An article by Burkard Kiesel ea.
Ensuring that supply is always on time while reducing the inventory means a challenge to all stakeholders of a supply chain. A rough calculation is not enough; only the sharpest pencil will give us exact results.
Only a few years ago, Montblanc´s range of products included less than 1000 different models. The sales forecasting for Montblanc´s luxury goods, including the regional splitting factor was realized monthly by the individual distribution units. The data were then centrally collected and processed according to procurement and production requirements and the supply of the regional inventories. Today, with more than 1,000 product groups and 3,000 items, this forecasting methodology appears too complicated and involves too much workforce. In addition, the accuracy of this method began to deteriorate. Management therefore started re-engineering the whole forecasting procedure in Spring 2001, from budget planning through forecasting to rolling – monthly – demand planning and supply of regional inventories.
The result is a clear distinction between strategic and operative planning. Today, the planning input of the distributors concentrates on the strategic planning on a highly aggregated product level with approx. 120 positions to determine the “track” for production and procurement. The operative planning, however, is dedicated exclusively to the item level and subdivided into two feedback control systems operating independently from one another but following the same methodology.
For the supply of the regional inventories, a replenishment system has been implemented, which is controlled by regional logistic managers with clear responsibility for their inventories.
At the same time, the role of planning and inventory at the Hamburg location was strengthened considerably: the central inventory at Hamburg is now responsible for securing the supply. In order to be able to fulfil this new task, a two-step planning approach has been developed in cooperation with Abels & Kemmner consultants:
- The Logistic Category Managers, assigned according to product areas, are responsible for sales forecasting of items from the central inventory. Their main task consists in forecasting as exactly as possible future demands per item considering all information available. In this forecast capacity limits are not considered in a first stage. The Logistic Category Managers are responsible for as exact a sales forecasting as possible and are measured according to the quality of their forecast.
- The data determined by the demand forecasting process are then used to balance the production capacity and to coordinate the procurement of components with suppliers. Peaks in demand expected in future can now be identified and managed in time.
By way of implementing this planning approach, the items are analysed according to their predictability by means of DISKOVER 4.1, an MRP-optimizing software developed by Abels & Kemmner. Then, the system determines the optimal planning methods and parameters for the items identified as predictable. AB-XY items (approx. 30% of all items), which can easily be forecasted, make up for 66% of the turnover and more than 75% of the annual production capacity. For these items, DISKOVER forecasts future demands and forwards the data to the sales-and-operation-planning function (SOP) of the SAP system. In order to coordinate the data with the production programme planning, the SOP planning table was adjusted so that it can be used as a central planning tool: on the basis of the forecasted demand, production and procurement quantities are planned monthly – rolling – according to the demand and following the supply chain with regard to the capacity load of workforce and machinery. In the case of capacity overload at some stage, necessary measures – such as advancing part of the quantity required – can be identified in the SOP table and pre-planned at an early stage.
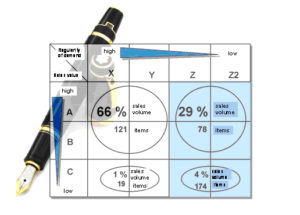
Structural approach to optimize sales forecast according to items
In order to determine the appropriate planning method per item within the sales forecast, the structural approach to the classification of items, developed by Abels & Kemmner, was implemented: The individual demands for each item by all distributors will be cumulated and examined according to their importance for turnover (ABC analysis) and current demand behaviour (XYZ analysis). This examination is realized by means of the MRP-optimizing software DISKOVER 4.1 developed by Abels & Kemmner. The demand behaviour examination is also based on an analysis of the trend and seasonality per item and the examination of the regularity of demand. Each item is therefore differentiated into an ABC category and an XYZ category. The results of such an analysis can be shown in an aggregated ABC-XYZ portfolio.
Figure 1 shows an example of such an item portfolio for one main product category. X and Y items show a regular demand behaviour with small to medium fluctuations. These items can easily be forecasted. Z and Z2 items, in contrast, are characterized by occasional demand and are subject to considerable fluctuations without previous notice. Future demands of this category are difficult to forecast. This is why other planning methods seem appropriate, e.g. order point or minimum inventory methods. The determination of the optimal planning methods and parameters as well as the identification of resulting inventory levels according to desired service levels per item category are also realized by DISKOVER 4.1. The expected average inventory per item according to different service levels is simulated and an optimal combination of methods and process parameters is selected so that the required service level is achieved at a minimum average inventory. Integrated in this simulation is the determination of the safety stock. The overall forecasting accuracy depends on the right combination methods for demand forecasting methods and for safety stock calculation. Then, the values for X and Y items are forecasted for the sales planning and submitted to the SOP (Sales and Operation Plan) module of the SAP system. Reorder point and safety stock are determined for Z and Z2 items and submitted to SAP for order point planning. The task of the Logistic Category Manager consists in verifying the submitted planning values within the SOP planning table. To this end, the planning table has been adjusted (see figure 2). In principle, the Logistic Category Manager disposes of both last month’s forecast and the current forecast. He decides which forecast to use for the further planning of the item. In addition, he can consider – on the basis of the trend report or in the case of non-forecasted special orders – additional demands by means of a percentile overhead or exact additional amounts per month. All required volumes are then cumulated to the (total) sales. The line “(total) sales” shows the decisive number of items calculated per month for production and procurement.
The SOP table is also to be used for production control and procurement planning: on the basis of the expected sales and considering the capacity resources of workforce and machinery required along the supply chain, production and procurement volumes can be planned in time or part of the volumes required can be ordered in advance. This is especially important for Montblanc, as seasonal demands play a decisive role; coordination and adjustment is therefore inevitable especially for the quarters with a high turnover. The key figure of this coordination procedure is the targeted inventory. The targeted inventory as well as the planning values of the forecast are determined by DISKOVER and submitted to SOP. This targeted inventory includes a safety stock also determined by DISKOVER. It is supposed to guard against coincidental and unforeseeable deviations from the planning data occurring in future periods. The production control varies the production and procurement volumes in a way to avoid capacity bottlenecks on the one hand and on the other make the targeted inventory always available, also in future planning months. In this context, SOP allows the current capacity situation to be identified resulting from the finished products to be manufactured each month. All capacity loads concerned may be shown for every planning month and for the actual item or planning category. If there is a capacity overload in one planning month, the planner can split the volumes of finished items and bring them forward in order to put volumes in demand in whole or in part off to earlier months and avoid impending capacity bottlenecks. At Montblanc, this coordination in the future will also include the main suppliers (e.g. of leather products), which allows an adjustment of the capacity along the whole supply chain at an early stage.
The presented planning methodology was first tested for two product categories. Since February 2003, it has been applied for all product categories, securing a 98 % service level to the regional inventories.
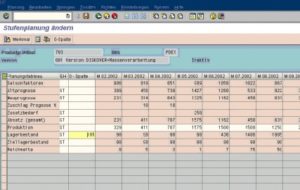
Learning to play your cards right: Kanban halves production inventory
After concluding the re-engineering of the sales forecasting process, the project focused on securing the replenishment of the central inventory in Hamburg and on reducing the lead time and the work-in-process inventory. Due to the large vertical range of manufacture, the long time required for re-procurement and the wide, and continuously growing, variety of products, efficient value chains were to be realized by establishing decentralized kanban control cycles; These kanban control cycles were designed to reduce the supply risk on all production levels to a minimum. The MRPII logic applied (see figure 3), which requires a high amount of coordination, did not lead to a satisfying result. The procedures applied before lacked flexibility, especially in the case of short-term fluctuations in demand of some final products. In order to guarantee the required service levels on the market, oversized inventories were required throughout the whole value chain up to the finished goods inventory.
At Montblanc, the optimization of service levels while reducing inventory was mainly achieved by the establishment of a just-in-time final assembly and a shift of the inventories from the final product with its numerous variants to the variant-building level of components.
The analysis of the throughput and setting-up time showed that a JIT manufacture was possible without much additional cost. Installing a JIT manufacture, however, requires a secure supply of the final assembly with components and external parts. For this reason, a central kanban inventory was put before the final assembly, which is controlled via a number of kanban control cycles in previous production phases. At present, the suppliers are being incorporated one by one into the system.
Thanks to precise planning within the kanban system and due to intensive and thorough preparations, the kanban system could go live without major problems. Within only three days, all the preparatory work for the switch to the new system had been completed. Given that kanban systems are self-controlling and generally do not require an additional IT system for production control, the kanban system at Montblanc was designed so as to run even without the SAP system in operation. To this end, a so-called signal kanban has been implemented. This is a kanban system ruled by kanban cards exchanged between internal or external suppliers and internal consumers. However, in a signal kanban system, the receipt of a single kanban card by suppliers does not trigger an additional production order; this can only be started after a minimum amount of cards has arrived (yellow area) and must be started after a maximum amount of cards has been received (red area). In contrast to simple or box kanban, a signal kanban has the advantage of reflecting different production lot sizes between different production departments in a simpler way.
In order to be able to introduce the kanban system, the SAP processes were reorganized in a first step so that they would not obstruct the procedures of the kanban system by creating more administration work. In a first step, when starting the production of one lot, the workers only opened a production order and registered it after its completion. No other SAP processes were involved. All inventory and stock transfer entries were already realized automatically in the background. In a second step, the kanban system was linked more closely to the SAP system. To this end, SAP´s own kanban control system was introduced. The opening and closing of the order is now realized automatically by scanning the bar codes of the kanban cards. In order to safeguard simple, easy and clearly arranged processes in practical operation, a number of details had to be considered in the design and preparation of the implementation.
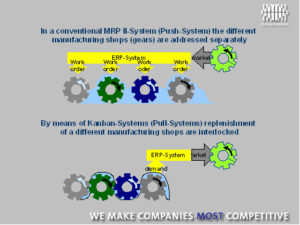
Implementation and introduction
The introduction of the kanban system required a change in the working habit and behaviour of the workforce involved at Montblanc. This change was also necessary because the production control was decentralized back to the individual production departments. Problems that occur in many companies when introducing kanban systems are often due to the lack of a clear definition of the rules of the kanban system and the unwillingness of the workforce to comply with these kanban rules. For example, products are manufactured in advance; components are stockpiled while lot sizes and throughputs are not attended to. If the workforces involved are not convinced of the kanban system, they will not comply with its rules and the system will be obstructed. One main reason for the success in implementing kanban at Montblanc was, therefore, the integration of the workforce into the design of the system. All organization procedures were worked out together with the staff of the production department involved. In this way, the staff had confidence in the design and an understanding of and even identification with the overall procedures, and the detail processes of every production department were fostered.
In general practice, many companies experience disasters during the introduction phase, because the kanban system has not been adjusted to the reality of the manufacturing processes. At Montblanc therefore, before designing the kanban control cycles, all relevant materials, information and order execution processes have been recorded and tailored to the requirements of the kanban processes together with the staff of the production departments. The processes have been analysed according to the following aspects in the process:
- Is it possible to realize a flow production across the production departments without establishing kanban stocks?
- In case kanban stocks are inevitable, can they be established on a lower value step or before a variant-building production step?
- Can the time required for production and setting-up and the lot sizes be reduced?
- Is the stability of the process sufficient to guarantee certain production times and can the quality of the process be controlled?
- Is the capacity situation (workforce / machinery) sufficient or sufficiently flexible to guarantee supply safety?
- Is the staff disciplined and qualified enough to manage the kanban system?
All major reorganization potentials identified at Montblanc during the development and design of the kanban system have deliberately not been attended to until some date after implementing the kanban control system. This was sensible because practical experience with the new system could be gained only after implementing kanban; this experience influences the decision how, to what degree and in which time other reorganization potentials identified could and should be made effective. In addition, this approach avoided doing the job twice and guaranteed that acceptance problems due to other reorganization measures that were adopted with the introduction of kanban, were not projected onto the kanban system itself. Finally, the implementation of the kanban system should not be delayed due to other reorganization projects.
One size does not fit all
At Montblanc, the range of items with their different characteristics means very different requirements to the design of the kanban feedback control systems. There are production-processes working with high lot sizes due to the process applied, and there are other areas characterized by minimum or no preparation time at all. The different requirements implied could only be met with the design of equally different kanban systems. The real design of every single kanban control cycle and the determination of the number of kanban cards to be used were therefore put on a broad mathematical-analytical basis. When conventional kanban control cycles are designed, only the re-procurement time per kanban, the average consumption of the item (related to past experience), the amount per kanban box and a so-called safety factor usually are considered. According to this methodology, the number of kanban cards used and therefore the inventory level depend mainly on a factor determined not mathematical-analytically but on the basis of a mere “feeling”. Important data for further processing such as
- lot size of the supplier (collective kanban).
- lot size / consumption of the customer.
- consumer behaviour of the item (XYZ behaviour) and the right safety inventory.
- scrap rate, and
- future consumption
often are not considered at all. An optimization of inventory, lead time and service level can be achieved by this simplified kanban design only in a limited way. Overstock and understock in the kanban system require “fumbling around” during months or even years, can lead to acceptance problems and finally to inactivating the kanban system. This is the second main reason – next to not involving the staff in the design – why many companies find kanban systems difficult to introduce and do not achieve the desired results.
One major weakness in designing a kanban control cycle can consist in a calculation based on consumption in earlier periods. When designing the Montblanc system, “future” consumption, that is a rolling sales forecasting for basic consumption values, was considered. This was possible due to the formerly revised, high-performance sales and production forecasting. kanban at Montblanc therefore turned out to be a proactive, not a reactive, process.
Another weakness of operating kanban systems often consists in the lack of a periodical adaptation of the kanban stocks. However, a quick and easy adaptation of the kanban stock must be possible, either periodically or when required, e.g. when sales forecasts are modified or production parameters changed. At Montblanc, this is the responsibility of the production control department. This department recalculates the kanban stock of every single item as required or periodically by means of a SAP-ABAP programmed by Abels & Kemmner on the basis of its special kanban calculator. As a result, the kanban cards required per item, among other values, are recalculated. When the number of cards is increased, additional cards have to be introduced into the system, and when the number of cards is reduced, cards have to be removed from the system.
The kanban calculator by Abels & Kemmner used for the dimensioning of the kanban control cycles not only helped to determine the actual number of kanban cards required per item and per kanban cycle. It also calculated the yellow and red areas of the kanban boards and realized a simulation of the capacity situation of every single production department. This simulation determines the maximum and minimum number of setup cycles per time unit and compares them with the current capacity situation. In addition, the stocks required for the kanban items are sized by calculating the minimum, average and maximum area required per item and kanban stocks in the course of time. The data obtained formed the basis for the procurement of sufficiently large kanban boards and shelf systems.
ERP systems and kanban
Since kanban is a self-controlling system, it generally does not require an additional MRPII- or ERP system. For this reason, an existing ERP system should not be forced into the kanban system. It is much more important to see to a logical interface between the ERP system and the kanban system. At Montblanc, kanban was therefore designed in a way to run production basically without the operating SAP system. Nevertheless, the production processes had to be reflected in an MRPII- or ERP system for invoicing, procurement and inventory planning purposes.
Why not recur directly to the kanban function available in many ERP systems and do without the manual kanban system? A kanban system is mainly characterized by visualizing all processes for the whole staff. This visualization is not available in an ERP system. However, it provides the individual production departments with a completely new overview.
At Montblanc, for instance, SAP kanban is operated in parallel with the manual kanban system, and normal users are not even aware of it. They only set a different status in the system by scanning the bar codes on the kanban cards. The materials balance in the SAP system is also synchronized with the physical changes in the inventory. Another disadvantage of a kanban control only through the SAP system would be that the SAP system still shows important weaknesses in kanban design and does not offer a direct solution for the realization of collective kanbans.
One frequent objection to the kanban system is that there is no room in the production site for a kanban inventory and kanban board. However, our experience has shown that after switching to a kanban system, there is more room available than is required for the kanban system. In order to identify kanban boards that are easy to read and yet require little space, Montblanc and Abels & Kemmner worked closely with Orgatex GmbH at Langenfeld, a leading manufacturer of kanban organizational materials. This cooperation resulted in the development of a kanban folding board that now forms part of Orgatex´ standard programme.
The results in short
- Forecasting method rearranged
- MRP planning optimized by linking SAP R3 (SOP) to Diskover 4.1
- Final assembly adjusted to JIT
- Finished goods inventory dismounted
- Supply control for final assembly adjusted to kanban
- Kanban made operative within 3 days
- Supply readiness with a 98% guarantee
- 48 % of the stock value at project start – reduced
- Work in process reduced by 50%
- SAP with simple bar code interface integrated into kanban processes
- More than 75% of the annual production can be forecasted.