by Adalina Elsner; Götz-Andreas Kemmner[1]
Additive manufacturing processes, often referred to colloquially as 3D printing, have undergone drastic further development in recent years. What seemed impossible yesterday is already standard in additive manufacturing today. As additive manufacturing can be used to produce in batch sizes of 1 with practically no set-up costs, the manufacturing industry has high hopes for these processes in order to get a grip on the diversity of variants in production.
This article provides an overview of today’s dominant additive manufacturing processes, discusses the advantages, disadvantages and legal aspects of additive manufacturing and summarizes the opportunities and risks of additive manufacturing for logistics.
Even though there are now a large number of different additive manufacturing processes, they all follow the same basic idea. According to this idea, an object is built generatively on the basis of digital 3D design data by creating individual layers of material. This is achieved by applying energy to an initially shapeless material to solidify it at the desired points, thus forming successive layers that bond together. The major advance over conventional production methods here is that products can be created directly from CAD models without having to significantly adapt the production systems or create suitable tools.
Today, additive manufacturing consists of a wide range of different technologies, which differ in terms of the materials to be processed, the installation space, the surface quality, the production speed and their costs. Most additive manufacturing processes can be assigned to one of seven categories. These categories are
- Material extrusion,
- Binder Jetting,
- Layer lamination,
- Photopolymerization in the bath with laser light source or controlled area light,
- Material Jetting,
- Powder Bed Fusion and
- Directed Energy Deposition.
Figure 1 shows the prevalence of the most widely used additive manufacturing processes.
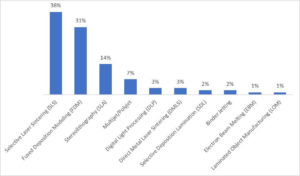
In material extrusion, fused deposition modeling is the most common process, as it is the most user-friendly and most common additive manufacturing method for non-commercial use. FDM is a manufacturing process in which a workpiece is built up layer by layer from a meltable plastic using an additive process. FDM is one of the most cost-effective methods. However, the components produced using the FDM process often do not have a particularly high surface quality and have clearly recognizable layers.
The best-known binder jetting process is 3D printing, where the workpiece is built up from powdered material using a layering process. Similar to inkjet printers, many 3D printers have several print heads from which droplets are shot in the form of small binders. The liquid binder crystallizes the individual powder grains of the current production layer and can be compared to glue. The finished models are freed from the surrounding powder and, if necessary, infiltrated with a type of superglue, which acts as a kind of sealant. The process has the major disadvantage that reworking is always necessary after printing and objects that have not been infiltrated are very brittle.
One example of layer lamination is laminated object modeling. In this process, the component is built up additively from layers of paper or films made of ceramic, plastic or aluminum. Each new layer is laminated onto the existing layer to form a stable object. The outlines are then cut with a knife, a hot wire or a laser. The next layer can then be applied. This process generates waste that has to be disposed of. However, the material costs are low and the end products can be made very durable with epoxy resins.
Photopolymerization in the bath with laser light source or controlled area light
The photopolymerization category includes processes such as stereolithography (SLA or STL), digital light processing (DLP) and vat polymerization. In stereolithography, a light-curing liquid plastic, for example synthetic or epoxy resin, is cured in thin layers by a laser. This takes place in a bath filled with the base monomers of the light-sensitive plastic. The STL process is the longest commercially used rapid prototyping process to date, allowing a wide range of experience and materials to be used. The process can also be used to create very fine and smooth surfaces with a high level of detail. Nevertheless, the finished parts often only have a minimal thermal and mechanical load capacity. In addition, the STL process is one of the most expensive additive processes due to the very high material costs.
A common example of material jetting is multi-jet modeling, in which a model is created layer by layer using a print head similar to that of an inkjet printer. The material, which is liquid in its initial state, is polymerized and solidified immediately after printing using UV light. Waxy thermoplastics and UV-sensitive photopolymers are used as materials for the MJM process. The printing process with this method takes quite a long time, but very fine details and a high print resolution can be generated during printing.
In powder bed fusion, powder layers are applied one after the other in the build chamber and fused or sintered at the desired points using heat to create a component. Many additive manufacturing processes follow this basic principle and can be divided into three subcategories: laser sintering, laser melting and electron beam melting (EBM). These processes are among the most common methods for the additive processing of metals.
One of the most common processes in the directed energy deposition category is laser cladding. In this process, almost any metal is applied to a workpiece by melting and simultaneous deposition. A powerful laser is used as the heat source for laser cladding. This process can also be used to apply metals to an existing tool surface, which can be used to repair tools or refine their surfaces, for example. However, the process is just as suitable for producing metal prototypes. Laser cladding produces a fine-grained microstructure that results in a dense product with good metallurgical and mechanical properties.
Space Puzzle Molding (SPM) is a form of plastic injection molding. This technology makes it possible to produce components in series-identical quality. This process also makes it possible to produce quantities of over a thousand.
Polyamide casting is a process in which components are manufactured from thermoplastic materials. Polyamide casting is particularly suitable for the production of high-volume castings.
With the Contour Crafting (CC) technology, it is possible to use concrete as a production material. The concrete is dispensed via a nozzle and applied with a spatula. Compared to other additive manufacturing methods, the CC process can be used to produce very large objects, such as entire houses.
Advantages and disadvantages of additive manufacturing and legal issues
Most additive manufacturing processes are very flexible, which means that no or only very short changeover times are required if different products are to be produced on the same machine. Likewise, fewer different tools are required, which can lead to a significant reduction in costs, especially for several more complex products. Additive manufacturing processes are therefore particularly suitable for manufacturing products with many possible variations and small volumes per variation. Similarly, additive manufacturing processes make it possible to manufacture products that previously consisted of several individual parts in one piece. In addition, some additive manufacturing processes are able to carry out cost-efficient production processes with different materials, which means that a separate machine is no longer required for each individual production step. The flexibility of the technology also means that product details can be adapted very individually to customer requirements and in some cases even products can be produced that were previously impossible to manufacture using conventional production methods due to technical hurdles. In addition, the flexibility of additive manufacturing systems means that production can increasingly take place close to the customer, which significantly reduces transportation routes and costs, as well as storage costs.
However, additive manufacturing processes are often not yet fully developed and can sometimes only manufacture products of lower quality than conventional processes. Furthermore, the number of materials that can be used for additive manufacturing is still significantly lower than for conventional processes. Many existing additive manufacturing processes are often still very slow and therefore generate high variable costs. In addition, additive manufacturing systems that can produce high-quality products usually have very high acquisition costs. Another disadvantage is that the scanning process of complex products to create the corresponding CAD files can often be very costly and time-consuming. In addition, additive manufacturing generally does not benefit from the economies of scale effect. Although this means that small to medium output quantities can benefit greatly from additive manufacturing, it is very likely that additive manufacturing will not be able to keep up with conventional mass production from a cost perspective when it comes to large output quantities. In addition to the costs for the actual production, it should not be neglected that significant additional costs can arise for the post-processing of additively manufactured products, depending on the product and process.
From a legal perspective, there are also still a number of unresolved issues in connection with additive manufacturing. The biggest problems are the copyright and patent law bases, standards and certifications, as well as liability issues. Essentially, the question is how intellectual property can be protected. Safety guidelines and ethical aspects must also be considered, as the 3D data for the additive manufacturing of firearms, for example, could be published.
In addition, quality approval is a major challenge in additive manufacturing, as not enough experience has yet been gained regarding the build quality and durability of additively manufactured components.
The restrictions of additive manufacturing presented above suggest that, despite their dynamic development, these manufacturing processes will continue to bring their advantages to bear in the future, especially in special production and demand niches, and are unlikely to lead to a widespread revolution in production technology.
Challenges and opportunities of additive manufacturing in logistics
However, assuming that additive manufacturing can overcome the majority of the restrictions described, it could have a major impact on existing logistics processes. The supply chain in particular could become increasingly streamlined and transportation over long distances could decrease significantly. Storage would also be greatly reduced. Additive manufacturing would also mean that some stages in the value chain would be eliminated and the main added value would increasingly lie in design rather than in production itself. This development would be particularly reinforced by the fact that many production and assembly steps could be eliminated if products are manufactured in one piece using additive manufacturing. In addition, many processes in purchasing could be digitalized by eliminating complex intermediate products, which would eliminate or significantly simplify some tedious and labour-intensive tasks in this area. In addition, local production means that producers are already close enough to their customers to sell their products directly to them without intermediaries.
In general, cost savings can be achieved with additive manufacturing because the lower number of raw materials and tools required for additive manufacturing compared to conventional technologies means that planning reliability is significantly higher. As a result, fewer orders for raw materials can be placed, each in larger quantities, thus reducing delivery costs. The increased planning reliability leads to lower warehousing costs and a reduced risk of not having enough raw materials available. The use of more standardized raw materials and a low demand for subcomponents also means that a much smaller supplier network is required, which often results in fewer negative influences from different places of origin of the raw materials, such as customs duties or other trade barriers, but also differences in quality.
Increasingly decentralized production close to the customer theoretically makes it possible to produce in a completely decentralized manner around the world in line with demand, as additive manufacturing has the advantage over all other technologies that it can be used to produce directly from digital data. The storage space required could also be significantly reduced with decentralized production and there would be no need to keep stocks of rarely required spare parts or components and other slow-moving products. In addition to reducing storage and manufacturing costs, delivery times and routes could also be shortened. Especially for very globally positioned logistics companies, which generate a large part of their turnover through transportation over long distances, production on demand close to the customer would therefore lead to significant losses in turnover, which could ultimately jeopardize their business models.
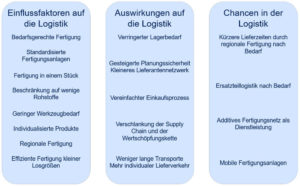
Decentralized production would create demand for well-distributed additive manufacturing networks close to customers, where various product developers could have their products manufactured. The establishment and operation of such manufacturing networks offers a major business opportunity for existing logistics companies. However, this step would ultimately result in an increasing separation of developers and manufacturers. In addition to a permanently installed additive manufacturing network, it would also be conceivable to use mobile additive manufacturing systems that can adjust their position as required. Such business models could make it possible to adapt the production of individual products very closely to actual demand and still be able to deliver promptly.
[1 ] Adalina Elsner is studying for a master’s degree in logistics at the West Saxon University of Applied Sciences in Zwickau. As part of her bachelor’s thesis, she looked in detail at the influence of additive manufacturing on logistics.
Dr. Götz-Andreas Kemmner is Managing Director of Abels & Kemmner and Honorary Professor of Logistics and Supply Chain Management at the West Saxon University of Applied Sciences.
Bibliography
- com (2017): Siemens installs 3D-printed parts in the Dubai metro,
https://3druck.com/blog/siemens-verbaut-3d-gedruckte-teile-in-der-u-bahn-von-dubai-2161107/ (15.08.2017)
- (2017): The revolution of the logistics chain with 3D printing,
https://www.3yourmind.com/logistikkette-mit-3d-druck (15.08.2017)
- net: Additive manufacturing a potential future market for academics
http://academicworld.net/karriere/additive-fertigung-ein-potenzieller-zukunftsmarkt-fuer-akademiker/ (15.08.2017)
- acatech – National Academy of Science and Engineering, German National Academy of Sciences Leopoldina (2016): Additive Manufacturing, in Union of the German Academies of Sciences and Humanities, Munich p. 6-32
- AEB (2014): White Paper: Six theses on how 3D printing is changing logistics
http://documents.aeb.com/brochures/de/aeb-white-paper-3d-druck.pdf (15.08.2017)
- Baldinger, M. (2015): Approaches to managing the additive manufacturing supply chain. RTeJournal – Expert Forum for Rapid Technology, Vol. 2015.
- Dachser (2015): Logistics from the printer
http://www.dachser.com/de/de/Logistics-out-of-the-printer_3912.htm (15.08.2017)
- Fastermann, P. (2012): 3D-Druck/ Rapid Prototyping/ Eine Zukunftstechnologie – kompakt erklärt, in: Springer Vieweg, Düsseldorf, pp.5-130.
- Feldmann, C./Pumpe, A. (2017): A holistic decision framework for 3D printing investments in global supply chains, in: Transportation Research Procedia, Vol. 25, pp. 677-694
- Fraunhofer Institute for Material Flow and Logistics: Additive manufacturing topic brochure
https://www.iml.fraunhofer.de (15.08.2017)
- Frey, S. (2015): 4 theses on how 3D printing will change logistics,
https://www.handelskammerjournal.ch/de/4-thesen-wie-der-3d-druck-die-logistik-veraendern-wird (02.08.2017)
- Glossner, S./ Leupold, L. (2016): 3D printing, additive manufacturing and rapid manufacturing Legal framework and entrepreneurial challenge in: Vahlen, Munich
- Grassl, W. (2016): Additive Manufacturing – Strategy & Operations Focus Analysis,
https://assets.kpmg.com/content/dam/kpmg/pdf/2016/04/ch-additive-manufacturing-de.pdf (15.08.2017)
- Güngör, K. (2017): Additive manufacturing: Change for production and supply chain, in: IPL-Magazin, Vol.38, S 2-5.
- Heutger, M. (2016): 3D PRINTING AND THE FUTURE OF SUPPLY CHAINS – a DHL perspective on the state of 3D printing and implications for logistics in DHL Trend Research,
- Hirschberg, C. (2017): Pressure on logistics, A new era begins in 3D!, in: IPL-Magazin Vol.38
- Hoffmann, E./ Oettmeier, K. (2016): 3D printing: How additive manufacturing processes are revolutionizing the economy and its supply chains, in: Zeitschrift Führung + Organisation (ZFO), Vol.85, pp. 84-90
- Intralogistics in Vision (2015): 3D printers & logistics
http://intralogistik.tips/3d-drucker-logistik/ (05.08.2017)
- Jiang, R./Kleer, R./Piller, F. T. (2017): Predicting the future of additive manufacturing: A Delphi study on economic and societal implications of 3D printing for 2030, in Technological Forecasting & Social Change, Vol. 117, pp.84-97
- Juschkat, K. (2016): 3D printing in series production,
https://www.konstruktionspraxis.vogel.de/3d-druck-in-der-serienproduktion-a-556439/ (15.08.2017)
- Langkau, S./ Heidemann, N. (2017): The growing influence of 3D printing,
http://www.dvz.de/rubriken/logistik-verlader/single-view/nachricht/einfluss-der-3-d-drucktechnik-waechst.html (02.08.2017)
- Leichtbau BW GmbH (2014): ADDITIVE MANUFACTURING IN LIGHTWEIGHT CONSTRUCTION – STRATEGIC AND ECONOMIC CHALLENGES AND PERSPECTIVES
- Logistik-aktuell.com (2015): 3D printing: logistics experts develop new business models
https://logistik-aktuell.com/2015/11/17/3d-druck-logistiker-entwickeln-neue-geschaeftsmodelle/ (11.08.2017)
- Logistik-aktuell.com (2017): GE Aviation – additive manufacturing in the aircraft industry,
https://logistik-aktuell.com/2017/02/21/3d-druck-in-der-flugzeugindustrie/ (11.08.2017)
- Pankow, G. (2017a): 3D printing in the automotive industry – disruption or hype,
https://www.produktion.de/trends-innovationen/id-3d-druck-in-der-autoindustrie-disruption-oder-hype-122.html (04.08.2017)
- Pankow, G. (2017b): MAN sees potential for large-scale production,
https://www.produktion.de/trends-innovationen/id-3d-druck-in-der-autoindustrie-disruption-oder-hype-122.html?page=2 (04.08.2017)
- Pickert, C./ Wirth, M. (2013): Additive manufacturing processes, in: CEDIFA Arbeitsbericht, Vol.1, pp. 1-26.
- Pour, M. A./ Zanardini, M./ Bacchetti, A./ Zanoni, S. (2016): Additive Manufacturing Impacts on Productions and Logistics Systems, in: IFAC-PapersOnLine, Vol. 49-12, pp. 1679-1684.
- Rudolph, J. P./ Emmelmann, C. (2017): A Cloud-based Platform for Automated Order Processing, in: Procedia CIRP, Vol. 63, pp. 412-417
- Silva, J. V. L./Rezende R. A. (2013): Additive manufacturing and its future impact in logistics, Fortaleza
- Thomas, O./ Kammler, F./ Zobel, B./ Sossna, D./ Zarvic, N. (2016): Supply Chain 4.0: Revolution in logistics through 3D printing, in: M+io Fachzeitschrift für Innovation, Organization und Management, Vol.1, pp. 58-63.
- Weinzierl, S. (2016): SAP and UPS want to simplify the process chain for 3D printing,
- Witzleben, S. (2014): What can logistics expect from 3D printing? Status quo and prospects at a glance, in: Bundesvereinigung Logistik Vol.1, October 2014.
- Zscheile, F. (2015): Goods flows to data flows,