From David Nyeste
In logistics, the degree of delivery readiness is one of the key factors in establishing and maintaining strategic competitiveness in a market.
In retrospect, the historical availability of an item may have been 100%; in other words, the item was available in full, on time, in the right quantity and in the right quality during the period under review. When planning future availability, however, no one can guarantee a value of 100%, even if one tries to come as close as possible to 100% availability for the so-called never out of stock articles. In practice, however, any availability of less than 100% can make sense and be required. Interestingly, the cause-and-effect principle is often reversed when deciding on the strategically required readiness to deliver: The readiness to deliver individual items often depends on the associated costs, i.e. primarily on the level of one cost factor: the safety stock.
For this reason, the topic of “delivery readiness and safety stock” regularly results in “keen interest” or “personal involvement” on the part of planners and dispatchers. This is perfectly understandable and even desirable from a business perspective. What is less desirable, however, are incomprehensible or simply arbitrary methods for determining the level of safety stocks, which are often based on personal experience, discretion or, to put it another way, pure gut feeling.
For this reason, the question of the sense and nonsense – including the differentiation criteria – of security stocks is legitimate. Here is a brief overview of the cause and effect of safety stocks. The main factors influencing the safety stock are
- the quality of information about future requirements
- the replacement time of an article
- the targeted delivery readiness.
Quality of information about future requirements
Ideally, it is known in good time which article is needed when and in what quantity. In practice, however, this is the exception rather than the rule. Items whose requirements are known in good time can be provided on a make-to-order basis without any safety stock. In most cases, however, the available information is not sufficient for such a strategy, so that stock buffers are necessary to compensate for this lack of information. A decisive improvement in the information situation, e.g. through reliable information from sales about future requirements, through increased customer integration in the form of reliable or even binding requirements planning, always has a real (inventory) effect.
Statistical forecasts based on historical consumption are another means of determining demand when there is a lack of information. These have two advantages: firstly, results can be reproduced exactly, and secondly, the quality and thus the suitability of different combinations of methods and parameters can be compared with each other. The bad news straight away: there is no guarantee that even the best forecasting method will reliably predict future requirements with a sufficient accuracy rate. However, indicators can be used to make quality statements about the respective risks and thus systematically derive conclusions about the level of necessary safety stocks.

The methods used in practically all ERP systems to calculate forecasts and safety stock levels are based on the assumption of normally distributed demand. This means that the frequencies of demand quantities within an observation period are distributed around the mean value according to a Gaussian bell curve.
In practice, however, items with normally distributed demand tend to be the exception. There are two ways to calculate reliable forecast values and safety stocks: One should use distribution-free forecast and safety stock methods and test the usefulness of the methods by simulating the entire forecasting and planning process over a historical period of typically 12 months.
The replacement time
Flexibility and responsiveness to customer requirements are valued quality features in many industries that are difficult to compensate for. From a company’s perspective, this statement applies to both supplier and customer-facing processes. Long replenishment times for individual products and components reduce the ability to react spontaneously and therefore often have two significant effects on inventory planning: On the one hand, with long replenishment times, the necessary flexibility has to be ‘bought’ with inventories. On the other hand, exception handling in the context of planning changes ties up additional important resources that are often subsequently lacking elsewhere.
The replenishment time for finished products and components is a special case: Here, planning should not only take into account the pure material-specific replenishment time, but also the respective delivery time agreed with the customer. Despite long replenishment times, planning can be relatively relaxed if customers tolerate a sufficiently long delivery time. In figures, this means less (security) inventory.
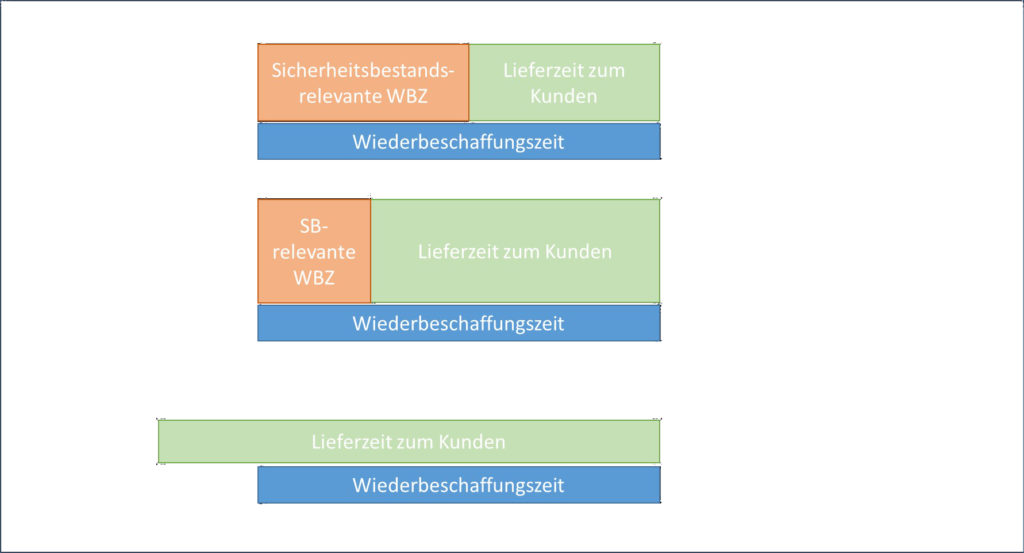
Required availability
Last but not least, the required availability as a strategic requirement is a key factor influencing the safety stock and the one adjusting screw with which safety stocks can be directly influenced. At this point, it should be noted once again that perfect availability of 100% can be achieved and is often actually achieved due to other framework conditions (e.g. batch sizes). However, a residual risk of unavailability cannot be ruled out from the outset in planning. Mathematically speaking, the statistical availability function is said to approach the value 1 (see graph). The ratio of required availability and costs increases disproportionately due to a statistical multiplier for the safety stock.
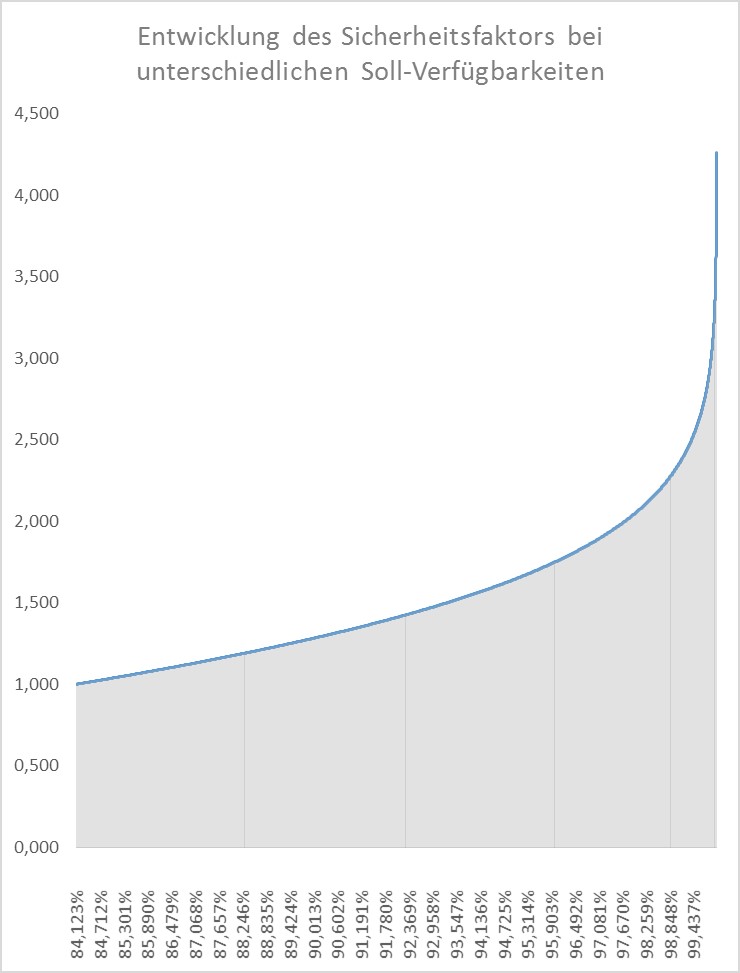
However, planning with statistical tools does not quite complete the puzzle. In practice, in addition to reliable and comprehensible safety stock planning, other factors such as organizational flexibility, responsiveness and communication skills also play an important role in ensuring the last bit of material availability. In addition to routine planning, these factors also help to improve availability. However, as these means and methods generally incur the highest costs, they should be used ‘on top’ to conserve resources as much as possible, i.e. ideally for exception handling only.
Betting on the lottery win
You can compare the safety stock with an insurance policy. Anyone who takes out insurance generally does so to protect themselves against a risk. The insured person undertakes to pay an insurance premium on a regular basis, in return for which the insurer undertakes to settle the claim in the event of an insured event. In principle, these are two opposite bets: The insured person bets on the occurrence of the insured event and pays a stake, the insurer bets against it and collects the stake. The stake is based on the one hand on the statistical probability of occurrence and on the other hand on the amount of loss of the insured event.
What sounds simple in principle is often completely disregarded in practice when dimensioning safety stocks. It may be that a warehouse fire at the supplier’s premises results in high costs for availability. But how (un)likely is it that this will actually happen? What is the likelihood that alternative suppliers and procurement channels will be able to compensate for the loss? How likely is it that the safety stocks will not cover a one-off delivery failure? What costs are incurred by the customer if an appointment is postponed? Are customers really so intolerant of unavailability caused by suppliers that their own safety stocks have to cover such a case? And if so, which contingencies should be covered by safety stocks? Such constructs can be continued indefinitely up to betting on winning the lottery, with the difference that no entrepreneur is likely to declare that betting on winning the lottery is a strategic business model.
Safety stock with a purpose
In addition to a balanced portfolio of measures to maintain availability, it is therefore crucial in inventory management to differentiate between useful and useless safety stocks. Every euro of stock value must be legitimized by the highest possible contribution to achieving the target for the required availability. There is a point at which every additional cent in safety stock does not lead to a correspondingly high or even a negative benefit, so that the costs are no longer justified. The latter can be the case, for example, if there is an upper limit for the required availability in addition to a lower limit.
Seen in this light, the safety stock is a blessing and a curse in one, which the logistics specialist has to deal with. In principle, he should therefore treat it like a democratically elected government: before making a decision, he should thoroughly examine the possible consequences, make a plausible and comprehensible decision, not set expectations at 100% of what was promised and, very importantly, review his own decision at regular intervals, reconsider it if necessary and, if necessary, make a new decision.