Act local and serve information globally
by Edvard Rückert, Götz-Andreas Kemmner, Martin Jürgens
The trend in the automotive industry is based on the motto “shorter product life cycles and faster time-to-market”. In order to meet these ever-increasing challenges, the supplier companies, many of which have a medium-sized structure, are doing everything they can to synchronize cooperation in the vertical supply chain. However, this is extremely laborious using conventional means. The Internet now opens up the opportunity to simplify decentralized project management through centralized data storage. An Internet cooperation platform called Kopl@ is being developed for this purpose in a joint project by six automotive suppliers. Kopl@ is intended to centrally structure the cooperation between the development employees of the 6 participating companies.
Similar to many supplier companies, WITTE from Velbert is taking the approach of working closely with selected suppliers in the development and manufacture of new products in the form of a network. For each order, a group of companies and employees is formed according to requirements in order to combine the best qualifications for a given task. Once a joint order has been acquired, the responsible employees of the respective companies must sit down together and master the job together. Unfortunately, they are not sitting on the same floor or in the same building, no, in this particular case they are sitting hundreds of kilometers apart. As a result, they have to come up with a sophisticated project management system to ensure that the benefits of collaboration are not negated by travel times and scheduling problems.
Project management must therefore be centrally controllable across company boundaries. WITTE-Velbert practices cross-company project management with its suppliers C.W. Hanebeck (Iserlohn), Gebr. Wasserloos (Velbert), Lahme (Kierspe), Paragon (Delbrück) and Schrimpf & Schöneberg (Hohenlimburg) have been successful since 1997; and since July 1999, the six companies have been working on a web-based central communication system as part of the VIA initiative of the state of North Rhine-Westphalia, to which all participants should have access. The project, code-named Kopl@ [Kopla], is used to exchange and store data and information, structure development processes, distribute project tasks and monitor project progress.
In the past, missing or inconsistent information (what is the current version of the protocol?) meant that the need for coordination and travel time as well as the costs for changes threatened to explode: The previously practiced distribution of digital and printed data did not lead to the desired transparency. There was the problem of promptly maintaining the data, which also had to be prepared twice and three times or, in this specific case, up to six times, which increasingly burdened the project staff with the management of information. Sales and project engineers, often on site with customers for days on end, were only able to obtain information on the current status of individual projects by telephone. The managers at WITTE-Velbert and the supplier companies involved were only able to find out about the current situation in the individual projects through project status reports and personal discussions.
The World Wide Office
Kopl@ should therefore provide relief on the project front. It is intended to be a shared virtual office in which all project employees can work together, no matter where they are in the world. All project documents and other information are stored in this shared office. Employees are supported in their search for information by a search system that creates a running full-text index and can execute complex search queries in dialog.
Recurring organizational processes are stored in predefined “workflows” and users are automatically informed about new or changed information and documents that affect them. Project handling and transparency are supported by joint task management and, if required, joint scheduling coordination.
In the case of product development projects, the product development process is structured and channeled through project phases with gate reviews and tracking documents. This means that project activities remain transparent not only for the project team members and the project manager, but also for members of an extended project team, the sales department and the management. The frequency of face-to-face meetings can be reduced and all those affected have the same level of information.
In order to cover this extensive range of services, the management consultancy Abels & Kemmner, which was commissioned with the design and implementation, is building on the Livelink® e-management tool from Opentext, expanding it with specific modules and configuring the system into a “management system for virtual companies”. According to the structure of Livelink, the user of Kopl@ moves in three work areas. Information that only the user has access to can be stored in the personal workspace. The project teams work together in project areas (Fig. 1), while the company workspace is available as a forum and source of information for all Kopl@ users. In the three work areas, the methods shown in Fig. 2 listed objects.
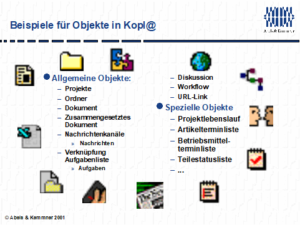
As the confidentiality of data and information is important in product development, Kopl@ offers a sophisticated authorization system. Users can be granted different access rights depending on their group membership and their role in projects, and individual access rights can also be defined for each object.
It is already clear that working with Kopl@ will save users time and effort, as information can be obtained more easily and quickly and tasks are less likely to be returned to the user’s desk for reworking or modification (Fig. 3). From the company’s point of view, development efficiency is also improved, development times are shortened and development costs are reduced.
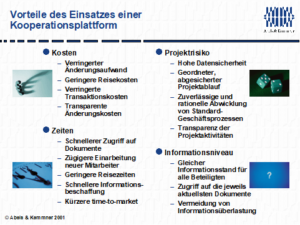
In addition, it is hoped that the increasing number of users and project management using Kopl@ will increase the knowledge base that can be accessed within and across companies. As the value, success and viability of a company are increasingly determined by the knowledge available within a company, the use of a cooperation platform such as Kopl@ is of strategic importance for VIA.
Summary
Controlling decentralized project development via the Internet. The trend in the automotive industry is “Shorter product life cycles and faster time-to-market”. The cope with this constantly rising challenge the largely medium-sized and small enterprises are doing everything they can to synchronize cooperation in the vertical supply chain. The Internet opens up the opportunity to simplify decentralized project-management by way of central data retention. In a joint project by six automobile component suppliers an Internet cooperation platform has been developed, named Kopl@, which is intended to structure the cooperation of development staff of the companies involved centrally.