional order processing or incoming goods processing times. Don’t forget the supplies “under the workbench”, where additional items are often stored for safety.
But if everyone is so concerned with safety stocks, why should the management worry about it? Well, if you were a general on the battlefield, would you let every officer and soldier walk around with whatever weaponry they see fit? Certainly not!
Safety stocks are only reliable if they are carefully identified, monitored and maintained on an ongoing basis. Anything else is not reliable. It is therefore absolutely essential that everything is put on the table during this review of safety stocks. After all, the aim is not to take away the departments’ cherished security stocks, but to manage them openly and centrally – all in one armory, if you like.
Have you now tracked down all the hidden safety stocks? Let’s take a look at the following graphic:
This curve is based on many detailed stock simulations. It shows how much safety stock different companies need in addition to their so-called basic requirements in the respective warehouse in order to achieve their target delivery readiness.
As you can see, some companies only need a small amount of safety stock, while others need a lot more. The chart also shows that 80% of companies with a 120% safety stock are hedged against demand-related uncertainties in addition to the basic stock. And this is exactly what the safety stocks in the ERP system are intended for – and only for this purpose: a hedge against fluctuations in demand. You can save this number as your first hint. However, this does not mean that you should now build up 120% safety stock for every single item in your warehouse. For items in regular demand, a much smaller percentage of safety stock should be sufficient, while for items in very irregular demand, this 120% may not be enough. The 120% is simply the statistical average for the total safety stock across all items in relation to the total basic requirement, which is sufficient in 80% of companies. For you, the required percentage may be significantly lower.
By now, your IT department should have provided you with the list of item-specific safety stocks. Now add the hidden safety stocks from your inventory and compare this total safety stock value with the 120% KPI in the graph above. This should give you an initial impression of your actual position in terms of security holdings.
Each warehouse stage in the supply chain has a demand side (outgoing warehouse side). For finished goods, the demand side is the market, while raw materials and purchased parts are demanded on the production side. In order to absorb the fluctuations in demand that occur here, a safety stock is sensible and necessary at these inventory levels. The safety stock required to deal with these fluctuations in demand should actually be referred to as “forecast safety stock” for clarity, but is generally just called “safety stock”. However, this ignores the fact that there are different types of safety stocks, which leads us directly to step 2:
Step 2: Identify the various uncertainties you want to guard against
Safety stocks are intended to absorb uncertainties. But what types of uncertainties are these exactly? And which of these can actually be eliminated by the portfolio?
From a very pragmatic perspective, a supply chain with procurement, production and distribution consists of a network of storage levels with time intervals in between that are required for transportation, production or other time segments. Uncertainties in your supply chain present themselves as disruptions on the supply side of a warehouse level, the demand side of a warehouse level or in the warehouse itself. As far as materials management is concerned, these disruptions occur as follows:
- On the supply side: fluctuations in delivery times, deviations in delivery quantities or deviations in product quality,
- On the demand side: Fluctuations in demand on the demand side or
- In the warehouse: obsolete stock, stock discrepancies, damage to parts or loss of parts (but this topic is reserved for another article).
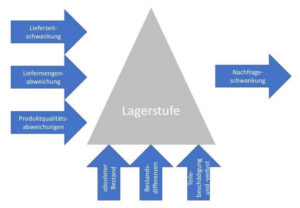
This may sound rather simple, but what are the characteristics of an unreliable supplier? Fluctuations in the delivery time, deviations in the delivery quantity or poor product quality. In contrast, what are the characteristics of unreliable production or an inconsistent manufacturing process? Precisely, fluctuations in the delivery time, deviations in the delivery quantity or poor product quality.
Unreliable transport routes from no man’s land, non-transparent customs clearance in some banana republic, delayed incoming goods inspection, incorrect delivery, transport damage – these are all factors that lead to fluctuations in delivery times, deviations in delivery quantity or poor product quality. Of course, deliveries can also be made too early and in too large a quantity, but at least this has no negative impact on the readiness to deliver to the market.
Let’s now take a look at the various warehouse stages of a supply chain. In order to determine the individual safety stocks required here, we need to quantify the fluctuations in delivery time, deviations in delivery quantity, poor product quality and fluctuations in demand across all storage locations.
I am sure you will agree with me that the finished goods warehouse or the component warehouse need their safety stock in any case in the case of customer order-related production in order to be protected against sudden additional requirements. You might say that it is not your responsibility to protect yourself against the negligence of your suppliers, but please realize that you are already doing this today, and at considerable expense!
Your purchasers travel halfway around the world in search of alternative sources of supply; your schedulers spend hours on the phone trying to negotiate more parts or faster deliveries from suppliers; your sales department appeases your customers who are urgently waiting for the ordered goods; your quality assurance department has to prepare yet another deviation report so that your production department can at least complete the most urgent orders.
Of course, you need to look at how to manage these safety stocks through appropriate measures, and this is the core of step 4, but it can sometimes be more cost-effective to stop the avalanche of problems first by building up enough safety stock in the purchasing warehouse to prevent it from sweeping through the entire supply chain to your customers. We therefore calculate the required safety stocks in the next step and see whether the increased stocks pay off.
Step 3: Determine the individually required safety stock heights
For this step you need a little knowledge of statistics and probability theory. If you don’t really enjoy statistics, as your colleagues in quality management hopefully do, you should perhaps consult an expert now.
The correct calculation of safety stocks is no simple matter. And unfortunately, it requires a little more insight into the subject matter than simply applying a mathematical formula. A detailed explanation would probably bore you, so here are just a few pointers. Let’s first look at the safety stocks on the demand side. Here, three errors usually lead to incorrect safety stock levels and also to incorrect demand forecasts:
Forecast error 1: | Forecasts and safety stocks are mainly created with a view to previous consumption. If you do not ensure that your ERP system uses the correct demand time series for its calculations, you will only receive perfect waste despite perfect calculations. |
Forecast error 2: | There is a statistical correlation between demand forecast, safety stock and target delivery readiness. Many ERP systems on the market ignore this connection or do not even allow the calculation of statistical safety stocks. |
Forecast error 3: | ERP systems usually calculate forecasts and safety stock levels incorrectly for 90% of items because they use statistically inadequate methods. These methods assume a normally distributed demand curve, but this does not apply to the majority of items. |
In order to calculate reliable safety stocks, distribution-free methods or a special simulation approach for creating forecasts and determining safety stocks are essential.
Safety stocks that absorb uncertainties on the incoming goods side are called delivery or supply safety stocks. ERP systems do not usually take care of these safety stocks. The existing uncertainties on the incoming goods side of the warehouse are usually buffered by extending the replenishment lead time and thus estimated values are included in the requirements planning. However, extending the replacement time harbors potential risks, especially in the case of in-house production. All too often, this is where the production control error cycle begins, which ends in decreasing delivery readiness and increased work in progress.
Experts can also be helpful here, even if you may not want to hear it. Look at it this way: even if you are an excellent driver, don’t tinker with your car’s engine yourself, but leave the complex tuning of ignition, combustion and valve adjustment to an expert. “Driving” your company’s supply chain, i.e. being able to plan and control it, is a different matter to creating, introducing and coordinating the necessary planning and control processes.
Safety stocks can tie up a lot of liquidity and therefore cost a lot of money. As already shown, the safety stock alone for fluctuations in demand can amount to 120% or more of your basic stock.
For this reason, you should link the adjustment of your safety stocks to an inventory optimization process. In our experience, 80% of our customers can reduce their total inventory by 20% if safety stock levels are set correctly and inventory levels are optimized. This compensates for the higher security holdings and the consulting costs that are likely to be incurred and still leaves you with some liquid funds at your disposal. You also save on storage costs every year.
As you should have determined the necessary safety stocks by now, we can now continue.
Step 4: Build up the necessary safety stocks and eliminate the stock drivers at the same time
The first part may seem trivial now that you have identified the safety stock you need, but providing additional materials or parts may prove difficult. If you don’t build up safety stocks in times of plenty, you won’t have them to hand in times of need. Because it is so difficult to build up safety stocks, you should start immediately, even if the long-term goal is to reduce or avoid them. You should therefore consider how to avoid this when building up the required safety stock and answer the following questions:
- What are the root causes of delivery time fluctuations, quantity deviations or quality defects on the incoming goods side?
- Who is responsible for these safety stock drivers and their elimination?
- Which of these causes (safety stock drivers) can be eliminated in the short term?
- Which of the remaining causes occur so regularly that you should maintain an adequate safety stock on a permanent basis?
- Is it possible to reduce the replenishment lead time of an item in a stock level? Shorter throughput times require less safety stock!
- Is there a department that has to pay for the remaining safety stocks?
In order to solve a problem, its causes must be identified and the responsible department, which has starting points for eliminating the problem, must help with the solution. A department that is unable to solve a problem caused by it should be charged for the resulting costs in the operating account – but that may just be dreaming.
In practice, it is often a little more complicated and the responsible party cannot be identified directly. In this case, the department closest to the cause should take responsibility.
Let’s take a look at the ‘usual suspects’:
On the demand side, poor statistical forecasts and incorrect safety stock calculations as well as insufficiently predictable customer and market behavior are the reason for excess (safety) stocks. Supply chain management should actually be responsible for the former, while the latter is at least roughly the responsibility of sales. Can customers possibly be motivated (or educated) to deliver better forecasts or order on time? Can customers who turn out to be incorrigible inventory drivers be reasonably charged for this? In the long term, all parties to a Supply Chan bear the costs jointly. Smart customers should therefore be seriously interested in an improved forecast (I know, another daydream on my part).
Negligent maintenance of the product portfolio is another trigger for high safety stocks. Products that are not in regular demand and only account for a small proportion of sales are classified as CZ items. In some companies, they account for between 30% and 50% of the total SKU and require unnecessarily high safety stocks. The sales team and product management could reduce delivery readiness or streamline the product portfolio. The costs for the remaining safety stock would have to be covered by the respective sales prices. Unfortunately, however, the costs are distributed proportionally across all items in relation to their turnover (according to “carrying capacity”) and are usually not charged to the items that cause these costs. CZ articles can therefore have false contribution margins and thus make you believe that you are earning from them. In my experience, this is often not the case with more precise cost allocation.
On the incoming goods side, the purchasing department should ensure that suppliers adhere to reliable delivery times, delivery quantities and product quality. Buyers who limit themselves to keeping purchase prices low rather than keeping total operating costs in check are contributing to excess safety stock and should therefore be urged to monitor unreliability on the part of suppliers. Of course, the purchasing department will now object that some purchasing parts are highly developed, can only be obtained from a few suppliers or must be available in an absurdly wide range. Well then, development and production must also be held accountable!
If you are on the procurement side of the supply chain and have to pass on fluctuations in demand to your suppliers or build up safety stocks, try to find out who exactly in the supply chain is causing these fluctuations: customers, sales or production? Unfortunately, the perception of this problem – and thus its solution – can only be achieved in this way.
And now finally to the in-house production. Delays, deviating delivery quantities and quality losses also occur here. But you have to look very closely to find the areas that can help improve the situation. In the case of in-house production, safety stocks may be required due to production problems or unreliable production control. If finished parts or incoming goods are not immediately checked for quality and released, quality management still has some homework to do.
A clear assignment of responsibility for measures against the various safety stock drivers helps with the final step:
Step 5: Develop a safety stock management system and introduce a continuous improvement process
As we hope we have made clear, safety stocks are a good indicator of weaknesses in your supply chain. Having to hold on to an additional 50% of the total stock volume due to problems in the production process hurts. It is just as painful to ignore the need for safety stocks. We have only two approaches to deal with these uncertainties in our supply chains: Either we have to reduce or eliminate these uncertainties or we compensate for them with safety stocks (or excess capacity, which in turn incurs costs). You may not be willing or able to build up all the safety stocks you need to cover all the uncertainties, but calculating the required safety stock will bring these hidden costs to light for the first time and help you prioritize.
And now, before everyone rushes off to work: A systematic approach could be helpful. I therefore propose the following process steps:
- Identify all uncertainties in your supply chain
- Quantify the required safety stocks
- Establish the most important safety stocks to secure your supply chain
- Question the real causes of these uncertainties
- Assign responsibility for reducing uncertainties
- Develop solutions to reduce uncertainties
- Initiate measures
- Monitor the results
- Continuously improve your solution approaches
Finally, I would like to come back to a statistic: the best companies work with safety stocks of less than 25% of their total portfolio. We hope and firmly believe that our five steps will help you to move up into this league and will be happy to support you on this journey.