By Götz-Andreas Kemmner
In the last issue of POTENTIALE, we explained in part 2 of the best practice article what a KPI means, what objective it measures, how it is precisely defined and from which input data it is calculated, as well as why it is so important to link KPI and originator. A KPI data sheet should be created for each KPI in order to record all the variables, parameters and definitions that make up the KPI. The data sheet is also helpful for the new colleague in the event of vacation replacements and staff changes!
In general, people are a key factor in defining and establishing a key figure, because:
Basic principle 7: If a goal (value) is unattainable, it motivates dreamers at best.
Fruit that hangs too high often tastes sour. The same applies to key figures with unattainable, because unrealistic, target values. Target values can be unrealistic because arbitrary targets have been set based on theoretical considerations. This is rarely the case in practice, because most of us are clever enough to at least base our target values on the current actual values if we don’t know any realistic target values.
It happens more regularly that the relationships between key figures are not taken into account. As the production curve methodology shows us, throughput times, work in progress, adherence to delivery dates and capacity utilization are not independent key figures. Accordingly, the individual target values cannot be specified independently of each other. Corresponding correlations also exist between inventories and delivery readiness. Such frequently statistical correlations are often overlooked in practice or are not even known.
To a certain extent, target values are of course also unrealistic if the key figures under consideration are not complete (best practice module 4). In order to achieve realistic target values, it is not enough to simply set the target values close to the actual values.
Setting a realistic, achievable combination of target values in the company is a major challenge. To do this, you must have suitable mechanisms in place to determine the key figure correlations. Tools that can support you in this are ERP simulation systems and, in some cases, production characteristic curves.
Our best practice module 7 distinguishes the top performers from the rest of the logistics controlling community:
Efficient logistics controlling ensures that realistic limit and target values are specified for the individual KPIs, which take into account the direct or statistical correlations between KPI values.
Basic principle 8: If you are to work with key figures, you must also be able to rely on the data quality
Much of the basic data for our logistics KPIs comes from our ERP systems:
- classic master data (batch size, replenishment lead time, unit weight, …),
- Transaction data (historical consumption, inventory posting records, …),
- Forecasting methods and parameters,
- Planning procedures and parameters,
- Scheduling and production control procedures and parameters.
Unfortunately, we regularly find that the data quality in ERP systems is abysmal. A study by the Research Institute for Rationalization at RWTH Aachen University in 2012 found that in 90% of all companies, more than 10% of master data is incorrect! (UdZ 2/2012, p. 42).
Incorrect master data is not just quantitative data such as batch sizes, replenishment times or minimum order quantities. Qualitative data also has a high potential for error. Such incorrect master data not only has an impact on key logistics figures, it also leads to economic losses. Incorrect forecasting or scheduling procedures and incorrect associated parameters can cause significantly more economic damage than a single incorrect quantitative master data.
You will never be able to keep your master data completely error-free with economically justifiable effort. With the help of so-called scheduling rules, however, the effort required to maintain a whole range of master data can be ensured with little effort. The term disposition actually falls short. All forecasting, planning and control procedure and parameter settings, as well as a lot of quantitative master data, can be regularly adapted to the current properties of the individual articles and material numbers via MRP rule sets.
The profitability of its own value chain is even more important for a company than reliable basic data for its logistics KPIs, which is why best practice module 8:
Best practice companies ensure that the quality of master and transaction data in the ERP system is kept as high as possible in an efficient manner, not only in the interest of reliable logistics key figures, but above all to protect their own company from economic damage.
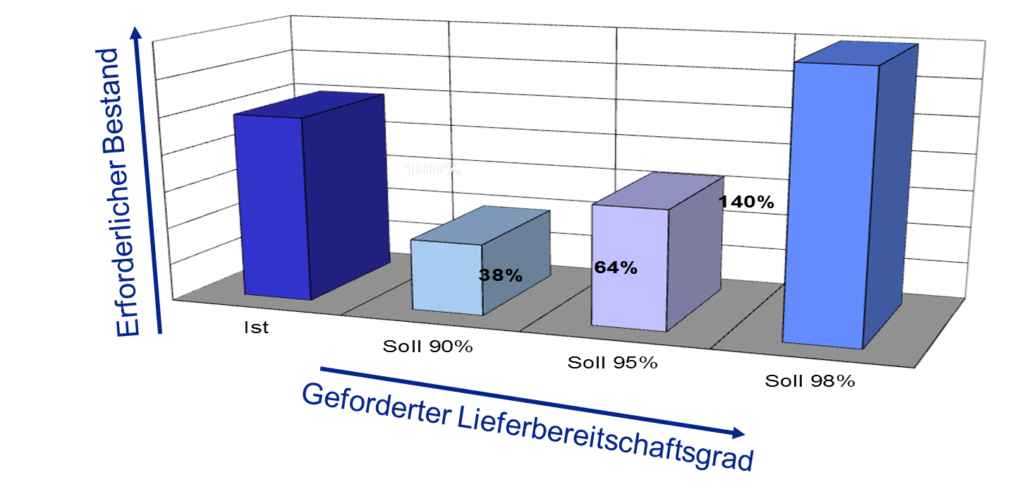
Basic principle 9: If you want to use logistics controlling to identify and continuously develop potential for improvement, you need to be able to dig through data flexibly.
Now that we have come such a long way together, all we need is for someone to let us access the data that we want to analyze and prepare for key figures.
This sounds plausible; unfortunately, practice sometimes looks different. In the age of Facebook and data protection, some people post the last intimacies and banalities online, while others (the companies) want to keep as much data as possible under lock and key for reasons of data protection, data security and compliance.
The access authorization of employees to data in the ERP system has been increasingly restricted in many companies in recent years. Sometimes you get the impression that data security is so important to some companies that they prefer to keep their own employees stupid. Efficient logistics controlling is not possible in this way.
In order for logistics controlling to fulfill its task of uncovering weak points and initiating and fuelling a continuous improvement process, it is not enough to access certain predefined logistics KPIs. In logistics controlling practice, it is much more necessary to be able to run specific data evaluations ad hoc and without major approval processes. You may be able to manage a company with seven key figures in the long term, but they are definitely not the same seven key figures all the time.
Which brings us to best practice building block 9:
Efficient logistics controlling enables employees to carry out ad hoc data analyses.
Basic principle 10: Anyone who is to work in a qualified manner must be qualified.
Permission and ability are sometimes two different things. The fact that users are allowed to carry out spontaneous data analysis does not necessarily mean that they can do so. The data in the ERP system databases is stored in a normalized format to avoid data inconsistencies and save storage space. From the user’s point of view, this means, for example,
- that information that logically belongs together, such as all the information on an order or a production order, is distributed across several database tables;
- that information belonging to different logical steps is sometimes stored in the same tables.
Working with such basic ERP data is not always easy, which is why the data is sometimes summarized in so-called data warehouses and stored in a more user-friendly way. But you also have to be able to operate such a data warehouse.
As we all know, the problem and the consequences of inadequate qualification are already apparent when using our ERP systems. Which company really trains its users sufficiently in the use of the ERP system?
Corresponding qualification potential also exists in logistics controlling. On the one hand, they are due to inadequate ERP training, but also concern the application of the entire controlling square and the creation of key figures.
The bon mot “If you think education is expensive, try ignorance”, attributed to Derek Bok, former president of Harvard University for many years, also applies to logistics controlling.
Education, training, documentation and regular refresher courses are essential foundations of efficient logistics controlling and far more cost-effective than systematically dabbling with key figures, which is why our final best practice module is 10:
Efficient logistics controlling qualifies its users and does not rely on ignorance.
The further we delve into the details, the longer the list of best-practice building blocks for logistics controlling would grow. However, if you construct your logistics controlling system from the 10 building blocks described above, you will have created the essential infrastructure for efficient logistics controlling. Good luck with that!
Further information on this topic can be found here: