Most production and trading companies are swimming in money, but they can’t get their hands on it.
Why this is the case and how you can do better!
Companies never have enough liquidity, even in good times. This becomes even more important in difficult economic phases, but it is often more difficult to obtain bank loans. According to the Ifo Institute, the proportion of industrial companies in Germany with lending difficulties rose from 26.2% in June 24 to 34.3% in September 24.
Many companies would need less or no money from the bank. However, for many companies, financial resources are tied up in stock. In our experience, around 75% of companies could reduce their inventories by at least 20% without compromising their ability to deliver. Unfortunately, most companies fail to free up this liquidity because they significantly underestimate the scale of the challenge. Effective inventory management requires more than just common sense and superficial observation.
By evaluating Top1o and Flop10 stock lists and manually intervening in replenishment, you can temporarily reduce stock levels with great effort, but this usually damages delivery readiness, fuels the whip effect and often even increases stock levels in the medium term.

Why it is so difficult to reduce inventories effectively and continuously
Three main causes are at work here:
Cause 1: Stocks change abruptly and not incrementally.
It is virtually impossible to deflate the stock of an isolated item without jeopardizing the ability to deliver. The stock of an item cannot be compared with the water level in a hot water boiler. Although (water) stock is also taken irregularly from the hot water boiler, water can be refilled immediately and in fine doses: Delivery time towards 0; minimum refill quantity towards 0, fixed jump water quantity towards 0. With the hot water boiler, you have quickly worked out how much water stock is required so that everyone can take a hot shower (readiness for delivery fulfilled) and unnecessary water quantities (excess stock) are not heated.
How would you set the stock in your hot water boiler correctly if you had to order water from the waterworks three months in advance, always have to order at least 100 liters and then be allowed to increase the order quantity in 50 liter increments? What level of water should be kept in the hot water boiler? Surprisingly, the answer baffles some practitioners, even though they face this challenge every day. There is no exact stock level that has to be maintained and that you can use as a guide. The stock always jumps up and down a lot. However, using suitable statistical methods, it is possible to determine a required average stock level, which is almost never exactly the same in the boiler, but around which the stock level must fluctuate in order to always be able to shower without wasting energy.
This average stock is the result of skillful management of inflows in response to irregular outflows. Sharp thinking and a supposedly correct gut feeling do not lead to the desired average stock, which brings us to the second cause!
Cause 2: Inventory management is a statistical task
Inventory management is not a mechanical mechanical interplay of stock levels, delivery readiness levels, changes in demand and replenishment times, but a statistical. Dieses Zusammenspiel kann man nicht durch gesunden Menschenverstand steuern, sondern nur statistisch beherrschen. Der Mensch hat jedoch keinen sechsten Sinn für Statistik, sonst würde niemand Lotto spielen.
Unfortunately, the challenge is even greater:
Cause 3: Readiness to deliver depends not only on the stock of a single item, but also on the interaction of all internal and external stocks
It is almost impossible to reduce stocks without taking into account the delivery and parts list relationships between the stock levels without impairing delivery readiness and causing a bullwhip effect at the same time. Isolated inventory reductions for individual materials or inventory levels therefore not only jeopardize the availability of goods, but also increase inventories in the medium term.
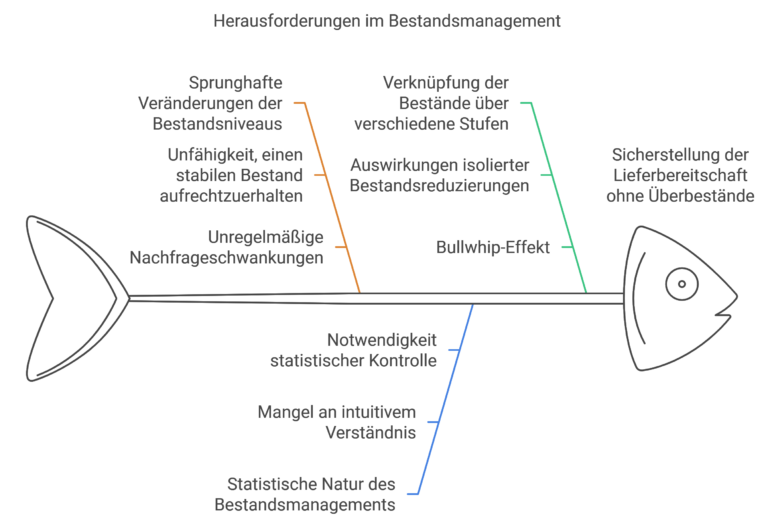
How to effectively reduce and permanently avoid unnecessary stocks
As inventory management is a statistical challenge and stock levels cannot be controlled by turning a tap, you need suitable algorithms that tell you when to order what and in what quantity. Your ERP system could possibly do this, but it doesn’t because the algorithms are set up incorrectly and fed with the wrong data. Sometimes the ERP system does not even have the necessary algorithms.
To ensure that your ERP system works at least as well as possible, if not always as well as necessary, you need to know how the planning and scheduling algorithms in an ERP system work and how they can be changed by setting parameters.
You also need clear rules on which algorithms are required for which article properties and under which boundary conditions, and how the parameters that control the algorithms must be set.
These rules mean that the algorithms that regulate an item’s inventory are constantly readjusted and changed, depending on the item’s life cycle, its market conditions, its interaction with other items and much more.
Ultimately, you must be able to determine the correct settings using simulation, as the correlations and effects of scheduling decisions in the value chain cannot simply be calculated due to the aforementioned statistical correlations. Simulation” does not mean the naïve extrapolation of stock trends into the future, as is done in the item stock list of an ERP system. Here, ideal conditions that never exist in reality are used. The market orders as planned, material is delivered as expected, disruptions do not occur in this fairytale world. No reliable findings on parameter settings can be gained from such extrapolations.
In order to obtain practical rules for setting the planning and scheduling parameters, you need to work with empirical data from the past, which contains all the unreliabilities that an internal value chain and an inter-company supply chain have to cope with.
In a digital twin (a simulation model) of the value chain and supply chain, this empirical data can be used to test and optimize the necessary adjustment rules. The interaction between the various inventory levels is also implicitly taken into account.
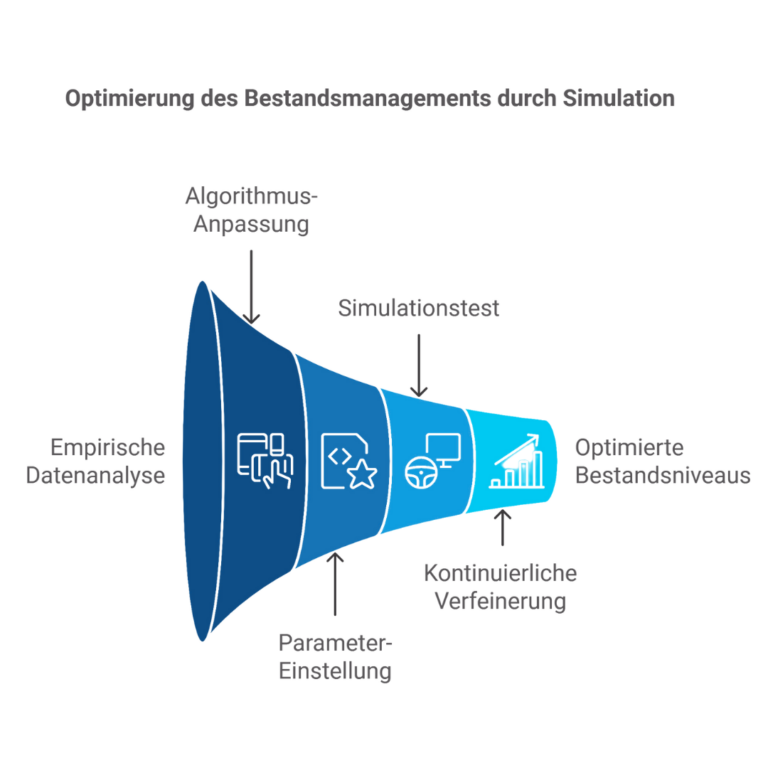
Do you not have the knowledge and tools required? Then you are in good company. Only a few companies can do this.
But that doesn’t matter and is neither necessary nor useful. You probably can’t repair your hot water boiler or control your central heating yourself either. It makes sense to call in the appropriate specialists.
The basic principle behind every make or buy decision is not to do anything yourself that others can do better and cheaper and that is not part of your own core competence.
So leave it to us to get your stocks under control. As specialists in inventory management, we have the necessary tools, years of experience and routine in their use. We will help you to join the ranks of the few companies that really have their stocks and delivery readiness under control, stop wasting valuable liquidity in the warehouse and manage your value chain more effectively and efficiently.
Or do you want to continue?
- Wearing out their dispatchers in battles against excess stock that they cannot win,
- lock up their liquidity behind stock gates that they cannot open, and
- endure monthly inventory costs that reduce your profits and that you could easily use to finance effective inventory management?
In the long run, only power helps, waving flags leads to nothing.