The supply chain management team at Otto Golze & Söhne has to plan material for around 2.9 million floor coverings and carpets every year. Otto Golze relies on the Advanced Planning & Scheduling (APS) tool DISKOVER from SCT to ensure that the complex interrelationships in the supply chain are easy to handle. It is one of the most feature-rich and therefore most powerful APS systems on the market and was recently awarded the BME seal of approval. Following its introduction, the previously normally high level of delivery readiness was increased from 95% to a particularly high 98% – with a significant reduction in inventories.
The brand manufacturer Otto Golze & Söhne offers high-quality floor coverings and carpets made of natural fibers, fitted carpets, door mats, clean-off mats and stair mats under its own ASTRA brand. Collections for the SCHÖNER WOHNEN and JOOP! brands are also developed and distributed throughout Europe. Golze recorded sales of 2.7 million door mats and 206,000 carpets in 2017. In addition to standard products, Golze also manufactures custom-made carpets. These approximately 46,000 orders per year require fast deliveries in batch size 1. Due to quotas, however, the sales channel via DIY stores also requires strict adherence to agreed delivery quotas, which requires maximum delivery readiness across the entire range. At the same time, demand in all areas fluctuates relatively strongly depending on the season. When the dirty weather sets in – no matter what time of year – the demand for clean-off mats increases exponentially, for example. In addition, the product ranges change every season, which means a not inconsiderable exchange of goods depending on the collection. On the goods procurement side, there are sometimes large suppliers with fluctuating delivery readiness, which results in high inventories without suitable countermeasures. Due to global purchasing, replenishment times are also extremely long for some product categories.
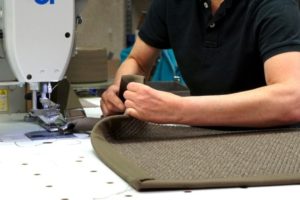
Increase delivery readiness and reduce inventories
Otto Golze wanted to be able to handle these complex relationships with sometimes competing objectives such as ‘favorable purchasing conditions despite small batches’ more efficiently than with the on-board resources of conventional merchandise management systems, such as those offered by ERP systems. Stocks were too high and the overall readiness to deliver was not yet optimal. A 95% readiness to deliver has already been achieved. But it should be 98 percent. However, an increase in stocks would not have been sustainable. On the contrary, they should also be reduced. Following a supply chain management project by the management consultants at Abels & Kemmer GmbH, which is celebrating its 25th anniversary this year, and the introduction of the advanced planning and scheduling tool DISKOVER from SCT GmbH, which can work with all common ERP systems, the company was able to increase its delivery readiness to the desired target figure of 98 percent. At the same time, the value of inventories fell by an impressive 43% from EUR 8.7 million to EUR 5 million.
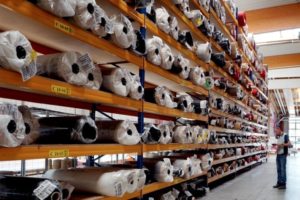
A wide range of functions is important
This success was made possible by several measures. On the one hand by checking and partially optimizing all relevant scheduling parameters, and on the other by introducing new sets of rules and item class-specific scheduling algorithms, which can be mapped in DISKOVER in a highly granular manner and thus very precisely in line with actual requirements. In addition, scheduling was consistently switched to shorter planning intervals. In some cases, orders have been planned and placed with some major suppliers on a three-monthly basis in order to achieve the best purchasing conditions. This planning was converted to monthly planning for all standard products to protect stocks. As a result, the stocks that were no longer ordered were successfully transferred to the supplier. The high level of planning transparency gained in DISKOVER provided all the necessary key data for the conclusion of framework agreements with breathing lots, so that the good conditions of the high quarterly purchasing quotas were maintained, but inventories in this area fell drastically.
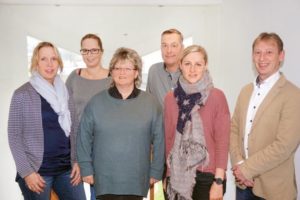
Sustainable stock reductions achieved
Even after several years of operation, Golze is still extremely satisfied with SCT’s scheduling software – which, like the latest cloud solutions, is constantly updated during operation in the continuous delivery model – because stocks have been kept constant in relation to sales and thus sustainably low. In addition, with just a few adjustments, the carpet warehouse in Hachmühlen, for example, which was newly commissioned in 2014, could be easily mapped in the system, as the tool can of course plan several warehouses as well as local distribution hubs located downstream and therefore closer to customer requirements. If required, this can also be done worldwide, as the most common language versions of the software are already in productive use with many customers.
Manage complex supply chains intuitively
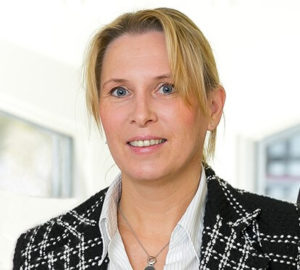
Long-time employee Andrea Taufall has headed the Supply Chain Management team at Golze for around a year and is also responsible for the company’s quality management. She is impressed by the APS tool: “DISKOVER has a high level of detail and comprehensive functions. Nevertheless, I was able to familiarize myself quickly and easily thanks to the intuitive interface. So users don’t have to worry about being overwhelmed when using this highly powerful tool with its many adjustment screws. It has a very intuitive structure.”
Otherwise, the APS tool does exactly what is expected. It enables a high level of delivery readiness with low inventories in the long term. “The planning tool gives us exactly the security we need to be able to satisfy fluctuating demand with high delivery readiness, even with low stock levels,” says Taufall.
All the functions that users want
The test results of the German Association for Materials Management, Purchasing and Logistics (BMEnet GmbH), which recently awarded the DISKOVER SCO scheduling management system the “Seal of Approval for Sales Planning/Inventory Management” once again, confirmed that the functions of the APS tool are truly comprehensive: The test results achieve top scores with 100% fulfillment of the mandatory criteria defined by the BME (299) and 81% of the optional criteria (58), resulting in an overall degree of fulfillment of 97%. According to Andreas Richter, who is responsible for awarding the BMEnet seal of approval at the BME, there is currently no other company that has had an even remotely comparable range of functions confirmed by the BME.
Lots of know-how and many lines of code
Such a complete package, which leaves almost nothing to be desired, cannot be created from nothing. There are many man-years of work behind it: Based on research work at RWTH Aachen University, the APS tool has been continuously developed for over 20 years and has now reached such a high level that even the experts at the BME only consider a few of the criteria to be in need of improvement. The software suite is therefore probably one of the most powerful advanced planning and scheduling systems on the market.
Simple and efficient
SCT’s APS tool is characterized by extensive simulation mechanisms that run automatically in the background and continuously optimize planning and scheduling settings and decisions. In this way, users benefit from a high level of forecasting accuracy and planning precision – and companies benefit from sustainably reduced inventories while at the same time ensuring the necessary readiness to deliver. Overall, dispatchers can therefore plan better with less effort, which in itself is an advantage of APS solutions. DISKOVER SCO’s simulation options also allow the effects of different logistics strategies to be simulated without risk before final decisions are made. This makes it possible to find the best inventory forecast for a wide range of product groups and life cycles.
From the dashboard easily into the depths of detailed planning
The APS tool also impresses with its sophisticated analytics and reporting functions, all of which are integrated into the tool so that no special solutions – such as Excel – need to be maintained manually. Another advantage of this solution is that you can dive directly into the order proposals from the KPI level (Key Performance Indicators). This would be much more time-consuming in the ERP system with the necessary supplementary reporting and analysis tools.