Efficient procurement processes are automated
by Dr. Bernd Reineke
Optimizing procurement processes to improve liquidity by reducing inventories and increasing delivery readiness generally leads to smaller batches and shorter replenishment cycles. Software tools such as DISKOVER automate these procurement processes to optimize liquidity and customer satisfaction, helping dispatchers to work more efficiently than before despite the increasing number of processes.
Suppliers of instant and stock programs are particularly familiar with the problem: in order to be able to deliver at all times, the warehouse is filled to the brim, and yet the items that the customer needs so urgently are missing. The company’s profitability suffers as a result: low cash flow due to tied-up capital, resulting in low financial flexibility, high capital costs and increased logistics costs. There are often additional complicating factors that result not least from industry-specific circumstances: e.g. high variant diversity, seasonal sales behavior or fluctuations in the yield of process manufacturers.
In numerous projects, Abels & Kemmner has worked out concepts and developed methods and procedures to achieve better operating results despite difficult boundary conditions. Our focus on supply chain management often results in inventory reduction and savings potential, which leads to a significant increase in liquidity and cost reductions, so that these projects pay off within a short period of time.
But the best results count for nothing if the concepts cannot be implemented. And the work starts with the implementation: the new processes have to be trained, understood and internalized. Areas of responsibility may change or be redistributed. The volume of work can also change drastically: if, for example, inventories have to be reduced, this is often accompanied by shorter order and production cycles as well as smaller batch sizes or order quantities. It is obvious that the number of production and order items is increasing, and with it the effort required to create and process these items. To ensure that the savings potential calculated when reducing the portfolio is not eaten up by the increased administrative costs, measures to reduce costs must be developed. Automation is the key word. What is already common practice in production and logistics is now increasingly finding its way into upstream administrative tasks.
The possibilities for automation here depend primarily on the IT systems used. As these are generally standard systems, you very quickly reach the limits of what is feasible. Implementation without additional adaptations or additions is then hardly possible. The adaptation of IT systems is associated with correspondingly high costs and is often not even feasible.
In such cases, the use of established software tools such as DISKOVER is recommended for the automation of scheduling and procurement processes.
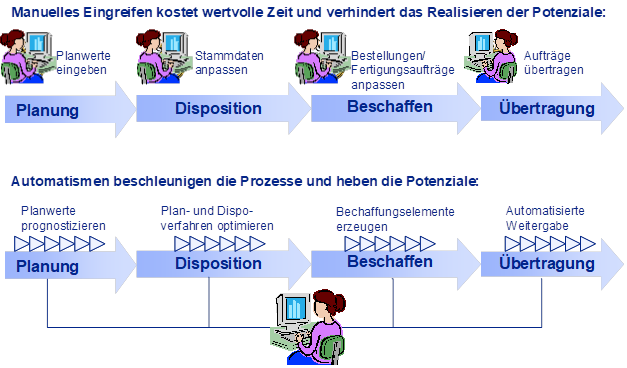
Many companies are therefore pursuing a strategy of filling identified gaps in the IT environment with special solutions. In the area of inventory management, the DISKOVER optimization tool was able to compensate for deficits in many projects and even improve them. DISKOVER offers all the prerequisites for optimizing processes from planning and scheduling to order proposals. In particular, the possibilities for automatic optimization of procurement parameters speak for DISKOVER as a supplement to standard ERP systems. For example, DISKOVER independently adjusts logistical parameters depending on the consumption behaviour of an article, determines the optimum forecasting procedures and optimizes the process parameters within the permissible framework.
The integration of DISKOVER into the company’s IT structures is relatively simple and requires little effort. While the existing IT systems and DISKOVER remain standard, existing transfer programs that can be adapted with little effort are used to link the systems. Depending on requirements, additional logic can be set or added in these interface programs to further optimize processes.
For example, delivery dates of the order proposals can be adjusted to the delivery days of the suppliers. Order quantities can be optimized by taking price scales into account. Or requirements at assembly or product level can be broken down to components using the BOM explosion. The aim is always to reduce the workload of the planners and purchasers and to adopt the results without any further changes. This provides the basis for automating the processes.
Of course, monitoring automated processes is essential. Regulations and indicators must therefore be developed to prevent processes from getting out of hand. If certain threshold values are exceeded or events are triggered, a message is sent directly to the screen of the person responsible, who can then deal with the problem. If, for example, an order exceeds a permissible range, the person responsible must decide what is to be ordered.
This allows those responsible to concentrate on such exception reports while standard business is processed without interruption.