Belimo has sharpened its demand forecast: Much earlier, much more precise planning
The further you want to look into the future, the more uncertain it becomes. However, due to changing supply chains and longer procurement times, procurement requirements need to be planned much earlier – and as precisely as possible. Belimo has achieved greater precision and thus greater planning reliability by migrating its demand forecasting and safety stock determination to the Advanced Planning & Scheduling (APS) software DISKOVER.
Innovative function of the DISKOVER APS system
A very innovative and useful new function of the APS system is the ability to forecast materials for customer order-related products generated in SAP – a functionality that was not previously available to Belimo. Belimo had also requested the integration of the bearing characteristic curve method for determining safety stocks.
Both functions were newly created in DISKOVER for this purpose, so that the already very powerful APS system is now even more powerful. In particular, the ability to create demand forecasts for customer order-related materials opens up new horizons for many machine and plant manufacturers. After all, they are often project or one-off manufacturers who produce in individual batches and therefore generally cannot cope with SAP’s requirements planning. But back to Belimo and the need to create much more precise demand forecasts much earlier and to determine the necessary safety stocks.
Belimo, which is listed on the Swiss stock exchange (SIX), is the global market leader in the development, manufacture and sale of field devices for the energy-efficient control of heating, ventilation and air conditioning systems and employs around 2,300 people in over 30 countries worldwide. Customers of the products include OEM customers, system integrators and building technicians as well as tradesmen, who can also order Belimo products online.
The needs of these customer groups are heterogeneous in terms of order quantities and configuration requirements. There are also seasonal and product-specific fluctuations in demand. However, all customer groups want to be supplied within the shortest possible time at all times – even for the smallest order quantities. Belimo aims to meet this customer requirement in full at all times, because in addition to outstanding products, readiness to deliver is also a decisive success factor for the world market leader.
Achieving top performance on the operational side
“We want to inspire our customers with unique solutions and operational excellence,” explains Louis Scheidegger, Head of Group Division Production.
In order to be able to deliver this top performance globally, Belimo operates two production sites worldwide, nine local logistics and customization centers and more than 30 branches in order to be as close to the customer as possible and to be able to deliver ordered goods within a few days or even hours. Belimo’s suppliers, who deliver assemblies and components, are located upstream of the production sites, logistics and customization centers and branches. 88% of manufacturing costs are incurred in procurement and 12% are attributable to in-house value creation. Supplier management and procurement processes therefore have a correspondingly high priority for the high level of delivery readiness required. However, excellent procurement processes are not enough. The demand forecasts must also be correct.
Belimo prepares these at the level of the nine local logistics and customization centers and the two production sites. Three planning centers in APAC, America and Europe are responsible for this. The sales branches are stocked with standard products based on consumption. This means that if the order point is not reached, subsequent deliveries are made. With this setup, Belimo is very well positioned in the market. Previously, the company had used an internally developed requirements planning system that was integrated into SAP. It enabled a linear extrapolation of past values to the next 12 months and was no longer able to cope with the increased requirements and complexity due to the company’s growth and the demands of the supply chain. As part of the migration of the ERP system to SAP S/4, a decision had to be made as to whether this existing in-house requirements planning should also be migrated and optimized or whether there was a better solution, perhaps even off-the-shelf.
Facing the turning point
Optimization was sought here primarily due to growth, limited storage capacity and increased inventories due to supply chain problems in recent years. The aim is to forecast with much greater foresight and sophistication in order to reduce inventories without compromising delivery readiness. Belimo needed a longer forecast horizon than the previous 12 months in order to be able to procure motors and microcontrollers more efficiently, for example. Delivery times here are often over six months and suppliers want forecasts that go well beyond one year. In addition, the options for responding to different demand characteristics were not differentiated enough: there were hardly any options for adjusting consumption curves and forecast weighting factors. There was only one standard factor that could be adjusted.
Public vacations and vacation periods such as China’s New Year vacations or Thanksgiving in the USA had to be adjusted manually, and seasonal factors could only be planned manually. Belimo also has to adjust its forecasts for specific product groups in the fall months, as this is when the heating season begins and heating systems are serviced and replaced. Holiday-related shifts of requirements due to company vacations could also only be adjusted manually and were correspondingly error-prone and control-intensive in order to avoid errors and their effects. There was also insufficient support for the phase-in/phase-out planning of new and discontinued products.
Reporting was limited to what was possible within the in-house development in SAP. Classic key figures for planning accuracy such as MAD (Mean Absolute Deviation) / MAPE (Mean Absolute Percentage Error) or an evolution index could not be determined automatically, which only enabled rough KPI reporting.
Needs-based feature selection
Be able to select characteristics according to requirements
It was possible to forecast demand for product groups or individual materials. There were no aggregation levels or grouping options according to material characteristics that influence the forecast. For example, summarized forecasts for the global sales organizations, logistics and customizing centers, plants, regions or specific customers.
Today, Belimo plans with an 18-month forecast horizon and benefits from the diverse simulation functions offered by the DISKOVER Advanced Planning & Scheduling System from SCT, which is now being used. For example, to simulate how stock levels and demand forecasts develop when the target delivery readiness level is changed. Demand can now be analyzed and determined across several procurement stages. However, it was very important to be able to plan with different billing horizons and demand distributions. In the old system, these parameters could be set the same for all articles. This meant that demand patterns (daily, weekly, monthly, etc.) could not be reflected in the demand plan. Based on these and other characteristics, products can now be grouped together and thus planned more efficiently.
“Ultimately, DISKOVER’s flexible set of rules offers almost infinite possibilities for adapting the forecast to our circumstances,” says Stefan Herter, Head of Global Production Planning at Belimo Automation, with conviction.
Being able to forecast KMAT requirements
The planning of configurable materials (KMAT) at end product level was also very important. This is because customers can order drives with specific cable assemblies and connectors, for example. With more than 100,000 variant options, these configurable materials account for around 10% of Belimo’s sales. A very efficient solution therefore had to be created so that the costs did not exceed the benefits.
The planning of these items has now been implemented in two ways: SAP generates pre-planning parts lists based on the historical consumption of the components for the configurable drives. DISKOVER determines the consumption history and forecast at end product level, as DISKOVER can group the material documents to the customer order stocks. The forecast of configurable materials is allocated to planning materials and generates dependent requirements for components and assemblies via the planning BOMs. Belimo can now also control material changes and discontinuations using these pre-planning materials.
SCT has implemented a new forecast composition procedure in DISKOVER that transfers the remaining forecast of the configured end product for the current month and further periods to the planning material. “This is a very, very lean process that solves the problems of the past excellently, but is not oversized,” says Stefan Herter with great satisfaction.
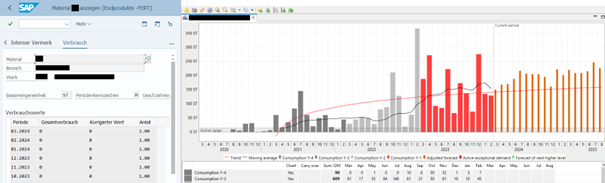
Demand forecast with APS system DISKOVER
Don’t throw the tried and tested overboard
Belimo has been using a simplified bearing characteristic curve method for safety stock calculations for several years. “It is easy to understand and can therefore be used by anyone,” explains Peter Neumüller, the project manager responsible for introducing DISKOVER.
Average and maximum rolling consumption in the replenishment lead time are offset against the desired degree of readiness for delivery in the inventory characteristic curve method. Taking into account the so-called C-norm factor, which defines the readiness for storage, the safety stock can thus be determined. Thanks to the modular software structure, this functional expansion was easy to implement, which helped Belimo a great deal. Thanks to the flexible set of rules, exceptions can also be easily identified and applied in the safety stock calculation.
The calculation of safety stocks was previously carried out on a quarterly basis using databases developed in-house, the analysis took many hours and the results had to be transferred to SAP using transfer files.
“The implementation of the inventory curve method was very important for Belimo and easy for SCT to integrate. In addition to the traceability of the calculation, we benefit greatly from the fact that the forecast and safety stock calculation could be realized in one solution,” says Peter Neumüller, welcoming this added value.
Powerful functional construction kit
Although the new APS system could also be used for real scheduling, Belimo has so far only used the demand forecast and the functions for updating master data and calculating safety stock and then transfers the data to the SAP system. Here, Belimo relies on existing methods and tools and has now created a particularly powerful, flexible modular function system to implement even the most complex demand forecasts more efficiently and make them available for daily scheduling, so that ultimately the desired high delivery readiness can be achieved with lower inventories. “The very flexible set of rules in particular means that better results can be achieved with less effort,” Neumüller is convinced. With a smile, he adds that he also greatly appreciates the automated reporting system and the flexibly configurable alerts from DISKOVER, especially as they are supplied free of charge.
Made by practitioners for practitioners
In addition to the product, Neumüller is also very satisfied with the consulting and services provided by the Abels & Kemmner consultants who accompanied the project, as well as the high responsiveness of the software supplier. “A key success factor for this project was the enormous expertise and practical knowledge of Abels & Kemmner and SCT as well as the very uncomplicated cooperation. The accessibility of the employees is very good. The speed of response is immensely high. Solutions are proposed within a very short time. In addition, services are provided in the interests of the customer without charging for hundreds of 15-minute tickets.” All in all, the introduction of DISKOVER is a complete win for Belimo Automation AG.
Authors
Tobias Brasch
Supply Chain Consultant at Abels & Kemmner Gesellschaft für Unternehmensberatung mbH
Peter Neumüller
Senior Project Manager – Project & Quality Management Production at Belimo Automation AG