Before discussing MRP parameter optimization, the term MRP parameters should first be clarified: The term MRP parameters, or MRP parameters for short, refers to material or process master data that controls the planning, control, forecasting and scheduling behaviour of materials management systems, such as ERP, merchandise management, inventory management or advanced planning systems. When it comes to MRP parameters, material properties such as delivery times, minimum batch sizes or fixed lot sizes come to mind first. However, MRP parameters also include those that determine which algorithms are used in a materials management system for requirements and inventory planning for a specific item (MRP procedure, lot-sizing procedure, planned value distribution procedure, forecast composition procedure, …) or that determine how an algorithm calculates (forward calculation horizon, backward calculation horizon, α-factor of exponential smoothing, …). Dispensing parameter optimization refers to the correct setting of these parameters so that certain material management or business management goals are achieved. Examples of such targets are the lowest possible total costs in the supply chain, the ability to deliver with the lowest possible inventories or the ability to deliver with the lowest possible costs in the supply chain. Our tip: Without correctly set scheduling parameters, a materials management system will neither produce meaningful forecasts nor meaningful order or production proposals. The desired business objectives are not achieved and the users have to regularly override order and production proposals more badly than well in an effort to maintain delivery capability and/or not allow stocks to rise excessively.MRP parameters are also not static values that are set once for a material. Parameters must be adjusted depending on the life cycle of an item and other varying item properties, such as demand behavior. In practice, this task is usually assigned to the schedulers and they are held responsible if scheduling parameters are not maintained. However, the time required to maintain the scheduling parameters is so great that it cannot be managed by the users in addition to their normal tasks. As a rule of thumb, it can be assumed that for every full-time scheduler, one third to one half of a person is required to keep the scheduling parameters up to date. This effort would hardly be feasible for economic reasons alone. What is ultimately even more serious is that a very deep understanding of the algorithms used in a materials management system is required to set the scheduling parameters correctly. Such a deep understanding is extremely rare among users. To make matters worse, the algorithms of a materials management system interlock like gears in a transmission, meaning that several parameters usually have to be set together in order to achieve the desired behavior. Ultimately, material flows and market behavior for many items in a supply chain are not static but dynamic; they change constantly over time and are more like a turbulent torrent than a laminar flowing stream. It is therefore difficult, if not impossible, to set the planning parameters using gut instinct or simple calculations in such a way that they can cope with this turbulence. Above all, if a target is to be achieved despite this turbulence, such as ensuring the required delivery readiness with the lowest possible average stock levels. Only special software systems for dispensing parameter optimization, such as DISKOVER, can provide reliable help here. Here you can not only define exactly which parameter settings should take effect under which boundary conditions of an article. Instead, the appropriate scheduling parameter settings are determined by simulations with empirical data and stored in an expert system. This expert system then automatically adjusts the scheduling parameters in the materials management system. A materials management system without an MRP parameter optimization system is like a numerical machine tool without CNC control; you should not embark on this adventure!
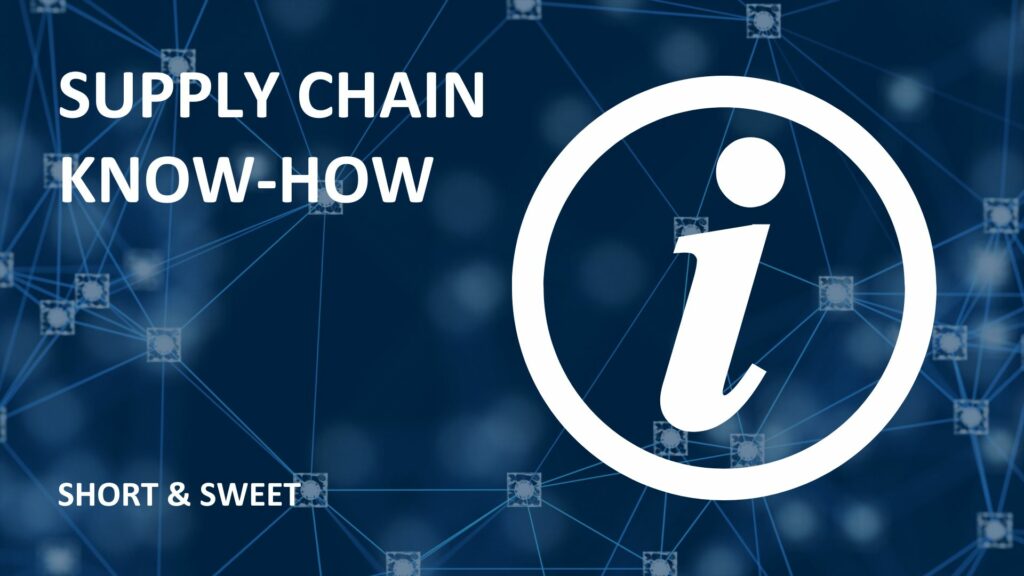
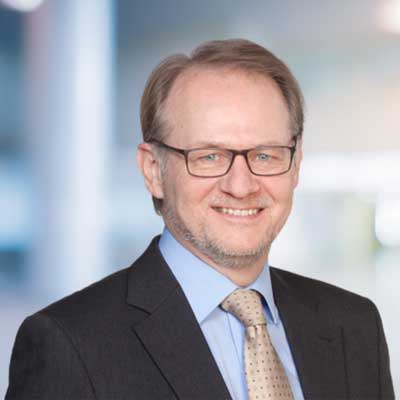
Prof. Dr. Andreas Kemmner
Prof Dr Kemmner is Co-CEO of the Abels & Kemmner Group and has carried out well over 200 national and international projects in 30 years of consulting work in supply chain management and restructuring and was the only publicly appointed expert for the profitability assessment of industrial companies in Germany for over 10 years. In 2012, he was appointed Honorary Professor of Logistics and Supply Chain Management by the WHZ. The results of his projects have already received several awards.
Talk to us!
We are there for you personally and will be happy to advise you individually on our services and solutions.