Forging the cause-and-effect chain
By Dipl.-Kfm. Armin Klüttgen
There is a wealth of problem-solving techniques and methods. Among these, constraint analysis has proven itself in practice by producing very good, stable and sustainable results. This analysis eliminates identified problems by comprehensively disclosing the causes and the measures derived from them, leading to significant and sustainable improvements in the company.
Identify root causes – define measures – solve the problem
A supply chain is a sometimes fragile and highly complex structure made up of entities of varying granularity. The network of machines, materials, logistics, processes, methods, customers, suppliers, employees and business rules creates a level of detailed complexity and dynamism that often seems almost unmanageable. Insufficient controllability and, as a result, insufficient controllability generate gaps, errors and weak points in the overall process. How should we counter them, or better still, how should we identify them in the first place? Only then can we seriously think about measures and solutions!
This is precisely where constraint analysis comes in. The constraint analysis guides you to the weak points and gaps in your organization, your business processes and your material and information flows, and, if necessary, from the supplier through your organization to the customer.
By carrying out the constraint analysis, you forge a cause-and-effect chain between the main problem you have identified, which you want to solve or at least mitigate, and the core causes of the problem. Once this chain has been forged, you can design measures that attack the core causes. The positive effect of these measures, mitigation or elimination of the core causes, continues impressively through the links in the cause-and-effect chain to the core problem, which in the best-case scenario disappears completely.
This eliminates many other problems in the form of individual links between the core problem and the core cause, which would have been tackled in separate sub-projects and work steps in a conventional process analysis.
Complex challenges, such as the decisive starting points for improving the logistics business model, optimizing business processes and increasing profitability, can be uncovered, efficiently and sustainably attacked and subsequently eliminated with the help of constraint analysis.
The core problem – starting point and hook for the analysis
The starting point of the constraint analysis is always a significant and subjectively perceived, or even better, objectively measured problem, e.g:
- The delivery readiness versus customer is too low, it is 82% with 95% target delivery readiness.
- Inventory turnover rates are too low at < 2
- 35% instead of the targeted 3% of the stock value is in articles with a reach of > 1 year.
- The throughput times for in-house production are 50% longer than required.
- The quality of the manufactured items has declined, reject rates and costs are rising and planning reliability is falling.
- Suppliers’ delivery readiness is too low, which requires additional security mechanisms, such as security times, which increase costs within the company.
- Bottleneck and missing parts situations in production become a permanent issue, missing parts lists and daily store floor meetings to prioritize production orders become the leading control instrument, exacerbating the unrest in production and thus the problem itself.
- …
Problems that are close to the customer or the market are often those that give rise to the longest and most complex cause-and-effect chain, as the core causes sought can have an impact across many levels!
How constraint analysis works
Once the core problem to be solved has been clearly identified, e.g. insufficient readiness to deliver to the customer, the next step is to work out and document the cause-and-effect network so that the root causes can be revealed.
It has proven to be very helpful to record the complete value stream of the company or all relevant areas of the company as a first step. This work step creates transparency and is often an essential tool not only for external but also for internal project staff in order to understand the overall context.
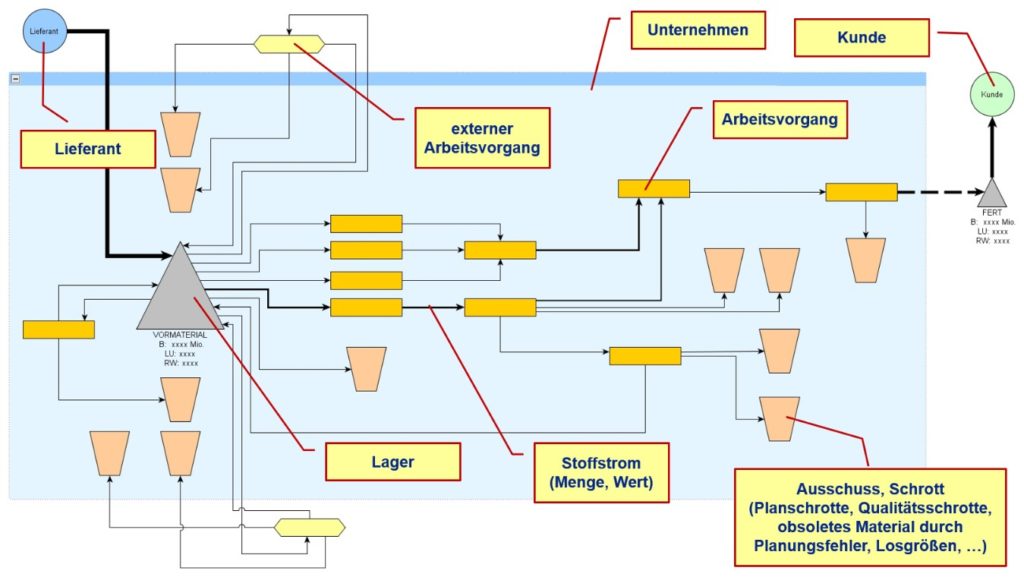
For example, the ability to deliver can be damaged at many points, starting with product development, product management, sales planning, scheduling, quality assurance, purchasing, logistics, the operational business model and more. At this point, the value stream very effectively supports the recognition of correlations and thus the identification of core causes.
Based on this first step, a series of workshops and interviews are then held with the specialist departments involved in order to formulate the process landscape and thus the cause-and-effect relationships in detail and to develop the associated network. Where necessary, correlations can be proven or disproven by analyses and simulations, or their effectiveness can be examined.
Above all, interviews also make it possible to shed light on certain causes and their effects from different specialist perspectives. The aim is to generate a network in which all root causes are at the lowest level. There are no further causes among them.
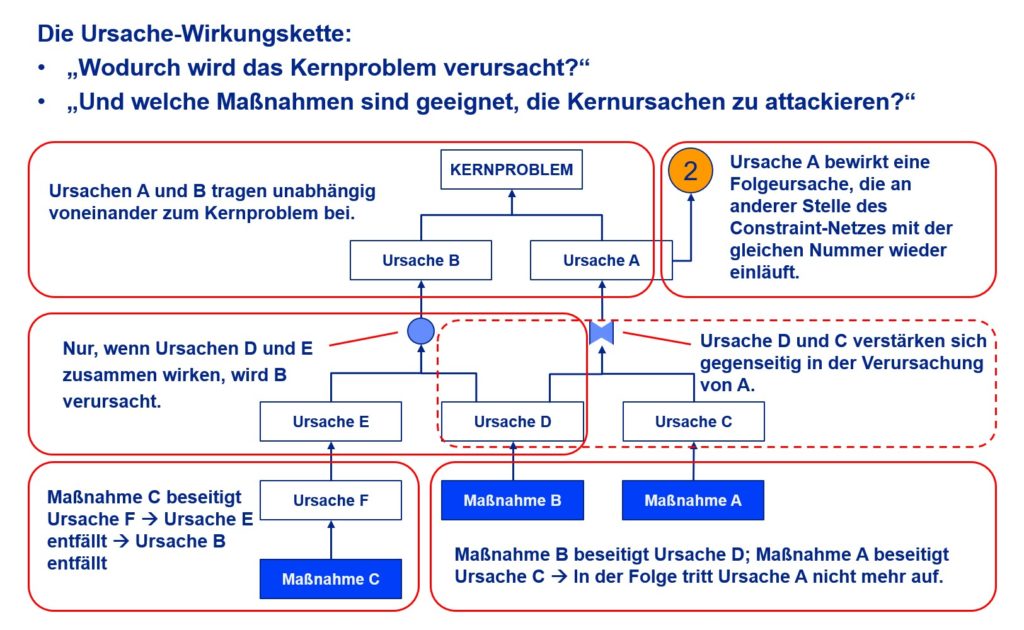
Once the core causes have been identified, it is important to define fields of action and measures that are suitable for eliminating the core causes.
Ideally, the cause-and-effect network can be completely resolved. In reality, however, there are numerous reasons why many significant improvements can be achieved, but the ideal state is still not reached completely or only in the medium to long term.
Possible stumbling blocks in constraint analysis
Figure 3 shows an overview of the result of a real constraint analysis on the question “Why is our readiness to deliver not as desired?”. The graphic gives an impression of the possible complexity of such an analysis and its results.

In the specific example, 72 measures were defined within the framework of 13 identified fields of action, which were intended to attack the causes of the core problem and thus solve the core problem.
Prioritization of fields of action and measures
It is essential to prioritize the individual measures once a certain number and complexity of action areas and measures have been reached. For this purpose, it is efficient to divide the measures into the following assessment classes, taking into account the mandatory sequences and available capacities:
- Effectiveness: How much does the individual measure contribute to combating the core problem?
- Deadline (duration): How long will the implementation take on the timeline (start and completion date)?
- Expenditure (costs): What personnel expenditure (internal, external) must be invested?
A sensible prioritization can then be derived from this classification. In this way, a digestible plan is created that quickly delivers initial results and motivates people to continue working thanks to the success achieved.
Constraint analysis: The conclusion
Constraint analysis is an excellent method for eliminating weak points in a value chain or planning chain, especially if their causes are difficult to grasp. The participants are involved in workshops and interviews from the first problem to the last measure and the identified core causes are derived from clear cause-and-effect chains. The fields of action and measures developed in a constraint analysis are therefore highly accepted within the company. We are regularly pleased to see how consistently and systematically the measures are implemented with the employees during the implementation phase.
So, become a blacksmith and sustainably increase the performance of your company!
Image: © by analogicus on Pixabay