First-hand insights: a look behind the scenes of our users
Roman Clausnitzer on the launch of DISKOVER at Kopp
To increase the efficiency of its processes, Heinrich Kopp GmbH has introduced the modular planning, analysis and simulation software DISKOVER from SCT.
Kopp, a leading supplier of electrical installation materials and technology based in Kahl am Main, develops, manufactures and distributes electrical engineering products worldwide via specialist wholesalers and DIY stores.
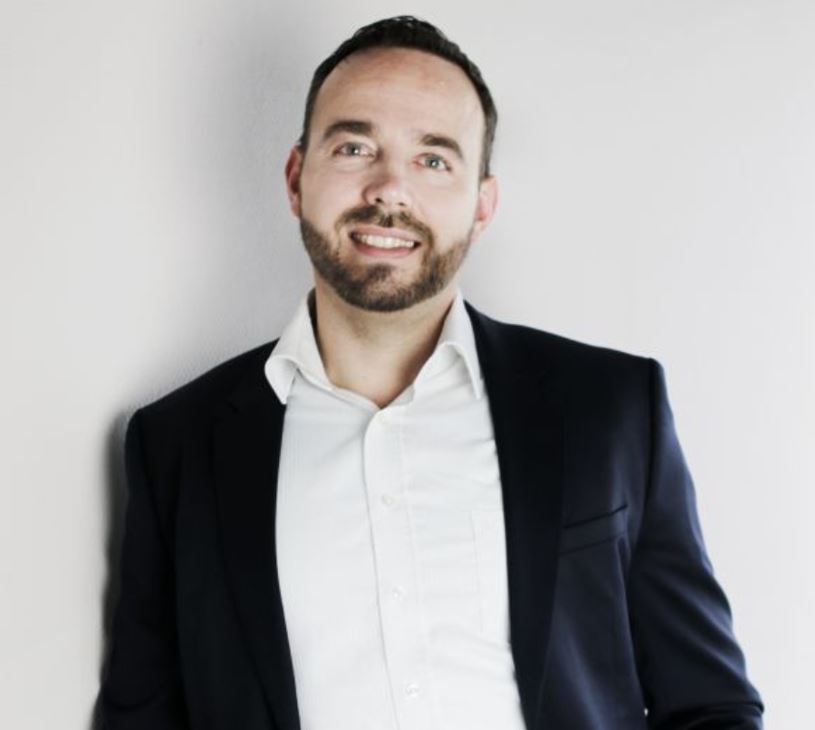
With around 7,000 products ranging from simple plugs, adapters and socket strips to mobile devices and innovative wireless systems for electrical installations, Kopp caters to both electricians and DIY enthusiasts.
In this interview, Roman Clausnitzer, Head of Purchasing and S&OP at Kopp, gives an insight into his experiences and reports on the changes and benefits that the use of DISKOVER has brought to Kopp .
Mr. Clausnitzer, what prompted you to introduce new scheduling software?
Our main driver was the need to optimize our forecasting accuracy and inventory levels.
Before DISKOVER, we had an automated but rather rigid process landscape that was based on historical data and offered little flexibility for adjustments.
The coronavirus pandemic has shown us that we need to react quickly to market changes.
With DISKOVER, we can now simulate different scenarios and adapt our planning dynamically, which is becoming increasingly important in today’s volatile market environment.
Fortunately, we had already started introducing DISKOVER before the pandemic.
Where do you stand today, what has changed at Kopp since DISKOVER?
DISKOVER has indeed brought us enormous benefits in terms of forecasting accuracy and inventory optimization.
Our forecasting accuracy used to be between 30 and 60 percent, today we achieve 70 to 90 percent.
This has a direct impact on our inventory management and delivery capability.
We have been able to reduce the number of stock-outs and optimize inventory levels at the same time.
The transparency of our processes has also improved.
We are now able to identify and resolve potential problems at an earlier stage.
We use the system to quickly and efficiently test various scenarios and generate graphical evaluations.
This not only saves time, but also improves the quality of our decisions.
At the same time, we have been able to significantly increase the competence of our employees, which has a positive impact on the entire organization.
Interesting.
The introduction of a new system is often associated with fears – the fear of not understanding the new system or the fear of losing your job.
How did you deal with this?
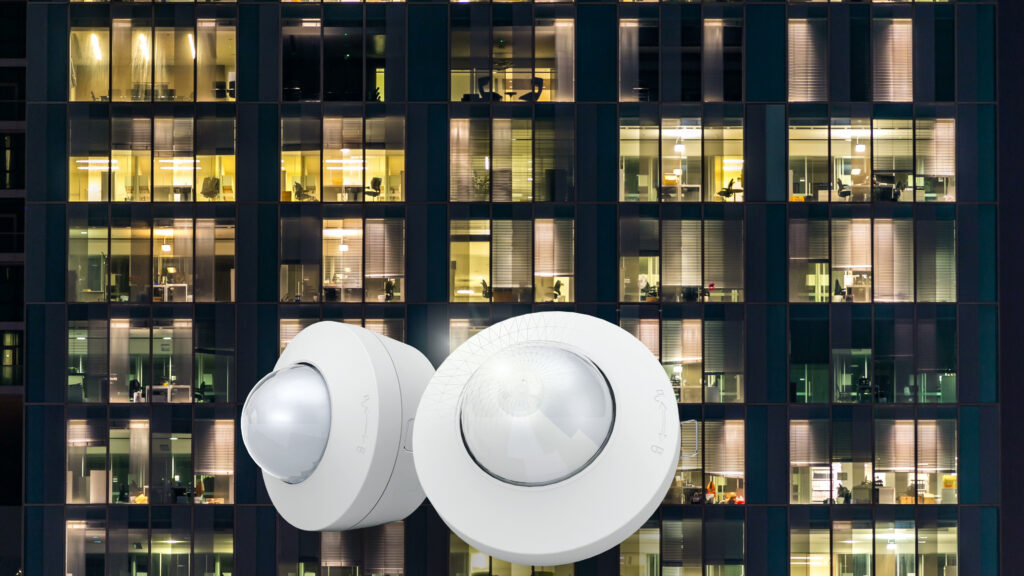
Training was a central part of the introduction of DISKOVER at our company.
We have invested heavily in the training and development of our team to ensure that everyone acquires the necessary knowledge and skills.
In addition to training on the system itself, we have also conducted theoretical training to provide a sound understanding of the planning and scheduling processes.
This training is not only important for the introduction, but is also repeated regularly for new employees.
Of course, there were concerns and fears at first.
However, DISKOVER was overwhelmingly well received by our employees.
The training courses certainly made an important contribution to this.
At the same time, many team members used the introduction as an opportunity to further develop their own skills and demonstrate their expertise instead of having to deal with routine decisions that the software can make itself.
Are there any highlights in DISKOVER that support your employees in their work?
In my opinion, an outstanding advantage of DISKOVER is the graphical support, which enables us to test different scenarios quickly and clearly.
For example, we can analyze the variability of the stocking time and we can immediately see how the stocks develop when we change the minimum batch size.
Another highlight is the ability to integrate non-DISKOVER users via automated forecasts and reports so that external partners, such as suppliers, are kept up to date.
We also make intensive use of the reporting system to create key figures and dashboards that are also accessible to non-DISKOVER users.
These features make a noticeable contribution to smooth collaboration.
I would also like to emphasize additional functions such as group scheduling, which helps us enormously when filling containers from Asia, as we can bundle and manage orders more efficiently.
And calendar control is important for us to be able to automatically take into account public holidays such as Chinese New Year or other local events.
These functions save us a lot of time and make the processes much simpler.
Looking back, where do you see the biggest challenges for successful implementation?
Implementing new software is not without its challenges for us either.
One of our biggest tasks is adapting existing planning processes and safety stock structures.
Safety stocks at component level, for example, did not previously exist in our system.
We used to work with blanket safety times.
Now, thanks to DISKOVER, we have more part-specific and automated control through a set of rules.
This has led to the scheduling department taking on new tasks.
We now have to examine how best to prioritize them.
The introduction of DISKOVER offers a wide range of options for optimizing planning and scheduling processes, resulting in more efficient and effective logistics:
Improved forecasting accuracy: The accuracy of sales forecasts has improved significantly, from 30-60% previously to 70-90% now.
This enables more precise planning and reduces over- or understocking.
Early detection of problems: With DISKOVER, pain points can be identified earlier, which is also an advantage in times of crisis, such as the corona pandemic.
Flexibility and adaptability: DISKOVER makes it possible to test and adapt different forecasting models quickly and easily, which is particularly helpful in the event of unforeseeable events or the introduction of new products.
Increased efficiency through graphical support: The graphical display of data and results facilitates analysis and decision-making.
Users can quickly simulate different scenarios and visualize their effects on stocks and stocking times.
Independence from IT: Many structural changes and strategic settings can be made independently without the need to involve the IT department.
IT does not have to provide any other capacity for user support.
If support is required for technical questions, the interpretation of planning decisions or the operation of the system, a personal advisor can be contacted directly at the manufacturer’s service center.
Time savings: DISKOVER’s comprehensive viewing options and ease of use save dispatchers time when analyzing and planning.
This is particularly useful in production-related areas where quick decisions need to be made.
Functions such as group scheduling and calendar control facilitate the handling of complex scheduling tasks.
Extended reporting functions: DISKOVER offers extensive reporting functions that make it possible to create key figures and dashboards and integrate non-DISKOVER users.
Automated forecasts and supplier connections facilitate collaboration and optimize processes.