Dr. Bernd Reineke’ and Steffen Schwippl2
Abels & Kemmner GmbH’, Herzogenrath, and Serag-Wiessner KG2, Naila
The following article describes the implementation of an optimization project in the area of scheduling management. The aim of this project is to sustainably reduce stock levels and costs while maintaining delivery readiness of 24 to 48 hours. The target parameters readiness for delivery, stocks, set-up costs and stock turnover are determined by means of simulations, which are carried out using new software as a supplement to the existing ERP system. With the help of the inventory controlling system introduced in the project, Serag-Wiessner KG, a medium-sized manufacturer of medical and pharmaceutical products, was able to continuously maintain a delivery readiness of 96% within two years, while at the same time reducing stock levels by 35%.
l. Introduction
In the pharmaceutical and medical sectors in particular, customers depend on fast delivery of products of the highest quality. Suture material of various resorption levels, textile implants or irrigation and infusion solutions often have to be on site within 24 hours. For the manufacturers of such products, this is associated with increased stock levels, as they must remain able to deliver even in the event of fluctuations in demand and disruptions in the supply chain. In order to produce cost-efficiently without jeopardizing delivery readiness, you need a scheduling management system that is optimally tailored to the company. In the case of Serag-Wiessner KG, a medium-sized manufacturer of medical products, this means optimally managing a range of around 3,000 items in the surgical sutures and textile implants division, which are characterized by different thread types, thread thicknesses, lengths and needle-thread combinations. Around 1,500 items have to be stocked from the dispatch warehouse to ensure that the approximately 25,000 customers, which include hospitals, doctors in private practice and wholesalers in Germany and abroad, receive their deliveries within 24 to 48 hours. To meet these requirements, stocks are held in the finished goods warehouse, which were dimensioned before the start of the project on the basis of the ERP order proposals from planners and dispatchers. These stocks are therefore the focus of the optimization project, as there is an enormous savings potential of up to 35 % for many companies (Fig. l) [1].
In the past, attempts to significantly reduce stocks by our own efforts did not lead to the desired success. For this reason, the medium-sized company initiated a project to optimize its scheduling management and relied on the experience of Abels & Kemmner Gesellschaft für Unternehmensberatung, which had previously helped other pharmaceutical companies to optimize their supply chain [2]. The management consultancy had already evaluated company data analytically and simulatively in many consulting projects and thus contributed to the optimization of company processes. In particular, scientifically sound methods and procedures were used. The requirement to generate a consistent solution raised the question from the outset as to whether and how the existing ERP system could support this solution. The restrictions in production and logistics had to be taken into account and included in the determination of the scheduling and planning parameters: In addition to the sales-oriented target figures – delivery times of 24 to 48 hours and an average target delivery readiness of 96% – the planning parameters also had to ensure that the production orders and the associated set-up processes were limited to 1,200 per month.
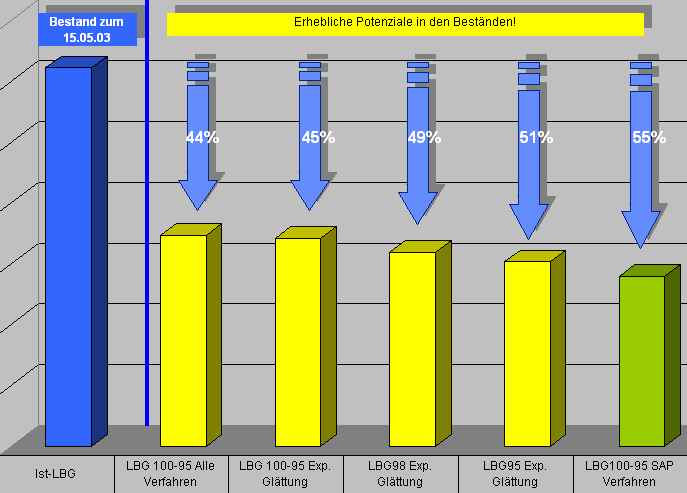
2. determination of the target parameters and their values
The project begins with an inventory of the current processes and logistics parameters such as range, delivery readiness and stock turnover. An important aspect in this phase is also the analysis of the ERP system used by the manufacturer of medical devices. Although the current system has basic scheduling and forecasting functions, it became clear right at the start of the project that the project objectives could hardly be achieved without extending this system, as the system could not be adapted sufficiently to the actual planning requirements [3]. The management therefore decides to supplement the missing application options with the DISKOVER SCO optimization tool. This software is characterized in particular by strong functionalities in the following areas:
- Optimization through simulation,
- Numerous forecasting and safety procedures (especially distribution-free procedures),
- Optimization of scheduling parameters and
- integrated inventory controlling.
As the decision to use this software is made in the early project phase, the system’s possibilities are already incorporated into the design, which means that the project team has much greater scope for design.
To find a solution, differentiated simulations are first used to determine the influences of delivery readiness, stocks and set-up costs. The following factors are of particular interest here:
- Lot sizes,
- Minimum quantities,
- Maximum stocks,
- Covering periods and
- Disposition procedure.
The medium-sized company therefore uses a total of 26 different simulation scenarios with different settings for the aforementioned parameters depending on their ABC/XYZ classification to achieve the target delivery readiness with the lowest possible inventories.
It quickly becomes clear that the project objectives can only be achieved with differentiated approaches. This means, for example, that different target delivery readiness levels are defined for different product groups or that higher ranges or larger batch sizes are selected for low-value C-items than for high-turnover A-items. Ultimately, a set of rules in the form of a decision table is created as part of the concept, which takes into account the criteria of the ABC and XYZ labels as well as the shelf life and market requirements of the various product groups. This set of rules is mapped in the DISKOVER SCO software and can be flexibly adapted to changing requirements, whether these changes are caused by new market demands, new products or changes in warehouse capacity or capital commitment.
As part of the simulations, the achievable target values for delivery readiness, stock and set-up costs can be determined in advance. However, the results are not yet apparent at the beginning of the implementation phase. The breakthrough to sustainable inventory reduction only comes after the implementation of daily inventory controlling. Inventories, sales, stock turnover and readiness for delivery are reported after each day and compared with the currently simulated target figures. In the case of delivery readiness, a distinction is even made between different time periods (seven days and 30 days) in order to better assess the short-term development of delivery capability. This report is sent by e-mail to the screens of dispatchers and management on a daily basis. This allows those responsible to react quickly in the event of major deviations and take countermeasures if necessary. The aim of this measure is to reduce stocks as far as possible so that the 24 to 48-hour delivery capability is still maintained.
3. use of inventory controlling to reduce inventory levels
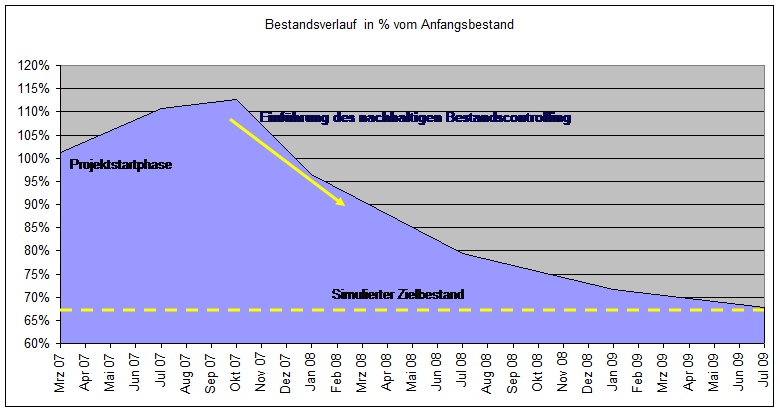
The inventory development (Fig. 2) shows that DISKOVER inventory controlling improves the results sustainably. Excess stocks will be reduced and the total stock will be cut to around 65%. This also leads to an increase in stock turnover, which rises from six to nine. This reduces the average storage period from nine to six weeks (Fig. 3).
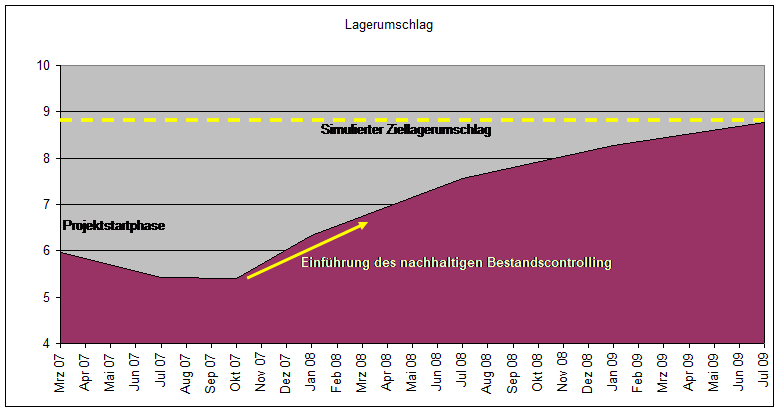
As delivery readiness must not be compromised under any circumstances, this is also closely monitored. In the course of inventory controlling and scheduling optimization, this critical parameter even improves from an average of 93% to 96%. Reducing stocks and shortening inventory turnover therefore does not have a negative impact on delivery readiness.
4. results and conclusion
As part of the scheduling parameter optimization project, the following goals were achieved in the long term:
- Stock turnover increased from six to just under nine. This resulted in an average storage period of around six weeks.
- Stock levels were also reduced to 65%, but this was not at the expense of delivery readiness. On the contrary, delivery readiness was improved by three percentage points to 96% and has been continuously maintained.
- The 35% reduction in inventories released corresponding liquidity reserves, which the company is now actively using to further strengthen its competitiveness.
Overall, all measures were successfully realized and implemented. The sustainable implementation of inventory controlling in particular leads to a permanent reduction in warehouse and inventory costs for the manufacturer of medical products, which in most companies is around 15% per year [3].
Medium-sized companies in particular, including those in the pharmaceutical industry, can reduce or save costs in the short and long term with adapted and comprehensive inventory optimization. It is important to ensure that a precise analysis of the existing data is carried out and that delivery readiness is not jeopardized. Simulations adapted to the company and the market support the optimization process by showing which stock quantities would have a reducing effect on the readiness to deliver and thus critical values for the disposition parameters of the respective article groups can be precisely defined.
Based on these scientific and mathematical principles, a low-risk, demand-oriented adjustment of the disposition and thus a successful inventory optimization while maintaining or improving the ability to deliver is possible.
Literature:
[1] Kemmner, G.-A. Up to 30% stock reduction potential; in: VDI-Nachrichten No. 20, 19.05.2006.
[2] Kemmner, G.-A. The external eye sees more; in: CHEManager No. 15- 16/2009, p. 23.
[3] Reineke, B. Effiziente Beschaffungsprozesse laufen automatisiert; in: Logistik & Fördertechnik No. 2, 15.02.2006, p. 42f.