SCT GmbH Supply Chain Technologies has won Rodenstock as a new customer for its advanced planning and scheduling software DISKOVER. The aim of the global innovation leader in the field of eye health and major manufacturer of spectacle lenses and frames is to take its scheduling management to a new level. Previously, Rodenstock mainly used the standard functions of the SAP ERP system for scheduling. As the optimizations achievable at this level have already been fully exploited, Rodenstock is now relying on DISKOVER’s significantly more powerful modular function system to further optimize the material flows. The pilot project went live at the end of 2022.
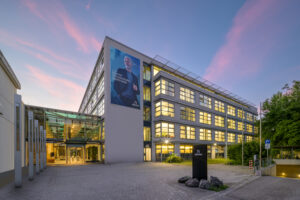
The introduction of a new level of materials planning became necessary because the business at Rodenstock is no longer as continuous as before, but increasingly volatile: Major projects are having an increasing impact on the product range to be manufactured, meaning that the percentage of requirements that can be constantly planned is decreasing, making it increasingly difficult to plan the items to be procured and manufactured with limited resources and a restricted range of functions for sales planning and scheduling tools. It was correspondingly challenging to always offer the best possible delivery readiness despite increasingly volatile business: Customers should be supplied within one day for standard products and within five days for prescription jars, which are still surface-treated and coated to customer specifications.
Sharpening planning excellence
It was therefore important for Rodenstock to significantly sharpen its scheduling management in order to further increase its scheduling excellence in the flow of goods. Important new functions that are now available to Rodenstock with DISKOVER are significantly differentiated scheduling parameters, powerful, flexibly interpretable sets of rules and comprehensive simulation options with which forecasts can be sharpened and sets of rules continuously optimized. Distribution-free methods are also used to determine forecasts and safety stocks. These are important because demand for items is rarely normally distributed, which is why all classic forecast and safety stock formulas systematically miss the mark.
Sales planning on the basis of aggregated characteristics
When selecting the right system, it was important to Rodenstock that the new Advanced Planning & Scheduling system could aggregate articles at different characteristic levels so that employees could make changes to sales planning at these levels and not have to do so at individual article level. This meta-level is absolutely essential, as each employee is responsible for around 30,000 to 40,000 SKUs. If each SKU had to be planned individually, with around 250 working days per year and a 40-hour week, there would only be 3 to 4 minutes per SKU per year, which would be impossible to handle manually. Five material attributes were therefore used as levels of abstraction. In addition, around 100 customer groups were created to combine the planning objects. From the forecast of a major customer, the team can now look at the aggregated characteristics and change their demand parameters, which then automatically affect all associated SKUs and their procurement and production requirements using differentiated MRP parameters and rules.
Procurement requirements planning against limited capacity
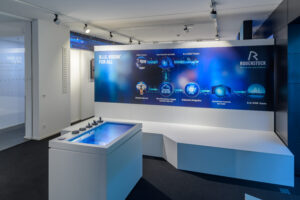
Another important new tool available to Rodenstock is the Capacity Analyzer. It can be used to recognize the effects of the planned orders determined in the MRP on production capacities. Entire order bundles can be shifted across SKUs in one go so that production is not overloaded. This tool had to be expanded for Rodenstock in order to be able to plan not only production orders, but also purchase requisitions to affiliated companies against limited resources. Quantities, deadlines and priorities can now be adapted to the capacity of this virtual factory ‘on the fly’. The planned orders are immediately rebuilt when parameters change, so that capacity optimization options can be run through very efficiently. If these are then fixed after checking the optimum capacity utilization, they can not only be transferred to the SAP system as planned orders for in-house production, but also as purchase requisitions.
Rodenstock expects further optimization potential from this newly created function, as it is now possible to react to changing conditions in the largest production facility in Thailand in a highly agile manner – while at the same time maintaining a high level of transparency and precision in the process with regard to delivery readiness to customers worldwide. In the past, these planned orders were readjusted manually in the event of production bottlenecks, which took a lot of time and was always associated with uncertainties with regard to delivery readiness to the customer, as it was not possible to reliably recalculate all the effects of these rescheduling measures. Now you can reschedule systemically and see all the effects immediately when the plan is changed.
He who rests, rusts
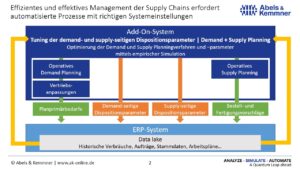
Overall, the introduction of DISKOVER now gives Rodenstock the opportunity to make the numerous interdependencies within the entire supply chain transparent and to further develop the existing daily practice of scheduling on the basis of these findings. Rodenstock also expects a great deal from the evaluation of the linked, long-term demand, inventory and production planning as well as the key figures across all 30 plants and all 200,000 SKUs that is now possible – such calculations were previously simply impossible. “To be able to optimize materials management holistically,” says project manager Andreas Schöttl, “a bird’s eye view like this is essential. Rodenstock sees great potential in the design and application of the differentiated sets of rules, which can be easily adapted to individual requirements, as there is a large degree of freedom in their design and parameterization. This opens up completely new horizons for doing things that would never have been possible with the existing ERP system tools.
What doesn’t fit is made to fit
It was not only the significantly larger modular function system that made Rodenstock decide to use DISKOVER. SCT’s development team was also convincing, as it is very agile and can quickly create new solutions for customers in design sprints that are not part of the standard configuration. For example, Rodenstock is currently evaluating alternative transport routes for articles in order to optimize logistics costs. Such calculations can be mapped by creating alternative sources of supply. Here, however, the dispatcher is required to make decisions between the alternative transport routes based on the requirements to be covered. However, Rodenstock’s aim is to automate this task as well, so that the most cost-effective supply route is always determined, taking delivery readiness into account. Specifically, Rodenstock’s aim is to use the expensive airplane as a mode of transport only when necessary and to make this decision automatically. Such a solution has now been implemented by SCT.
Transparency is crucial
Costs naturally also played a role in the decision in favor of DISKOVER, but user acceptance was ultimately more decisive. After all, the employees who will be operating the systems have extensive know-how that has been built up over many years. They therefore want to understand exactly how the software arrives at planning and scheduling proposals. This is precisely where DISKOVER scores with its high level of transparency, which ultimately creates the necessary trust among users to hand over decisions to such a system and accept automated scheduling decisions.
Efficiency gains open up new potential for further optimization
Following the go-live of DISKOVER as the leading scheduling management system with an interface to the SAP system, which took place at the end of 2022 and was supported by the supply chain management experts from management consultants Abels & Kemmner, Rodenstock is now planning to convert all items to the new system – this is expected to take around two quarters. The next step will be to fine-tune the system to achieve the desired logistical optimizations. For this purpose, the scheduling parameters previously used under SAP must be transferred to the clearly differentiated options of the new system. In addition, a number of media discontinuities need to be resolved so that scheduling ultimately has an end-to-end view of the entire supply chain, spanning several stages of the value chain, logistical decoupling points and a total of 30 SAP plants (production and warehouse locations). Once all this work has been completed, Rodenstock will be able to plan much faster and more dynamically in a more intelligent, differentiated and transparent way and largely automatically, which the entire Rodenstock team is already looking forward to. However, aggregated sales planning on the basis of product characteristics and customer groups as well as the aggregated possible planned order changes against limited capacity already promise Rodenstock immense efficiency gains. These will then also free up the necessary time for users to further optimize the system.
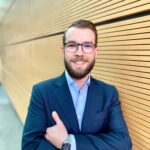
Co-author:
Andreas Schöttl, Senior Manager Supply Chain Planning of the Corporate SCM Department at Rodenstock GmbH