The requirements planning cake: allocation horizons and planned value distribution as basic ingredients
At the weekend, my almost three-year-old daughter baked a cake for me for the first time – with the active support of her mother, of course. The joy was huge, and my little one’s eagerness to carefully weigh the ingredients and mix everything together properly was heart-warming. However, as is the way with small children’s hands, the sugar was measured very precisely, while the flour went into the bowl more “by feel”. And the fact that our oven doesn’t keep its temperature quite as reliably as the display indicates gave the baking result a very special touch. The cake was still delicious, but such an approach would be less likely to lead to success in demand planning.
The “cake of requirements planning”: Allocation horizons and planned value distribution as basic ingredients
What I have learned over the years is that many companies make a very similar mistake in the area of requirements planning: in some areas, they focus on the last decimal place – the “10 or 10.2 grams of sugar” – and overlook the core settings such as the allocation horizons and the planned value distribution, which correspond to the basic ingredients in requirements planning. Just as with cake, it is crucial that the basic ingredients – in this case the correct parameters in the planning – are correct. Attempts are often made to minimize forecasting errors with AI, but the major improvement in planning results usually fails to materialize if the basic parameters are not set correctly.
Calculation horizons: the measure for reliable planning
The allocation horizons (backwards and forwards) are core settings that many companies do not pay enough attention to. These parameters determine the horizon over which planned requirements and actual requirements – e.g. sales orders – can be offset against each other. If the horizons are too generous, sales orders can consume too many planned requirements and the total requirements are often underestimated. If, on the other hand, the allocation horizon is too short, too many unallocated (and often no longer required) planned requirements remain and the actual demand is overestimated. The result: excess stock!
Planned value distribution: Planned values should be based on the distribution of actual requirements
The planned value distribution is another cornerstone. It determines how a forecast is broken down over the planning period (usually the month). It is important that the way in which the forecast is broken down over the days or weeks of the month comes as close as possible to the usual demand for a material. Good software tools such as DISKOVER can help to fine-tune the planned value distribution so that it perfectly matches the actual demand profiles.
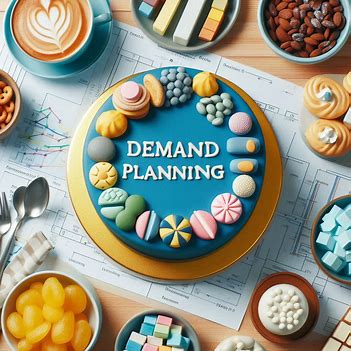
AI-supported forecasts are often just the icing on the cake
Of course, AI-supported forecasts are an exciting field, but I can say from experience that they can only improve forecast quality in a meaningful way if the fundamentals are right. The best icing on the cake is of little use if the rest of the “cake” is not successful. You can think as much as you like about whether it should be 10 or 10.2 grams of sugar, but if the flour is only correct by eye and the temperature of the oven is incorrect, the end result will suffer considerably.
As with so many things, the same applies here: A chain is only as strong as its weakest link. In demand planning, the weakest link in many companies is not the forecast, but the correct setting of parameters such as allocation horizons and planned value distribution. As long as these are not correct, the result will always fall short of its potential – no matter how good the forecast is.
Conclusion: First the basics, then the finishing touches
Experience shows that companies often try to get the most out of their processes with marginal AI improvements, but overlook how important the basic settings are. So if you really want to optimize your demand planning, you should first set the basic parameters – the “flour percentage” and the “temperature” – correctly. This not only makes the “cake” of demand planning efficient, but also provides a reliable basis on which further optimizations can be built.