Optimized material flow with a high number of variants
By Mathias Seidler and Dr. Bernd Reineke1
In recent years, the bicycle manufacturer Derby Cycle has managed to escape price-volume competition by repositioning itself in the direction of mass customization. For production and logistics, this meant an increasing number of variants and more flexible processes. In order to meet these requirements while also increasing sales in the paint shop and decor area, Derby Cycle commissioned the management consultancy Abels & Kemmner to accompany and coach the optimization process.
Derby Cycle is the largest bicycle manufacturer in Germany. The entire brand portfolio comprises the main brands Focus, Univega, Kalkhoff, Raleigh and Rixe. The company designs and produces trekking, city, off-road and children’s bikes for everyday and touring use as well as the complete range of sporty mountain bikes and racing bikes for demanding leisure cyclists or for use in competitions. The range is aimed at all age groups and offers numerous variants for every purpose.
To optimize the processes, the following work packages were agreed with the management in the first step:
- Situation analysis with value stream mapping and constraint analysis
- Identification and conception of solutions
- Economic feasibility study and decision for a solution scenario
The logistics and production processes were recorded together with the project team, which was made up of production employees from the areas under investigation.
It became clear that the individual design of the bicycle frames with customizable paintwork and decorations places considerable demands on the processes. The material flow is synchronized from the straightening process to pre-assembly by using an overhead chain conveyor system. However, the material flow must be interrupted at certain points in order to introduce individual design elements, such as masking frame parts to retain the natural aluminum color. This creates gaps in the conveyor chain, which are then filled with other frames that have already undergone intermediate processing in order to make optimum use of the paint shop’s capacity. A high handling effort, as the decor example shows:
Decor refers to the design of bicycle frames with the help of decorative films, some of which are customized and applied directly to the frame. Whereas in the past these were applied after the final painting stage, the decor is now applied before the final clearcoat protective layer in order to protect the decor in the long term (undercoat decor). This leads to the painting process being interrupted again. The frames are removed from the conveyor chain and temporarily stored on special racks. To attach the decor, the frames are then removed from the intermediate storage racks and placed on placement devices. In two layers, the employees in the decor area glue the decors manually onto the areas specified by product management: a process that can hardly be automated due to the numerous gluing variants. After gluing, the frames are stored again before they are finally clear-coated.
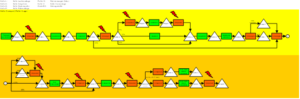
Identified bottlenecks (constraints)
The capacity of the painting line is not the main bottleneck in the process, but before the painting line is fully utilized, the decorating area, which already operates in two shifts during the peak season. Due to the increasing proportion of undercoat decors, there are increasing bottlenecks in the decor area in terms of intermediate storage space, handling costs and personnel capacities for gluing. In order to supply the second layer with painted frames for gluing, a storage area is required which, assuming the growth rates, can no longer be provided. Furthermore, the handling effort for removing and repositioning the frames is considerable.
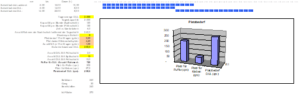
The calculated space requirement for buffers, gluing and DUL (decor under lacquer) shows the potential space gain when changing the processes.
Using analysis tools to find solutions
A specially adapted analysis tool was used to illustrate the relationships between the daily number of undercoat decorative frames, the storage space requirement and the gluing space and personnel requirements, which made it possible to calculate various quantity and capacity scenarios. In particular, the mapping and variation of the layer model led to interesting results. For example, it was found that the space required for intermediate storage to supply the second shift with frames to be glued increased significantly as the number of pieces grew. However, when the shift model was reduced to one shift, the space required for temporary storage decreased, but at the same time the space required by the decorating staff to handle the quantities increased. As a result, the solution of a single-shift operation showed considerable advantages over a multi-shift operation.
It was also shown that the process can be accelerated and the overall effort reduced if the frames are no longer placed on the intermediate storage racks after painting, but directly on the devices for applying the decor. This eliminates the need for handling for relocation. Although these measures increased the space required in the decor area, the storage space freed up in the pre-assembly area could be used for activities after painting, which in turn had advantages for the material flow towards pre-assembly.
Measures and economic efficiency
A number of organizational and structural measures were necessary to implement the new concept:
- Changing the transport routes of the chain conveyor system
- Relocation of the small parts attachment and undercoat decorative label application area to the pre-assembly area
- Procurement of additional devices for attaching the undercoat decorations
- Re-organization of the provision of label material
To approve the concept and the necessary measures, an evaluation of the solution was presented to the management by means of an ROI (return on investment) calculation. This showed a clear economic advantage of the proposed solution, as the handling effort was significantly reduced. Following a positive review, the necessary measures were immediately initiated and implemented.
1 Mathias Seidler is Managing Director of Derby Cycle Werke GmbH; Dr. Bernd Reineke is Managing Partner of A&K