In materials management, the term ‘MRP process’ refers to the mathematical methods in business software that are used to identify when material needs to be replenished. MRP procedures can be divided into three basic forms and mixed forms: sales order-based MRP, plan-based MRP, consumption-based MRP and mixed forms of plan and consumption-based MRP, such as DDMRP.
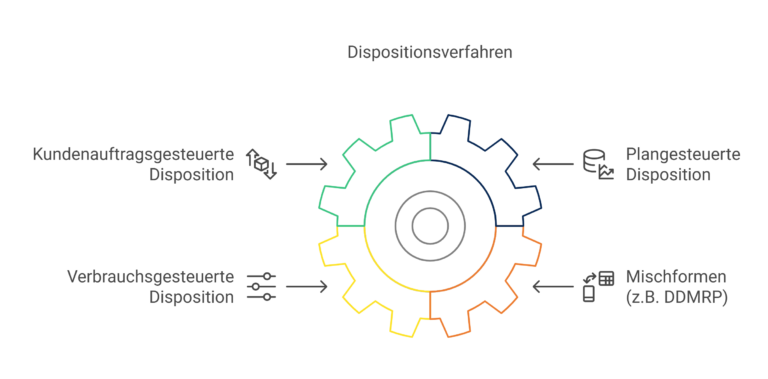
From the logistical decoupling point downstream of the value stream to the customer, customer order-driven replenishment is always used. Upstream from the logistics decoupling point, plan-controlled, consumption-controlled or mixed forms of MRP can be used. All of these MRP methods have their advantages and disadvantages and must therefore be selected depending on the MRP situation of an item (more on this in other articles).
Our tip:
The term is often misunderstood – and incidentally also incorrectly described by Microsoft Copilot – as a summary of all methods for planning and controlling material stock
As MRP procedures ultimately only determine the date on which the order is triggered and, depending on the procedure, also the material requirements date, they only represent one half of the material requirements determination. The other half, with which the order quantity is determined, is taken over by the lot-sizing procedures.
A successful scheduling strategy requires the skilful combination of the right scheduling procedures for the situation with the right lot-sizing procedures for the situation.
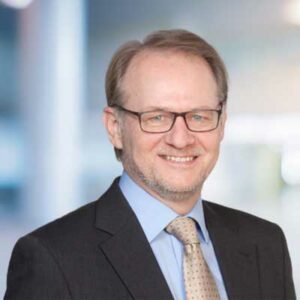