New SCM system optimizes the Sihl Group’s global supply chain – across all ERP boundaries
by Fabian Ossen, Sihl Düren, and Armin Klüttgen
How can a global company like SIHL, with sites in Switzerland, Germany and the USA, which has to bring three previously independent plants under one roof in terms of planning, manage this complex task as efficiently as possible? And that with three different ERP systems?
The decisive factor here was not only the DISKOVER integration software, but also two special functions that enable automated forecasting across the entire planning chain.
Globally active companies that have not grown organically, but have emerged through mergers and acquisitions, do not need to standardize their ERP systems in order to optimize processes between the individual locations. The cross-location use of a Supply Chain Management (SCM) system based on Advanced Planning & Scheduling (APS) tools such as DISKOVER, with which the Sihl Group has recently optimized its global supply chain across the various ERP systems as if it were a single plant, is sufficient.
The Sihl Group is a leading international manufacturer of printable media for the fast-growing global digital printing market – from photo paper to wallpaper, art print media, tickets, labels and packaging. The company is the only one in the world to operate as a single-source provider thanks to its broad portfolio and comprehensive industry expertise. Customers and partners benefit from technologically leading product solutions and innovative, process-supporting services to optimize value creation. Over 450 employees worldwide work on this every day at the main sites in Bern, Düren and Fiskeville near Boston in the USA. In 2018, Sihl generated sales of 125 million euros and delivered over 60,000 consignments to over 1,000 customers worldwide.
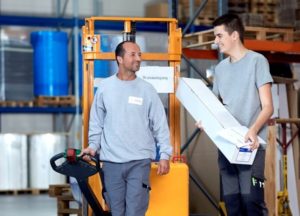
Limited transparency with regard to global inventories
One of Sihl’s organizational challenges, however, is the multi-stage production at the three different sites with a wide variety of recipes, which are stored in many long parts lists. As a result, new demand for end products triggers many requirements in procurement and upstream production across all plants. Organizing such global production as if it were a single plant was only insufficiently possible at Sihl until recently, as the group was created out of acquisitions. As a result, the locations had previously operated largely independently and basically only maintained customer/supplier relationships, which were more intensive than those of non-affiliated companies, but in organizational terms were handled exclusively via the ordering system using the ERP system. As a result, there was little transparency in global inventories across all locations.
Global view of the joint supply chain not possible
It was possible to aggregate different inventories via the independent ERP system of each location. However, it was not possible to create complete transparency with regard to stocks of finished and semi-finished products and chemicals, which would enable a centralized view of global supply chains. As a result, the production of individual items was scaled back or ramped up in a comparatively uncontrolled manner, based more on a sense of proportion and gut feeling, because there was a lack of transparent stock information and precise forward-looking planning requirements. As such a situation certainly holds great potential for optimization, Sihl’s management set itself the goal of creating greater transparency across all locations with regard to inventories and future stock requirements.
Primary requirements of one should automatically trigger secondary requirements of the other
In future, for example, it should be possible to control the stocking of the warehouse in the USA from Düren on the basis of targets for stock levels and delivery readiness as if it were the company’s own warehouse. Today, Düren can react to the changing requirements in the USA even before the actual orders have arrived from the sister company. The advantage is obvious: the increased transparency and greater overview enable the entire group of companies to operate more efficiently. It was therefore necessary to transfer the separate planning and scheduling methods at the various locations into a single system. This can certainly be organized if the same ERP system is used everywhere. At Sihl, however, a different ERP system is used at each location, which has historical reasons, as the Sihl Group was formed from different acquisitions.
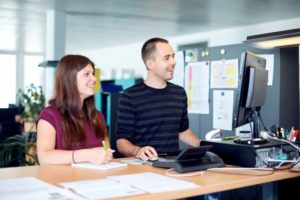
Turning three ERP systems into one is extremely time-consuming
For example, SAP is used in Düren, a solution based on MS Access in Bern and a Sage 3 platform together with other modules from other manufacturers in the USA. This means that two out of three systems would have had to be abandoned for a standardized ERP solution. However, this would have triggered immense change management processes at the affected locations and placed a heavy burden on them for months and sometimes years. It was therefore decided to opt for the adaptive use of a supply chain management system that docks onto all three ERP solutions in order to standardize the planning and scheduling methods. This is much faster, costs less and also provides more accurate data.
Supply chain management software is the answer
Sihl uses an SCM system based on the Advanced Planning & Scheduling (APS) tool DISKOVER SCO from SCT GmbH as an integrated and standardized planning platform. It obtains its information from all three ERP systems and returns the necessary planned requirements to the respective ERP systems on the basis of daily updated demand forecasts. All requirements are now planned globally within DISKOVER. The system knows the different supply relationships between the individual locations – broken down to BOM level. It can thus optimize the global flow of goods within the entire Sihl Group, as all secondary requirements associated with the end product are generated automatically.
Continuous planning chain without interruptions or gaps
In the implementation project, which was supported by the management consultants Abels & Kemmner, the parts lists of the individual locations were ‘married’ – i.e. logically linked together. In a single nightly MRP run (Material Requirement Planning or Material Resource Planning) in DISKOVER, all requirements of all locations are determined. In this way, the requirements of one location automatically become secondary requirements for all other locations involved in production. The MRP run generates planned orders for these requirements if there is insufficient stock. In the next step, these are operationally converted into production orders in the respective ERP system in order to ultimately achieve the stock level that matches the specified delivery readiness. Today, this setup ensures a continuous planning chain without interruptions or gaps in all three plants, as if they were a single plant. From a purely technical point of view, DISKOVER could even be used for ordering and only transfer this data to the ERP systems. The question of which system is the leading one can therefore be decided flexibly depending on requirements.
AI that learns from the past for the future
Operationally, the USA plant was integrated by manually integrating the sales employees’ forecasts based on actual orders, framework agreements and individual estimates of future sales success. The system was gradually enriched with more and more data in monthly cycles, so that ultimately, like a system with integrated artificial intelligence, it provides increasingly precise forecasts using more and more “big data”. After just a few months, this led to an automatically generated demand forecast that no longer had to be adjusted manually and manually, thus significantly reducing the burden on the sales department with regard to the submission of sales forecasts as part of sales planning. Today, production and procurement requirements are forecast fully automatically by the SCM system. Major fluctuations in demand due to changing customer relationships – such as new listings or special promotions – can be easily integrated using the SCM system’s special requirements planning functions.
Complete transparency for crystal-clear decisions
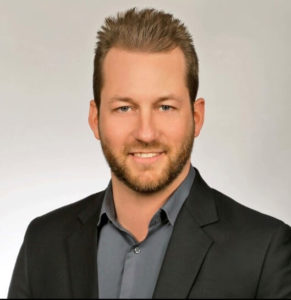
“Thanks to DISKOVER SCO, we have a global, virtually merged plant. This increases transparency enormously. Stocks can now be ramped up or down in a much more controlled manner. We can see exactly where the company stands and determine where we want to go. Our inventory targets, which are also based on the company’s delivery promise and KPIs, can be clearly planned, implemented in line with demand and transparently monitored,” explains Fabian Ossen, Supply Chain Manager at Sihl in Düren.
Demand-oriented delivery class classification
Other important points during the introduction of the SCM system were the implementation of rules to optimize planning and scheduling parameters – for production to optimize capacity and for purchasing to increase efficiency and optimize framework agreements. For this purpose, ABC/XYZ analyses of the articles were also carried out according to sales volume and order frequency, as well as a classification of all products according to delivery classes for a grading according to speed of delivery from order. The introduction of these delivery classes made it possible to identify decoupling points for certain products that Sihl does not have to deliver directly. As a result, more semi-finished goods can be stored instead of finished goods, which reduces inventory values and thus ties up less capital in the company.
Net working capital optimized
In addition to increasing transparency, the use of the cross-plant SCM system has also led to a reduction in inventories while still maintaining the specified delivery readiness. One of the objectives was to optimize the key performance indicator “net working capital”. If this KPI, which Sihl calculates from the key figure form ‘inventory plus receivables minus liabilities’, is lowered, there is important scope for investments and increases in earnings.
Key figure dashboard in preparation
In the future, a web-based dashboard will also be provided for Sihl’s management in order to display selected KPIs of the supply chain in a highly aggregated form and at the same time much faster and in more detail than would be possible with the ERP systems currently in use. In this add-on tool of the APS tool, you can use favorites to specify which KPIs are displayed on the start screen as required. It can also be used to implement a push system via e-mail to trigger periodic or ad-hoc notifications when certain values are exceeded or not reached. The net working capital KPI could also be integrated here, for example, provided that all the necessary data is also drawn from the ERP systems.
Comprehensive reporting functions
The APS tool used also impresses with its comprehensive reporting functions. For production, for example, a report is generated automatically on a regular basis, showing the production manager the worklist of the individual machines two weeks in advance. DISKOVER therefore also provides important information on machine utilization for production. The production planner can then use this data comparatively easily to design the shifts to meet the target. This and many other reports can be generated extremely flexibly with the APS tool. In push mode, parameter settings can be regularly checked and confirmed by purchasers so that, for example, exceptions do not become standard. Every few months, for example, expensive minimum stocks can be checked. The flexibly configurable report dispatch triggers can even be used to automatically send reminders for overdue orders to the purchasing department. Once all this has been set up, shipping is completely effortless. This makes work much easier for everyone involved.
SCM integration is faster, better and cheaper than ERP consolidation
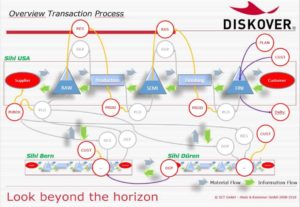
All in all, the SCM system used, based on the Advanced Planning & Scheduling (APS) tool DISKOVER SCO, therefore fulfils many functions that globally operating companies with interwoven supply relationships between the individual locations could otherwise only achieve operationally if they standardized their ERP systems. However, when using APS-based SCM systems, the ERP systems no longer need to be standardized in order to optimize the supply chains. This avoids costly change management processes due to the introduction of new ERP systems. This is an advantage that can also be an important lever in merger & acquisition processes for faster and more efficient leveraging of planning optimization potential, which can quickly release enormous amounts of money through inventory reductions.
Increased transparency creates more time for the essentials
In contrast to pure ERP processing via customer/supplier relationships in the form of orders, a cross-company SCM system links all locations. In addition, you achieve significantly more transparency for everyone involved in the supply chain, as everyone can see what the other person’s requirements are at any time and what the actual stock situation looks like. All (secondary) requirement elements are also generated automatically across all location boundaries. This increases the planning reliability of the supplying partner and saves an immense amount of time. It also enables better foresight than if the individual locations only had to plan on the basis of orders and external forecasts.
The ideal solution for just-in-sequence production planners too
It would therefore also be of great benefit to closely interlinked companies that do not belong to a group but only work closely together – such as manufacturers and suppliers in the automotive industry – if they could forecast and request their requirements for just-in-sequence production in the same way. This would ultimately make it possible to realize a virtual factory across company boundaries, which is already planned by many in the course of Industry 4.0 efforts. SCM systems based on Advanced Planning & Scheduling (APS) tools are therefore also the right systems for change management in the context of cross-company Industry 4.0 processes that focus on batch size 1 and are produced globally in virtual factories.
Orders are still placed – but fully automated if required
However, the SCM system does not dispense with the purely formal ordering process, which is necessary for complete documentation anyway. However, depending on the configuration and interaction between the SCM and ERP systems, it can be fully automated. The interaction between the SCM and ERP systems is, of course, synchronized at all times without redundancy, so that it is impossible for requirements in the SCM system and orders that arrive via the ERP system to add up.
Pay attention to distribution-free procedures
“Incidentally, a similarly high level of transparency would not even be possible if the same ERP system were used everywhere, as the planning depth of APS tools such as DISKOVER is naturally higher thanks to more sophisticated rules and regulations,” explains Armin Klüttgen, Principal at Abels & Kemmner GmbH. In addition, the APS tool also uses distribution-free methods for forecasting and safety stock calculation, which only very few APS tools offer. However, distribution-free methods are important if basic requirements and safety stock calculations are to be more accurate. They should always be used to achieve the stock required for the desired delivery readiness if the actual demand distribution is not known and therefore cannot be reproduced mathematically and statistically correctly. And this applies to the majority of all articles.
This article was also published in an editorially modified form in issue 11-12/2019 of the magazine
Logistics for companies
on pages 45 ff.
This article has also been available on the CIO Magazine website since October 29, 2019.
You can find this article in English on page 23 of the Q3/2020 issue of the IFPTA Journal – or on page 25 here in the online edition.