Smooth production with a market-synchronized value stream
by Stefan Bünger, Manfred Bürger1, Andreas Gillessen, Dr. Andreas Kemmner
Increasing market fluctuations and variant diversity as well as shorter delivery times with delivery dates that cannot be postponed caused a lot of extra work and unrest in production and final assembly at Fritz Driescher GmbH & Co. The new logistics business model was implemented in the form of a market-synchronized value chain from component production to final assembly, in which production was greatly streamlined. To achieve this, capacity bottlenecks had to be resolved, throughput increased and lead times shortened.
Fritz Driescher GmbH & Co. KG in Wegberg is a medium-sized company specializing in the development and construction of switchgear and switching devices for the energy supply industry. The product range includes medium-voltage switchgear, medium-voltage switches, transformer stations, low-voltage switchgear and high- and low-voltage fuse-links. Production is characterized by a very high level of vertical integration, with order-related component production supplying the components required for customer-specific final assembly – with extremely short delivery times and high adherence to delivery dates. However, this essentially highly customer-oriented, order-based production – based on the Industry 4.0 principle with batch size 1 on demand – became increasingly critical. Delivery deadlines could only be met with great commitment from everyone involved.
Bottleneck pure contract manufacturing
Due to market fluctuations, the increase in the number of variants and shorter delivery times, this order-oriented production was now reaching its limits. Due to the complexity of the products and the variety of parts, the constant need for coordination between component production, central warehouse, final assembly and order center became an almost impossible task. As a result, components were constantly missing in final assembly, which led to stockpiles of parts that were not needed. On the other hand, this also resulted in stocks of systems that could not be fully assembled because parts were missing. Component production – especially machining – also struggled with high order backlogs and long throughput times. Thanks to the great flexibility of the working time accounts in component production and the relatively high proportion of standard parts manufactured, it was still possible to meet the delivery deadlines. However, this comes with increasingly high costs and growing inventories. It was therefore time to develop a new logistics business model that would continue to flow very synchronously with the market but would bring significantly more calm to production and also reduce stock levels.
80/20 leveling performed
A portfolio analysis of the individual parts made it clear that the majority of production capacity utilization (approx. 69%) is accounted for by only around ten percent of the parts that are required on a fairly regular basis. Such products are well suited for so-called pull control according to the supermarket principle. The remaining approx. 90 percent of the parts to be manufactured occupied the remaining third of the production capacity. As the results of the analyses showed, the existing capacities in the various production areas were sufficient over time to produce both the ten percent of items to be stockpiled (so-called XY items) and the 90 percent of items to be produced to order (so-called Z items) on time. A separation of the material flows between XY and Z articles or line production on different material numbers was not necessary or sensible. The core element of the new logistics business model was therefore a so-called 80/20 leveling in production.
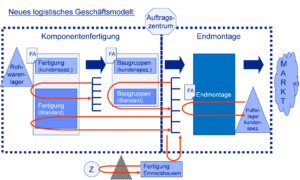
Full production hopper emptied
However, a throughput time analysis in component production showed that despite a balanced inflow and outflow of production order hours, there were excessively long order queues in front of the various capacity units in production, which were the main reason for the long throughput times. The work backlog averaged 21 working days and led to major problems in meeting deadlines in component production.
In order to correctly position component production logistically and focus on short throughput times with high adherence to delivery dates, the work in progress in component production had to be reduced:
– The production work in progress was reduced to the new required target level by temporarily increasing production capacity through additional and ghost shifts and the outsourcing of orders.
– A personnel capacity management system was developed and installed, which shows the short-term personnel capacity requirements for the various areas of component production. In addition, production orders may only be dispatched on time and not prematurely or backdated.
Over the course of six months, these measures made it possible to significantly reduce production order throughput times. However, this required more than just these purely production-oriented measures.
Planning and control in the scheduling department also had to be aligned with the principles of the new logistics business model.
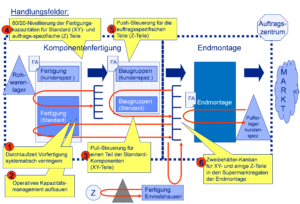
80 percent manufactured in the Kanban warehouse
Whereas previously all items were manufactured to order and only stored in batches, today XY items are stored in the central warehouse or on the supermarket shelves in final assembly. These warehouses are managed using Kanban-based pull control. This means that all items to be produced for specific orders can be prioritized with short throughput times and fast availability. This push production is triggered via a production order in the ERP system (Baan 5).
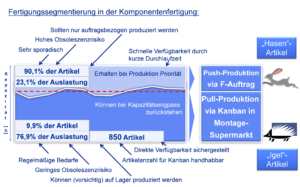
In order to efficiently implement push and pull control for component production and the Kanban system, the planners and schedulers now regularly adjust the planning, control and scheduling settings in the ERP system on an item-specific basis. The “operating point” is always readjusted so that the value chain functions at minimum cost. In order to achieve this, it was necessary to develop a set of rules for optimizing the system settings (technical jargon: dispo parameter optimization). The parameter settings for the individual article classes (ABC/XYZ/ELAN/etc.) such as push/pull control, degree of readiness for delivery, safety stock, ordering method, etc. were defined in the rules and regulations. The entire range of articles managed by the order center is now structured as follows
– components with reasonably even requirements and
– Components with a low degree of repetition, sporadic demand behavior or customer-specific parts.
Optimum disposition parameters simulated
While the first group of parts is managed via Kanban organization, the second group continues to be managed conventionally in order to avoid unnecessary stocks while still meeting delivery deadlines and further reducing delivery times. However, applying the rules to all articles and determining the parameter settings to be changed can no longer be done manually in the ERP system. The effort required for this would be far too great. Due to the variety of system settings to be changed, this is now carried out with the help of the DISKOVER SCO simulation software from SCT. This tool has already been used to analyze the current situation and simulate various scenarios of the new logistics business model and can also be used by users as a front end for daily scheduling.
The effects of these measures
By implementing the new logistics business model, DRIESCHER-WEGBERG has managed to significantly reduce throughput times and increase flexibility. As a result, it was possible to reduce inventories and even improve delivery readiness. Despite shorter throughput times, production is now running extremely smoothly. Overall, DRIESCHER.WEGBERG was able to significantly strengthen its competitive position in the market. This result impressively underlines the importance that an optimized supply chain can have on a company’s success.
1 Stefan Bünger is an authorized signatory and Manfred Bürger is head of the order center at Fritz Driescher GmbH & Co. KG, Wegberg