Production planning with the support of artificial intelligence
The medium-sized paper and film refiner Sihl from Düren has raised its production planning to a new level.
With the support of artificial intelligence (AI) and the DISKOVER-PP/DS system from SCT GmbH, Sihl was able to replace its outdated provisional solutions with an integrated and transparent planning system.
Thanks to AI-supported machine allocation planning, the company now achieves better results much faster.
As a medium-sized company, Sihl is not a typical early adopter of new technologies.
When looking for a suitable PP/DS (Production Planning and Detailed Scheduling) system, Sihl was primarily concerned with replacing the many makeshift solutions resulting from outdated detailed production planning from the 1990s.
The primary goal was to create more transparency and more integrated planning.
But today, Simone Stahr, Team Leader Production Planning at Sihl, is delighted to have chosen a solution for her project with SCT and DISKOVER that already uses artificial intelligence (AI).
Mastering complexity with AI
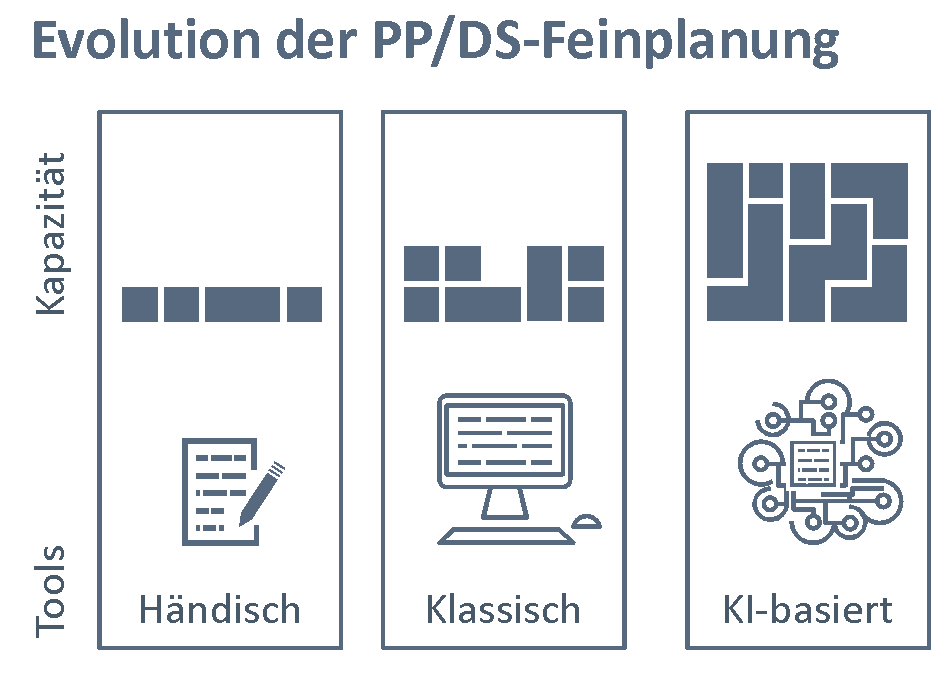
The detailed planning of production benefits considerably from AI, especially in view of the large number of machines, products, orders and delivery dates, which, in combination with fluctuating personnel resources, raw materials and set-up times, create an almost infinite decision-making space.
In complex production processes with numerous dependencies, it is extremely difficult to achieve the optimum overall result every day.
The dilemma of providing goods on time with the most efficient possible factory utilization and limited capacities cannot be optimally solved with simple machine allocation plans and classic calculation methods. However,
AI is able to cut through this Gordian knot with the help of heuristics and metaheuristics.
It can perform even the most difficult optimization tasks efficiently and automatically within seconds for each new order load.
The result: greater adherence to schedules, increased productivity of the entire factory with less planning effort and lower costs for the planning tools.
This means that even medium-sized companies like Sihl can now afford such advanced tools.
Paving the way: Consolidating data
But before the new, AI-supported PP/DS system could be put into operation, Sihl had an implementation project that required some essential preparatory work.
This was not about learning AI inference logic.
Rather, many of the measures to be implemented were necessary because the previous PP/DS system only offered a limited range of functions.
Over the years, the medium-sized company had developed numerous subsystems and isolated solutions that were maintained separately.
In order to enable fully integrated planning, it was necessary to merge the data from these systems.
The three production areas – paint production, large roll coating and subsequent converting, i.e. the process of converting the large rolls into customer products that can be ordered – had developed their own production programs over time.
There were Excel tables with additional information on individual work orders, and the paint shop had even created a query tool in Access in order to better orchestrate the work orders from the PP/DS system available in the production data acquisition (PDA).
As a result, different order, deadline and processing statuses existed in each system – from PP/DS and PDC to the Access and Excel solutions.
The critical coordination required to bring all areas up to the same status was correspondingly time-consuming.
Dissolving isolated solutions
In addition, paint production essentially acted as a supplier area for large roll coating, whereby the requirements in paint production were planned almost as if they were in an independent operation.
Due to the sequential individual coordination of these two production areas, there was a lack of transparency about the current status at the PP/DS planning level – which was actually supposed to provide the specifications.
As part of the introduction of the new PP/DS system, a lot of work was therefore put into defining cross-departmental standards and work schedules, which are now transparently available to enable integrated planning across the entire supply chain.
The master data of the ERP system also had to be optimized in order to optimally set all planning parameters.
Step-by-step introduction of DISKOVER PP/DS at Sihl
The new PP/DS system was successfully put into operation in the nine systems for processing large rolls at the end of 2023.
Sihl has been in the process of integrating converting since the beginning of 2024.
This involves cutting the large rolls into the blanks ordered by the customer, from large and small rolls to sheet formats.
The next step will be the introduction of the system in coating production.
The in-house system for production data acquisition (PDA) called Promas PDA, which is individually tailored to Sihl’s needs, has been retained as the key specifications have already been taken into account in the new PP/DS system.
This made it possible for the new PP/DS system to continuously write the specific work orders to the PDC system in the overall operationally optimized sequence.
This then makes them available at each machine – subject to the still individually possible interventions of the foreman or machine operator – records the actual processing and reflects this back to the PP/DS system.
The Access and Excel solutions only contain the specific work instructions for the order.
In contrast, all planning elements are stored as parameters in the PP/DS system.
How Sihl uses DISKOVER – and vice versa
The production plan, which is updated at the touch of a button, is also distributed to all other relevant systems and displayed there.
This enables a high, integrated level of digitalization to be achieved on all platforms.
Another new feature at Sihl is multi-resource planning.
This means that not only is a sequence planned on the machines that is optimal for the setup.
Instead, availability planning is also used.
This means that the system simultaneously checks whether all component and personnel resources are available in order to ensure that all the necessary framework conditions for the production order are in place.
This makes it even easier to avoid machine downtimes.
To this end, Sihl has also integrated work plan management into the PP/DS system.
Simultaneous planning of this kind is significantly more complex than traditional machine allocation and sequence planning, but results in more comprehensive and efficient production control.
The PP/DS system also supports setup matrix structures to enable integrated planning of all relevant framework conditions.
This function allows times and costs for machine changeovers to be automatically taken into account in every planning process based on holistic optimization considerations.
Sihl thus benefits from greater delivery reliability with minimized operating costs and at the same time has a significantly greater ability to react to changes.
The resulting agility is already paying off.
“Thanks to DISKOVER, we are now in a much better position than before,” explains Stahr. “For one thing, we have achieved an unprecedented level of data transparency. This makes it much easier for us to visually see delays or manual changes in the production plans and plan in a more integrated way. Secondly, we are now able to react in a highly agile way to extremely dynamic situations – such as corona, with staff absences and very fragile supply chains. We also see a major advantage in the fact that the system offers us a great deal of flexibility and openness overall.” For example, the reporting can be flexibly adapted with customer-specific fields, and numerous plug-in interfaces make it possible to take customer-specific calculations or individual setup matrices into account.
In addition to the DISKOVER PP/DS system, Sihl has also been using the DISKOVER APS (Advanced Planning & Scheduling) system for several years as a tool for daily scheduling. The solutions from SCT therefore map the entire supply chain at Sihl, including all value creation between the various production stages. Stahr appreciates the ease with which the newly introduced PP/DS system can be implemented. “The PP/DS tool from SCT is self-explanatory. You find your way around immediately, regardless of whether you are already using APS-Toll or not.”
It was also important to Stahr that the PP/DS could be efficiently integrated into the existing ERP system.
Stahr explains: “Docking with our customized version of the SAP ERP system worked extremely well for DISKOVER. DISKOVER PP/DS can integrate data very flexibly, which is very important for individually configured ERP systems.”
Conclusion
AI is no substitute for careful adjustment of decision parameters and restrictions, nor for strategic decisions as to which target function should ultimately be pursued.
However, once these have been set, AI-supported PP/DS systems can simultaneously evaluate almost infinitely possible machine allocation plans based on a carefully parameterized, highly complex target function.
At Sihl, for example, several 10,000 solution options are compared in each planning process, in a time in which a human could only calculate one or two plans.
The result is much faster generation of significantly better plans.
As a result, the PP/DS system has significantly improved the quality of production planning at Sihl, leading to more throughput per unit of time, better adherence to deadlines and higher productivity.
Stahr’s assessment of the project is positive: “Thanks to AI-supported machine allocation planning, we now achieve better results much faster than with conventional methods.
The fact that PP/DS consulting and software come from a single source has also proved its worth for us.
SCT’s support is also excellent.
We are always helped quickly and competently with problems or suggestions.”
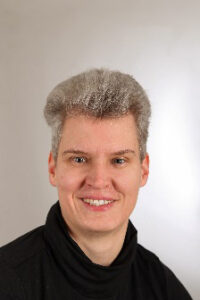
Simone Stahr
Team Leader Production Planning at Sihl
Simone Stahr co-authored this article.