Best practice rules for the production kanban, part 3:
Maintenance and care
After presenting the basics and prerequisites for the introduction of a production Kanban system in the first part, the second part dealt with the concept and implementation of this system. In the final spurt, we are now finally devoting ourselves to maintenance and care and are getting straight on with it:
Basic principle 21: Sustainable success requires sustainable training.
Precisely because a kanban system seems so simple, many companies think they can get by with a quick training course for their employees. This is a fatal mistake that has caused many a kanban system to fail.
It is not enough to train employees, like Pavlov’s dogs, to develop reflexes with which they can perform “their” Kanban step. If problems arise in the Kanban process, employees should be able to make the right decisions and not improvise incorrectly. This only works if everyone involved in the kanban system understands the overall mechanism of the kanban system.
Even someone who only removes parts from kanban boxes and places the kanban card of an empty container in a “mailbox” or scans the card must know how important the correct execution of their work step is for the entire process.
In addition to the careful dimensioning of a kanban system, no other factor contributes as decisively to the sustainable success of a kanban system as employee training.
In our Kanban implementation projects, we attach great importance to training all employees in all Kanban steps. Anyone who has understood the entire Kanban process is also in a position to understand the effects of their actions on the Kanban control loop. Based on the analysis of numerous Kanban systems, we can clearly state the following:
Best practice module 21: In companies with sustainably successful kanban systems, all employees involved with the kanban system have received comprehensive training.
Basic principle 22: Pull mechanisms require reserve capacity.
The effect that the performance of the system decreases beyond 85% utilization of the storage capacity is known from automatic high-control bearings. This effect presumably also occurs when production capacities are utilized beyond 85%. Unfortunately, it is not so clearly visible in the normal interaction between many production capacities. The costs caused by frictional losses seep into many cost centers without the link to capacity overload becoming clear. If production capacities that are run through by Kanban control cycles are overloaded, this has an immediate effect in the form of a longer production throughput time and therefore a longer replenishment time.
An occasional short-term extension of the production throughput time can usually be absorbed by the safety stocks of the kanban control cycles. However, if the duration and severity of bottlenecks increase, the delivery capability of Kanban control loops can quickly collapse. To prevent such cases, capacity bottlenecks should ideally be avoided. In many cases, this can be achieved through flexible working hours and shift extensions, but rarely as quickly as the capacity bottlenecks occur.
In order to maintain the supply capability of the kanban system in such situations, heijunka mechanisms must be used or replenishment times must be extended in good time and with foresight. In both cases, however, the delivery capability of the kanban control cycles is purchased with increased kanban stocks. These can only be avoided by making production capacities more flexible, but this generally costs money.
Best Practice Module 22: Companies that attach importance to the performance of their kanban systems make sure that the capacity utilization of production does not exceed 85%
[1]
. At the capacity units where this target value cannot be met, production is leveled using Heijunka.
Correct care and monitoring
Basic principle 23: You can’t judge what you don’t monitor.
“What actually happens if we lose Kanban types? That can hardly be ruled out in practice!” This is a typical reservation that you almost always encounter when introducing Kanban solutions. If the employees are well trained and the kanban board is clearly visible, this happens far less often in reality than is feared. Nevertheless, the loss of kanban types in a purely conventionally designed and not electronically monitored control loop poses a serious risk to the delivery capability of the control loop. In reliable kanban systems connected to the ERP or PDA system, card losses can be easily detected. Cards that have been lost no longer change status (full/empty/etc.). This can be automatically evaluated and reported.
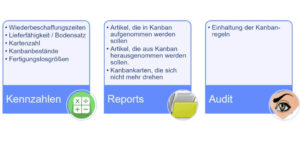
In the same way, the replenishment time from reaching the red zone to the delivery of the collective kanban lot to the supermarket can be evaluated or the delivery capability of the control cycle can be logged.
In a purely manual kanban system, many things cannot be checked and some can only be checked laboriously using tally lists: an absolute NO-GO in modern kanban systems, which are designed with the aim of working economically and conserving stock.
Only continuous monitoring through suitable reporting ensures the quality of the kanban master data and the discipline of the system process.
Best practice module 23: In successful kanban systems, the control loops are continuously monitored with regard to replenishment times, delivery capability of the control loops, compliance with the kanban rules, dimensioning of the number of cards, kanban stocks.
However, the best evaluations are useless if they are based on incorrect figures. To ensure that your controlling works, you should keep this in mind:
Basic principle 24: The basis for clean key figures are clean measuring points.
Replacement time is a very sensitive parameter in collective kanban control loops. As already mentioned, the replenishment time used in a collective kanban system is measured from the time the red zone is reached until the collective kanban lot is delivered to the supermarket.
Setting a kanban card to “empty” does not initiate production in a collective kanban system. The card moves (manually or electronically) to the kanban board and sits there until the stack of cards has reached the yellow area or the red area. Only then does production begin and only then should the stopwatch for measuring the replenishment time start. You can normally stop reaching the finish line by setting the kanban types to “full”. However, scanning a card “empty” does not record the starting point of the replacement race.
That is why we have to keep this as a small but important building block:
Best Practice Module 24: In order to be able to accurately determine the replenishment times in a collective kanban system, it is normally necessary to scan three times. In addition to “container empty” and “container full”, the system should also be scanned again at the start of production.
The monitoring of a kanban system does not end with the tracking of operational key figures. Another basic principle that your kanban system must observe is as follows:
Basic principle 25: If you want to produce in line with demand, you must also focus on demand.
If you want to limit the operation of your Kanban system to those items that do not show any fluctuations in demand, seasonality or trends, you will only be operating with a handful of parts for which Kanban is not profitable.
The days when a kanban control cycle was calculated once and for all are long gone. Companies with a professional approach to Kanban also used to calculate cleanly. However, conventional formulas for Kanban calculation make it almost impossible for you to consistently design your control loops to achieve the required delivery readiness with the lowest possible inventory. This is because fluctuations in demand are ignored in the calculations and only taken into account using a belly factor. If you were too low with the belly factor, you noticed this during operation because your supermarket was suddenly empty. If you were too high, you were always able to deliver and happy, but unnoticed with too much stock.
The correct design of a kanban control cycle works in the same way as the statistical calculation of a reorder point. As with the reorder point calculation, the required readiness for delivery and, if necessary, the delivery time must also be taken into account when designing kanban control cycles. minimum and maximum lot sizes are taken into account. Basically, a kanban control cycle is an alternative way of mapping a reorder point system[2].
The mathematical recalculation of kanban control cycles does not require a great deal of effort, provided that the system in which the recalculation is carried out receives the required consumption time series from your ERP system. The second step of re-dimensioning, the operational adjustment of the number of cards in circulation in a control loop, is not very difficult, at least with electronic kanban systems. You should always re-dimension your control loops on a monthly basis. Even if this requires some running through production to pull out and insert kanban cards on the boards.
A tough best-practice criterion applies to modern, high-performance kanban systems:
Best practice module 25: In high-performance Kanban systems, control loops are re-dimensioned on a monthly basis.
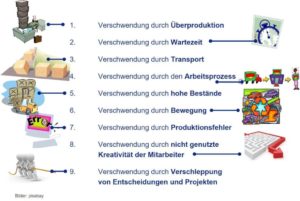
Even if the demand quantities per time unit and the fluctuation in demand remained constant, you would have to regularly re-dimension your kanban control loops and take into account changes in replenishment times and production lot sizes, which hopefully are being worked on diligently, because this is where…
Basic principle 26: A kanban system alone does not bring about continuous improvement.
Kanban systems are a building block of lean management. The central mechanism of lean management is the continuous elimination of waste (“muda” in Japanese).
Whether you are familiar with lean management or not, you should definitely focus on the potential of continuously reducing replenishment times and batch sizes so that your kanban system becomes a best-practice solution. Nice effect: If you regularly re-dimension your kanban system, you can measure the benefits of the improved logistics parameters directly in monetary terms in the form of lower circulating stocks.
Best practice module 26: The most efficient kanban systems are continuously working on reducing replenishment times and the required production batch sizes.
If you diligently implement the best-practice building blocks presented, you are well on the way to setting up an efficient and exemplary kanban system. To ensure that your efforts are sustainable, you should consider another basic principle that can destroy more than just Kanban systems:
Basic Principle 27: Human negligence reliably erodes any organizational and technical system.
Let’s be honest: to a certain extent, we all tend to be a little nonchalant about existing rules and laws. Some people and some countries more, other people and other countries less. Nothing in life is eaten as hot as it is cooked and no rule is followed as precisely as it is intended.
Because Kanban works so amazingly simply, it is often assumed that it is also easy to introduce in the company. Unfortunately, that is far from the case. Just as you cannot dimension a kanban system sloppily, you cannot handle it sloppily.
There must be clear rules for everyone and everyone must abide by the rules. This is the only way to ensure that everyone works together successfully and that all the wheels of the kanban system mesh smoothly.
But no organizational process, once set up, remains perfect for all time. The rules of a kanban system must also be adapted to the changes in the company at certain points. However, this should not be done tacitly by the employees. Problems in the processes must be discussed and, based on this, alternative processes must be coordinated and tested. If the tests are positive, the rules should be changed accordingly, otherwise the old rules will be reverted to. Defining clear standards is also a building block of lean management, but was also taught by REFA 50 years ago.
The “yellow area” in a collecting duct system is a good example of this type of control optimization, which has now become “standard”. It allows a deviation from two basic principles that must actually be strictly adhered to:
- Never request more material than is necessary and never request material prematurely;
- Never produce more parts than requested and do not produce before requested.
The “yellow area” deviates from these basic rules. By allowing production to start as soon as the yellow area of kanban types is reached, a light but clearly defined pre-production is permitted.
In practice, this control deviation has proven to be so useful that it is now part of the standard mechanism of every collecting duct system and the term “traffic light duct” (green / yellow / red area) has become commonplace.
Unfortunately, in practice we often find that Kanban rules are interpreted very generously. An efficient kanban system is not possible in this way.
There are various ways to ensure that the rules are adhered to. If you set up the monitoring of replenishment times cleverly, you can also see from the data whether any returned kanban types have been quickly added to a current production order or have been placed on the kanban board in accordance with the regulations to form the basis of the next production batch.
Ultimately, only an audit can check whether all organizational processes and rules are being adhered to.
Best practice module 27: The efficiency of a Kanban system can only be maintained if compliance with organizational processes and rules is regularly checked in audits.
Because human carelessness is so pleasant and so dangerous, you should observe another basic principle, especially in a young Kanban organization:
Basic principle 28: Education requires consistency.
From a fatalistic point of view, change management can be compared to raising children: It takes 18 years and still sometimes goes wrong.
In addition to many causes that cannot be influenced, there are two levers that must be actively addressed: clear rules and consistency.
We have already identified a best practice building block for the “rules”. We still need to talk about consistency, because despite audits, you will hardly be able to ensure that all defined rules of the Kanban mechanism are always fully complied with.
Do you still remember your driving school days? We would probably all fail our driving test today, because in practice we apply some rules more generously than we originally learned them. It takes some driving experience to understand which rules of the road you have to strictly adhere to and which ones you can be a little more generous with in practical driving behavior without endangering yourself and the traffic. The driving instructors’ insistence ensured that we not only learned the rules and regulations, but also internalized them and largely adhered to them.
The same applies to a kanban system: with growing experience in handling a kanban system and a growing understanding of the kanban mechanisms, you can optimize rules or handle certain rules more generously. However, the latter inevitably leads to chaos if the Kanban rules are not internalized. If the employees’ Kanban compass is in order, any deviation from the rules automatically causes a guilty conscience and pulls everyone back onto the path of virtue.
The American psychologist Anders Ericcson came up with the 10,000-hour rule. This states that one must have studied a subject for 10,000 hours in order to master it at a world-class level, assuming talent.
If you have spent 10,000 hard hours mastering a task over and over again, then mechanisms have become second nature to you that you adhere to without having to think.
In our experience, this principle also applies to Kanban. Compliance with rules must be consistently monitored and enforced over a certain period of time so that employees internalize them. Once a behaviour has been internalized, once we have “settled in”, it causes us a certain discomfort if we deviate from the path of internalized virtue. We have repeatedly encountered the “educational” consequence in successful Kanban companies.
Best Practice Module 28: In a Kanban organization that is to remain efficient in the long term, all rules should be strictly adhered to without tolerance for the first 12 – 18 months in order to internalize the rules. If possible, only start optimizing processes afterwards.
Basic principle 29: Every “system” requires maintenance and care.
The decentralization of production control is a key feature of a kanban system. Some companies therefore believe that they can do away with production control by introducing a kanban system, but a production control function is still required even in a kanban system. However, the task of a production controller for Kanban parts differs significantly from the task in a classically organized production system. In the Kanban mechanism, planning and execution are separated from each other. Production control is responsible for maintaining and regularly resizing the kanban system, while production itself makes the operative scheduling-relevant decisions. No parts or dates are chased in a Kanban system. The entire Kanban mechanism is designed and calculated from the outset and is re-dimensioned so that this is not necessary. The classic production control mechanism, on the other hand, is often still manually oriented and more concerned with the elimination of faults than with their systematic prevention.
When introducing kanban systems, it is tempting to reduce production control costs to well below 50%, and initially this seems possible without causing problems.
After some time, however, you will notice that stocks increase and/or parts and dates are hunted again. In this case, either the effort in production control increases significantly again, or the kanban system gets out of hand.
Only in a well-maintained kanban system can the potential faults be adequately compensated for and thus relieve the production control system.
Best Practice Building Block 29: Companies with sustainably successful Kanban organizations give production control sufficient time to maintain the control loops and therefore reduce the production control effort for the Kanban parts by a maximum of 50%.
CONCLUSION: Kanban is worth the sweat of the brow
We had to compile many, sometimes very detailed best-practice modules for the simple and transparent production Kanban. How important these many aspects can be may become clear if we point out one last basic principle:
You only have the chance to introduce Kanban once every 10 years.
If you have “messed up” the introduction of new organizational processes, it takes some time before you can try again without directly encountering resistance from those affected. When introducing Kanban, the time needed to let the grass grow over the matter seems to be particularly long. However, if you make the effort to introduce your production kanban carefully and approach the project with the aim of achieving an exemplary solution, you will be rewarded with a cost-effective, economical and stock-friendly replenishment mechanism. Kanban is worth the sweat of the brow!
[1 ] This should not only apply to kanban control loops, but to all production capacities regardless of the production control mechanism.
[2 ] If you want to design your safety stocks correctly in both cases, this requires more mathematics than your ERP system probably uses for a statistical calculation of the reorder level. The reason for this lies in the so-called “non-normally distributed demand”. However, this discussion would go too far here. For further information, please refer to the article “Best-practice building blocks for sales forecasting”.