Restructuring at Hansa Metallwerke AG:
By Steffen Trautwein 1 and Armin Klüttgen2
Inventory pain not only means having to bear the pressure of high inventory costs, but also – due to incorrect inventory planning and the resulting stock shortages – shortages in terms of delivery readiness. With the support of Abels & Kemmner, Hansa Metallwerke AG, manufacturer of high-quality designer fittings and innovative shower and shower systems, has succeeded in achieving sustainable improvement effects through a finely tuned “combination” of measures and strategies in the areas of process design, planning procedures and IT system support.
As part of the restructuring of corporate processes at Hansa Metallwerke AG, the significant and, above all, sustainable reduction of inventories was one of the most important targets, as the existing excess inventories were causing immense suffering from a cost perspective. During the course of the project, it very quickly became clear that the goal of reducing the number of animals in the population can only be achieved if several approaches are pursued in parallel and the respective solutions are integrated efficiently. The introduction of a better planning system would only deliver suboptimal results in a process landscape that was not completely scrutinized as a zero base. Similarly, the conception of article-related planning and scheduling methods that are optimally adjusted each month by an automatic scheduling rule set makes no sense on the basis of an outdated ERP system that stretches its wings even for far simpler requirements. An intensive analysis of the current processes, the existing system support and the procedures used, supplemented by concentrated inventory driver workshops, uncovered the existing deficits and pointed the way to a new and holistic supply chain concept.
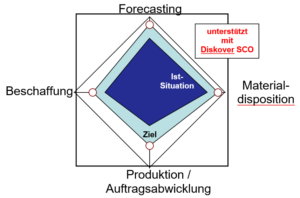
The project procedure model
An initial scan of the planning and scheduling processes showed that there was significant potential for optimization in the areas of demand forecasting, materials planning, procurement and production/order processing. The basis for the scan was intensive work with checklists from Abels & Kemmner, which can be modularly adapted to the respective company to be examined. The less than optimal state of development of the supply chain processes, measured against today’s best practice possibilities, was an initial indicator that significant logistical improvements could be expected through suitable measures in the areas of system support, planning and scheduling processes and the procedures used.
In addition, an initial overstock analysis for finished goods, merchandise and purchased parts was carried out as part of a potential study. Inventory reduction potentials of between 18 and 40 percent were identified, which were achieved in the first six months. The total inventory reduction potential was over 50 percent in some cases.
Designer fittings
In the first main project phase, the planning and scheduling processes for the various material types were recorded in detail, the existing IT support was examined and plant and warehouse structures were recorded in the existing system. At the same time, portfolio driver workshops were held with the various specialist departments. These workshops very quickly led to the first important answers to the following questions:
- Where are the process deficiencies?
- Where is the existing system support not sufficient?
- Where are methods used that produce qualitatively inadequate results?
- What are the causes of excess stock that cannot be tackled by planning and scheduling processes, methods and system support?
For example, it was found that procedures were used that are not recommended if the goal of reducing the portfolio is included in the target horizon. Examples of this are
- Purchasing tended – not wrong in principle – to optimize prices through quantity. New products are subject to a long design process, which is fine in principle. However, milestones for the handover to the production phase were not set, which often resulted in time-critical decision-making at the end with a fixed end date. One of the consequences of this was that the initial stock levels for new products were set too high because there was no time to carry out suitable analyses.
- The innovative spirit of the developers also led to frequent technical changes, but often without multiple use options, which unnecessarily increased the number of variants and led to high stock levels, particularly for the spare parts business.
- During the discontinuation process, residual quantities from framework agreements were found that were keeping inventories unnecessarily high due to a lack of communication of residual purchase obligations. Moreover, not all discontinued products were actively managed, so that in these areas it was not always possible to dispose of parts quickly (sale, discounting, scrapping). Due to the lack of active control, stock levels sometimes fell below minimum levels, resulting in new orders.
- The comparatively poor delivery reliability of suppliers was not actively addressed due to a lack of resources. Alternatively, it was easier to increase the safety stocks.
- Assortment constraints for accessories were generally endorsed and stocked ready for delivery as a finished assembly kit, but without examining alternative supply chain models at previous stages of the value chain in order to avoid expensive inventories including in-house value creation.
In the second main project phase, a concept for the sustainable reduction of finished goods and purchasing inventories was developed. In addition to article structuring according to ABC and XYZ codes, various sensitivity analyses were carried out in the form of simulations.
These analyses showed which logistical variables, such as target delivery readiness, replenishment times or batch sizes, influence the inventory situation and to what extent. Based on this, all parameters for optimizing the value streams were determined using dynamic simulation.
The detailed analysis of the existing IT support as well as the planning methods and processes revealed weaknesses in some areas that could be sustainably resolved by the concept to be implemented.
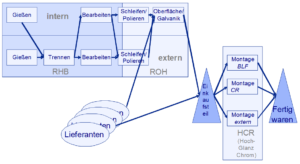
System support
A major problem was the existing ERP system BAAN in the 1999 release, which could no longer be updated due to extensive customization programming and in this version only provided rudimentary support for the requirements of efficient planning and scheduling. For example, stock levels of primary materials could be allocated to orders several times, as Baan continued to show reserved quantities as available. In addition, the retrograde booking led to late orders and thus to late replenishment. There was also insufficient transparency regarding stock levels and pull mechanisms to reduce stock levels could not be adequately implemented with the existing IT support. The implemented planning, scheduling and production control processes therefore only produced suboptimal results:
Planning and scheduling
The planning cycles were too long and there was a lack of clear demarcation between the planning levels. As a result, the planning information was not consistently structured throughout and there was no standardized planning model. Seasonal effects and the special issues relating to new arrivals and discontinued items were only taken into account to a limited extent. Although reorder points and safety stocks were used, these were determined without system support (ERP). When determining the safety stocks in particular, it was noticeable that they were calculated in different ways depending on the responsibility or resulted from empirical values. In some cases, the type of calculation did not do justice to the actual purpose of a safety stock, as it did not necessarily have anything to do with covering fluctuations in consumption behavior. In addition, the safety stocks and reorder points were determined completely independently of each other, whereby the safety stock is by definition part of the reorder point. In the disposition of purchased parts, order requirements were not checked on a demand basis, but once a week. As a result, we were “flying blind” for a week after the planning date and could no longer react to changes in the demand situation. The overall process at this point was highly manual, very time-consuming and therefore prone to errors despite the utmost care.
The production control process
In production control, it became apparent that there were no consistently clear business rules for structuring the control process, as the IT system did not function stringently either. Predefined rules (e.g. the processing of certain lists) were sometimes not adhered to, as the input for sequence planning was too complex: there were up to 5 different lists (sequence lists, priority lists), which were used more or less or not at all, depending on the responsibility. Summaries of quantities over too long an anticipatory horizon led to a strong stock-increasing effect. In some cases, the availability of primary materials from our own production and purchased parts was insufficient. This in turn led to planning uncertainties in final assembly. In addition, special requirements were not always scheduled as a separate order with an agreed delivery time, but as a regular warehouse order, which shortens the delivery time, but fills the warehouse with special items and uses up valuable production resources far too early.
Planning, processes and system today
The inadequate system support made it necessary to investigate the need for external forecasting and scheduling optimization. In future, Hansa Metallwerke AG will now be using the Diskover SCO software from SCT (Supply Chain Technologies). Diskover receives all planning-relevant data from the ERP system via a transfer table, which is then processed by Diskover using simulation to optimize the processes and parameters as well as for planning and scheduling through to the order proposal or production order proposal. The optimized procurement elements generated in this way are then returned to BAAN for operational implementation.
A standardized planning model and a clear delineation of planning levels and their responsibilities / tasks (sales, production planning / scheduling, production control) were established. Sales planning incl. The planning of new and discontinued products is also clearly regulated and supported by the system. The calculation of optimum reporting and safety stocks now takes place throughout the system and is no longer distributed among different people using different methods. Disposition takes place when there is a need for action, i.e. when replenishment is required. Manual planning activities are replaced by optimized automatic processes. Each item is automatically adjusted on a rolling monthly basis according to its consumption characteristics and its current life cycle position in terms of planning and scheduling. How this is to be done is stored in the software in the scheduling rules, which are maintained by the planner and automatically processed by the system. The stock and supply situation is transparent at all times and planning deviations are immediately displayed to the dispatcher via alerts and reports. The entire planning process is less time-consuming and significantly less prone to errors.
There are clear business rules on how to work in planning and scheduling / production control. The variety of sequence and priority lists has come to an end and the approach of achieving the desired readiness for delivery through optimum scheduling and quantity planning is being consistently pursued, thus eliminating the unrest caused by the heterogeneous use of different preliminary lists. Only in the event of competition for material and/or capacity will a priority list continue to be taken into account.
Unnecessary production advances no longer take place, as they build up superfluous stocks, consume input material for parts that are used several times and may be needed elsewhere, and use up production capacity at the bottleneck. The stocks are transparent, so that multiple allocations can no longer occur, as the available quantity is reduced when the planner schedules a production order.
Input material life cycle = L
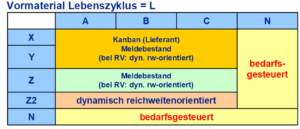
Conclusion
As part of this project, Hansa Metallwerke AG has consistently pursued and achieved the implementation of integrated planning. The company avoided tackling only individual symptoms and their causes, but was committed to implementing all the necessary changes required by the holistic concept in the interests of sustainability. The disease of inventory pain caused by unbalanced and uncoordinated supply chain processes, inadequate system support and the use of suboptimal procedures or manual processes is a thing of the past. A good supply chain performance in the form of the desired delivery readiness with minimal stock levels means that the inventory pain is quickly forgotten. The combination therapy worked successfully, according to the motto – operation successful, patient dead…al fit-! Hansa Metallwerke AG is thus well positioned not only to master the current economic crisis, but also to be able to act in line with requirements and, above all, without any complaints about its continued existence when the economy picks up again.
“About Hansa Metallwerke AG”
The long-established company Hansa – with its headquarters in Stuttgart – produces bathroom and kitchen fittings as well as shower and shower systems at its Burglengenfeld site. Sales are split roughly equally between domestic and foreign markets, with 50% each. The main customers abroad are Austria and the USA in particular. At 75%, a significant proportion of turnover is currently generated from the sale of single-lever mixers.
The production process consists of casting the fitting and is then continued in several operations such as cutting, machining, grinding, polishing and surface/galvanizing. The parts manufactured in this way are temporarily stored in chrome parts warehouses in order to be subsequently assembled with externally procured components such as seals and mixing valves (cartridges) in the assembly process to create the finished fitting.
Hansa Metallwerke AG offers a wide range of innovative fittings as well as shower and shower systems. These products enjoy a strong position in the international premium markets, not least because of their outstanding design. Furthermore, according to an annual survey of dealers and installers conducted by the magazine “markt intern”, Hansa has been voted the “No. 1 specialist trade partner” without interruption since 1982, which further underlines the continuity in service and quality.
In addition to functionality, Hansa’s motto is “Experience water”. Functional aspects are combined with the highest design standards. As a result, not only the fittings but also the element of water itself are now being designed. This is achieved using specially developed aerators, open watercourses and the colorful visualization and staging of the water. The colors can be accentuated and highlighted even more with the choice of chrome, gold or platinum fittings.
1 Steffen Trautwein is Head of Supply Chain Management at Hansa Metallwerke AG in Stuttgart.
2 Armin Klüttgen is a Senior Consultant at Abels & Kemmner GmbH.