A tailor-made suit for efficient planning and control of procurement and production at Oras Group
by Andreas Capellmann, Olli Mäkilä and Steffen Trautwein[1]
By using the DISKOVER APS system for planning and controlling procurement, production and assembly, the Oras Group has a sophisticated solution for the efficient handling of day-to-day business.
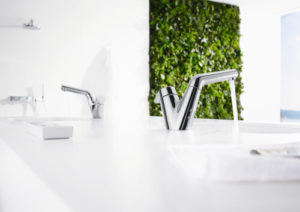
Oras Group, headquartered in Rauma, Finland, is the market leader for sanitary fittings in Finland and took over what is now Hansa Armaturen GmbH in Stuttgart in 2013. This made Oras Group one of the leading manufacturers of sanitary fittings in Europe. With 1370 employees at four production sites in Burglengenfeld (Germany), Kralovice (Czech Republic), Olesno (Poland) and Rauma (Finland) and its own sales offices in 20 countries, the company generated sales of € 245 million in 2015.
The merger of the two companies required new business processes in the entire order processing and the planning and control of procurement and production processes. Oras Group planned and managed its entire value streams using the American ERP system QAD. Hansa GmbH, for its part, used BAAN IV as its ERP system. However, the entire operational order processing was carried out using the DISKOVER add-on system from SCT GmbH in Herzogenrath/Aachen.
When comparing the processes, it quickly became clear that the QAD system was much more powerful than the outdated BAAN IV release, so it quickly became clear that the new Oras Group would work with QAD as its common ERP system. However, it also became clear that DISKOVER as a planning and scheduling system offers far more options for efficient order processing than would be possible with the ERP system alone. And so the strategic decision was made to roll out QAD as a joint ERP system and DISKOVER as an operational planning and control system throughout the entire Oras Group. In mid-2015, the former Hansa sites in Stuttgart (administration), Burglengenfeld (production) and Kralovice (assembly) switched to the QAD system; the final separation from the BAAN system took place at the end of 2015.
The introduction of DISKOVER at the Oras Group sites in Rauma and Olesno was very efficient thanks to the high user-friendliness of DISKOVER. To ensure that the planning and control processes are supported as effectively as possible, 12 months were allowed for the rollout. Apart from three workshops in Finland and one workshop in Stuttgart, the entire system introduction was carried out by telephone and video conference, with great importance being attached to weekly coordination meetings right from the start.
From the start of the rollout project, several production sites as well as distributed logistics centers and sales branches were directly integrated to ensure that multi-plant planning was truly designed as an end-to-end process. Initially, the focus was on analyzing the data and determining in detail how the existing processes and supply relationships should be mapped.
Today, the Oras Group has a sophisticated order fulfillment process that is handled entirely by DISKOVER, from sales forecasting to production control and procurement. In total, around 80 employees work with the system. DISKOVER supports a whole range of special sub-processes:
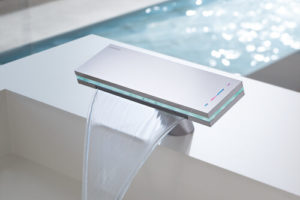
The sales department sees the supply situation
This begins with the connection of the sales department. Via a web interface, the sales department can see what the stock/demand situation is for the desired end products when a customer makes an inquiry. He sees the available stock, the customer orders already dispatched and a summary of the next receipts at weekly level. In the event of delivery bottlenecks, the production controllers can also enter comments that are displayed to the sales department in this list. In many cases, this is enough for the sales department to be able to provide delivery dates. In critical cases, the ATP function of the QAD system can be used.
Scantling dimensioning and automatic storage location determination
At the Kralovice and Burglengenfeld plants, the value streams at the production and assembly sites are linked together by Kanban processes. Final assembly is supplied by Kanban from prefabrication (electroplating and mechanical processing), which in turn is supplied by the basic stage (foundry). The kanban control cycles are dimensioned by DISKOVER on the basis of a special kanban calculation algorithm that allows each kanban control cycle to be set to a defined readiness for delivery. As storage capacity at the final assembly plant in the Czech Republic is tight, only the fast-moving parts are stored there. The remaining parts remain at the Burglengenfeld site and are only sent on to Kralovice when required. Which parts are to be stored in the Czech Republic and which in Germany is determined by DISKOVER on the basis of specific key figures.
Heijunka board for leveling the foundry
In the foundry, the production order sequence must be differentiated for reasons of set-up optimization on the one hand and capacity balancing on the other. Oras Group uses the digital Heijunka board from DISKOVER for this purpose. In this module, production orders can be loaded onto the various casting systems using drag-and-drop.
Automatic generation and dispatch of picking lists
Each production order requires material from one or more warehouses, either at the same location or from a different location. DISKOVER automatically generates a pick list for a production order for each warehouse from which material is required. This is either sent there by email, printed out directly on a network printer in the relevant warehouse or transmitted online to the relevant warehouse management system. Each warehouse uses these picking lists to compile the required components and assigns the production order number to the consignment. On arrival at the assembly site, the components that have arrived are checked off an additional overall list generated by DISKOVER. As soon as all components are available, they are taken to the workstation already on the complete list.
All-round service and ongoing process coordination
Thanks to DISKOVER’s special service concept, ongoing coordination between the system users at Oras and the SCT GmbH service center in Herzogenrath/Aachen is very close, so that work on further optimizing the processes is ongoing.
In a further optimization step, for example, the sales department is to be integrated even more closely into demand planning on the basis of DISKOVER’s Sales Forecast module.
[1 ] Andreas Capellmann is Managing Director of SCT GmbH in Herzogenrath / Aachen. The company is the manufacturer of the DISKOVER APS system and is part of the A&K Group. Olli Mäkilä is Manager, Materials Management at Oras Group, Steffen Trautwein is VP Purchasing & Logistics at Oras Group.