Scheduling parameter optimization is a methodology discussed and applied in many companies today. However, consistent maintenance of the scheduling parameters is only useful if the daily scheduling largely adheres to them. With the help of target stock management, the application of an MRP system can be effectively monitored on an ongoing basis and the focus remains on the goal of high delivery capability with the lowest possible stock levels.
Optimization of scheduling parameters refers to the correct item-specific definition of planning, control and scheduling parameters and procedures as well as the ongoing readjustment of these parameter and procedure settings. To simplify matters, the term “dispensing parameter optimization” or “DPO” is often used. With the DPO, this readjustment is not done by analyzing article by article by the users and making individual adjustments to the master data according to their ideas and experience. Instead, the DPO is based on a set of disposition rules. This set of rules defines which master data settings are to be made for which article properties.
A classic and simple example is readiness to deliver. For example, an MRP rulebook could specify that all A articles with regular demand, so-called AX articles, should always be managed with a readiness for delivery of 98%, while CZ articles with highly irregular demand should only be planned with 93%. Because master data settings are not linked to a material number but to material properties, necessary master data changes can be read from an MRP system and these can be efficiently maintained in the ERP system with the support of suitable software tools.
The great advantage of these dispensing systems:
- Master data settings are based on objective rules and not on the subjective opinions of individual users.
- Using suitable tools, the master data settings can be simulatively optimized so that the ERP system generates the most economical scheduling proposals possible.
- A powerful dispatching control system enables even inexperienced dispatchers to achieve a high level of dispatching.
- The scheduling process can be significantly automated and carried out more efficiently.
There are only a few applications in which a scheduling rulebook is used practically for fully automatic scheduling. With an optimized MRP system, however, part of the scheduling work can be automated, primarily for regular items on the one hand and for irregular C-items on the other.
Ultimately, however, even the most efficient scheduling rules cannot ensure that the ERP system always generates the correct scheduling proposals for all items. When calculating order or production proposals, MRP control systems and ERP systems can only be based on the information that is mapped in the ERP system.
Much of the information available to production controllers and dispatchers is not even stored in the ERP system, e.g:
- that a supplier has temporary delivery difficulties,
- an alternative supplier is currently offering particularly favorable prices,
- a system has broken down in production,
- the sales department is in negotiations with an important customer regarding a major order at short notice.
This and similar information is stored in detail in very few ERP systems and can therefore not be taken into account when creating MRP proposals.
Experience has shown that in retail companies around 70-80% of planning proposals can be adopted by users without the need to adjust quantities or dates. For manufacturing companies, the rate is likely to be around 10% lower.
A certain proportion of scheduling proposals, but only a certain proportion, must be adapted by the users with regard to quantities, deadlines, suppliers, production facilities or similar.
In order to realize the potential of good scheduling rules in practice in the long term, suitable controlling is required to identify the extent to which actual scheduling deviates from the scheduling settings of the ERP system according to the scheduling rules. Target inventory management has proven to be an effective controlling instrument.
The core of the target stock element are target average stocks determined for specific material numbers, referred to as “target stocks” for the sake of simplicity. The target stock of an item is determined by the MRP settings of the ERP or merchandise management system according to the MRP rules.
The easiest way to illustrate the target stock level is using the example of a reorder point control system (Fig. 1):
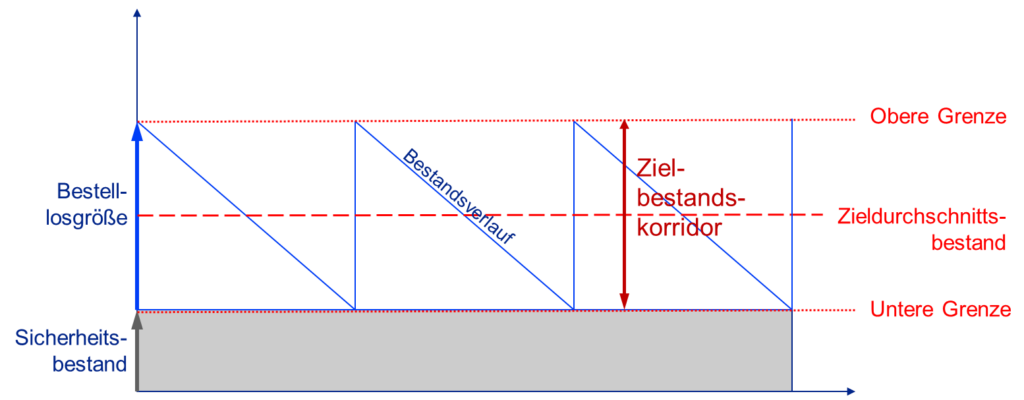
In the case of the in Fig. 1 for safety stock and order lot size results in the displayed target average stock.
Now the stock of an individual item does not run along its target average stock line but follows the typical sawtooth pattern. In relation to an individual material number under consideration, this must be taken into account in target stock management in the form of a target stock corridor (Fig. 1). If an item is planned according to the MRP settings of the ERP system, then its stock trend should be within the target stock corridor. Disruptions, such as shorter or longer replenishment times, partial deliveries, system failures or similar, can cause the stock trend to leave the corridor.
If a larger group of articles is considered instead of one article, e.g. all articles of a product group, a plant or a material type, the fluctuations in the target stock trends are neutralized and, according to the statistical law of large numbers, it can be assumed that the sum of the stocks of the individual articles at a certain point in time should correspond to the sum of the target stocks, provided that all articles are within their stock corridors.
The addition of stocks or target stocks for a group of articles cannot usually be carried out on the basis of physical units such as pieces, tons, bags or m². It makes little sense to add five hairpins to 8 laptops; the total values must be considered in monetary units. The example of the 5 hairpins at 0.5 ct each and the 8 laptops at €560 each clearly shows that the value of an item is automatically included in the target stock analysis. If the target average stock of 5 hairpins is exceeded by 500%, there are 5 x 2.5ct too many in stock. If the target stock of laptops is exceeded by 12.5%, there is €560 too much in stock. Target stock deviations for expensive items have a greater impact on target stock management than deviations for low-value items, which is intentional.
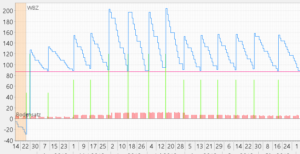
In target inventory controlling, the focus is not on the individual items, for which there are always reasons why they break out of the target inventory corridor, but on the target inventory situation in the evaluation groups under consideration (see Fig. 2), e.g:
- How large is the proportion of articles that are below the stock corridor?
- How large is the proportion of articles that are above this?
- Has this ratio improved over time?
- How many material numbers in total are below, in and above the stock corridor?
- What is the absolute value of overstock or understock?
When looking at individual articles, the TOP 10 articles with excess stock and the TOP 10 with shortages are of particular interest.
The entire target stock management stands and falls with the calculation of the material number-specific target stocks and target stock corridors. Ideal-typical considerations for determining the target inventory value, as in the example above, ignore the fact that in practice the MRP suggestions of the ERP system are occasionally off the mark unless the user intervenes. Much more reliable target inventory values can therefore be obtained by using a simulation process to determine how the item-specific replenishment settings and parameters would have behaved in the past compared to the actual daily demand situation. This results in a far more realistic target portfolio. Typically, the last twelve months of the past are simulated. In this way, the DISKOVER SCO ERP optimization system from SCT GmbH, for example, simulates the target average stock levels material number by material number.
However, initial item-specific reference values for target inventory controlling can also be created using rough formulas.
If, for example, in the case of reorder level control, you work with an order lot size that is larger than the minimum lot size but smaller than the basic requirement, the ideal stock flow is as shown in Fig. 3 is shown below.
In this case, the target average stock is calculated as follows:
Target stock = safety stock + 0.5*Max(minimum lot size; order lot size).
For sensible target stock management, the safety stock to be set must be determined by the ERP system and not set manually according to feeling and experience, otherwise the door is open to arbitrary stock levels and the entire target stock management no longer makes any real sense.
The “order lot size” to be used in the target stock determination does not correspond to the actual size of an order or a production order created, but to the order lot size as it results from the lot size settings in the ERP system.
If the order lot size is not constant, but varies from order to order, this can theoretically still be taken into account in the rough formula by using the average order lot size. In practice, however, there is usually the obstacle that the fluctuating lot sizes suggested by the ERP system in the past are no longer known. The fluctuating batch sizes can only be determined by evaluating the MRP lists from the order proposals of the future.
The key values required for target stock controlling, target stock levels and upper and lower tolerance limits are best determined monthly on a fixed date. Due to the problem described above of no longer being able to determine the actual order lot sizes proposed by the ERP system in retrospect, it should be checked in each individual case whether the average order lot size should be determined monthly in advance, while the actual stock value to be compared with it is tapped at the end of the monthly period. This evaluation is also still associated with inaccuracies, as the order lot sizes proposed by the system change several times within the monthly period for most materials.
If it is clear how the target average stock is to be calculated, then it is easy to define the upper and lower tolerance limits. To calculate the upper tolerance limit, only the full term must be added to the safety stock instead of 0.5. The lower limit of the target stock corridor corresponds to the safety stock.
Approximation formulas for target inventory management
Upper tolerance limit
= Safety stock + Max(minimum lot size; order lot size)
Target stock
= safety stock + 0.5*Max(minimum lot size; order lot size)
Lower tolerance limit
= Safety stock
Another disadvantage of the rough calculation of target stocks described above is the ideal-typical assumption of regular consumption. In practice, most items do not have regular consumption. The target stock level is only more precise and reliable if it is determined by means of simulation based on past requirements but with the current parameter settings of the article.
With such target inventory controlling, you will be able to efficiently and effectively monitor the extent to which operational scheduling and production control adhere to the specifications from the ERP system and MRP system. Track the deviations over time, scrutinize the causes of the deviations in general and the increase in deviations in particular. This will not only improve the discipline of operational scheduling and production control, but also increase the quality of your MRP system.