Making multi-stage inventory optimisation processes more efficient
The next generation of multi-echelon inventory optimization needs artificial intelligence
Multi Echelon means “multi-level” in German. In inventory management, multi-echelon inventory optimization (MEIO) ensures that stocks at several locations and warehouse levels are optimized holistically. Such processes are complex. Artificial intelligence helps to get this complexity under control.
Internal and inter-company supply chains consist of the interlinking of several locations or warehouse levels. Different items are stocked in each location and there are stock transfer relationships or relationships between the locations that result from the bills of materials. In order to correctly control the stock of an individual storage level, two key stock parameters are generally required. One is the base stock and the other is the safety stock. The base stock is normally calculated from the restocking time multiplied by the average daily consumption of the item.
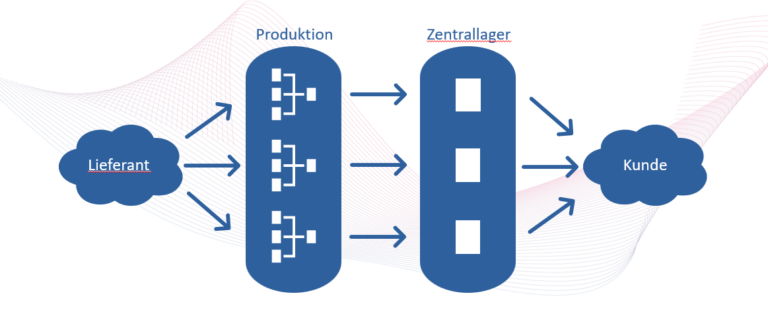
Several stages influence readiness for delivery
In addition to the replenishment lead time, the required degree of readiness for delivery is also included in the safety stock. The higher the required degree of readiness for delivery, the higher the safety stock. If an isolated storage level is considered alone in order to calculate these two stock parameters, it is normally assumed that the upstream stock level is basically able to deliver, i.e. has a degree of readiness to deliver of 100% and can therefore always deliver the requested material quantity after the replenishment lead time. However, this assumed concept is not realistic. Typically, the supplying stock level, i.e. the stock level that supplies to the stock level currently being considered for the calculation of its control parameters, also has a degree of readiness to deliver of less than 100%. For example, if the submitted inventory level has a degree of readiness to deliver of 98% and can usually deliver within five days, this means that 98% of the requested quantity can be delivered within five days.
This leaves 2% of the quantity that cannot be delivered within these five days because it is not available at the supplying stock level. In this case, the supplying inventory level must therefore fall back on its pre-delivery level. If we assume that the replenishment from the pre-delivery stock level takes seven days, it can be stated that a delivery time of twelve days is required for 2% of the delivery quantity in the above example. However, only 95% of this pre-delivery stage can be delivered. For 5% of the 2% of the delivery quantity, the delivery time is therefore further extended by the delivery time of the pre-delivery stage. This must be taken into account when determining the inventory control parameters of the inventory stage in question in order to actually achieve the required delivery readiness. In an internal value chain, as in inter-company supply chains, we are very often dealing with far more than three inventory levels that are interlinked, so that the example given is distributed across many inventory levels. If you have several interlinked inventory levels and are looking for the optimum inventory level across all inventory levels, the question arises as to what safety stock you should set for the various items at the different inventory levels in order to ultimately meet the delivery readiness to the end customer that is required and, on the other hand, to be able to keep the total inventories in the value chain as low as possible.
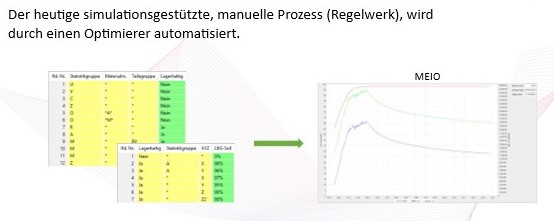
Optimization problem with large search space
This problem is an optimization problem with what mathematicians call a large search space. This means that it is not possible to try out all conceivable solutions using classical mathematical methods. In practice, therefore, multi-level stock optimization is usually dispensed with and the stock is set in isolation for each stock level, independently of the value chain and the other stock levels. The approach of using rules of thumb to define the inventory levels at which safety stock should be held, as is the case with DDMRP (Demand Driven MRP), goes a little further. Criteria such as critical components, long delivery times or high fluctuations in demand play a role here. At the points at which the decision is made in favor of safety stock, a safety stock is then determined again in isolation for the stock level and without taking the statistical supply reliability into account.
Although classic inventory management in multi-level supply chains feels transparent from the user’s perspective, as each inventory level represents a small world in itself, for which an attempt is made to achieve a reasonable compromise between delivery capability and inventory levels, at the end of the process chain this leads to a situation where delivery readiness cannot be achieved or can only be achieved with excessive inventories.
It is theoretically clear that a clever distribution of stock across the various stock levels leads to lower stock levels and more reliable delivery readiness, and in simple constellations this is also recognizable in practice. However, as soon as the value stream and supply chain become more complicated, the distribution of stock can no longer be calculated; the number of parameters is too large and the number of solutions that need to be calculated increases exponentially.
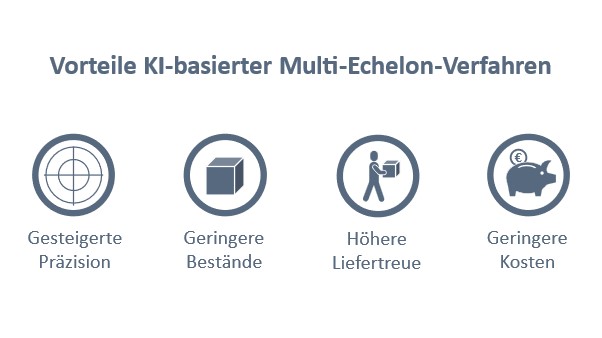
Delivery readiness with low capital commitment thanks to MEIO
Multi-stage inventory optimization can only be solved with the help of mathematical optimization methods. SCT GmbH from Herzogenrath near Aachen has developed a particularly efficient approach. Its new Multi-Echelon Inventory Optimization (MEIO) process, which is now available as an extension to the DISKOVER software suite, optimizes the interaction between the individual stages of the value chain based on state-of-the-art heuristics and metaheuristics from the field of artificial intelligence (AI). The aim is to distribute stocks across the entire supply chain in such a way that the required delivery readiness at the end of the supply chain can be achieved with the lowest possible capital commitment.
The result: greater adherence to delivery dates with lower inventories across all warehouse levels – with less planning effort and lower costs. This solution is particularly relevant for companies with three or more warehouse levels, from procurement to production and distribution.