MEDION and Abels & Kemmner develop innovative spare parts management system
Outstanding after-sales service is the way to stand out in the consumer electronics sector, which is why MEDION attaches great importance to the supply of spare parts. The products are subject to special requirements in terms of spare parts supply: Short product life cycles, high-priced spare parts and unpredictable spare parts requirements characterize this business. Nevertheless, together with Abels & Kemmner, MEDION was able to develop an intelligent and innovative solution for stocking spare parts.
MEDION AG is one of the very few companies with a comprehensive portfolio of consumer electronics and information technology products. In terms of product groups, MEDION focuses on three pillars:
- PC/multimedia (e.g. personal computers, notebooks, TFT screens, scanners, printers, software, etc.)
- Consumer and household electronics (e.g. televisions, flat and plasma screens, DVD players and recorders, hard disk recorders, etc.)
- Communication technology (e.g. SAT systems, decoders, telephones, fax, answering machines)
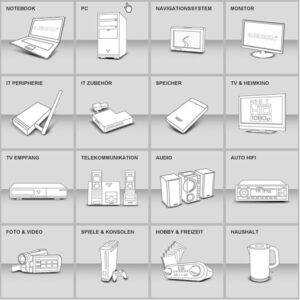
The company operates according to the so-called “build-to-order” principle, i.e. the devices are only produced in the required quantities once orders for sales promotions have been received from retail partners. The advantage of this strategy is that no storage costs are incurred – a cost saving that the company passes on to its customers and therefore impresses with a particularly good price/performance ratio. It also ensures that the company’s products are always up to date. In addition to Germany, MEDION also has a strong geographical presence in the entire eurozone, including Scandinavia and the UK, and very well-positioned and professional sales and service units in conjunction with its retail and cooperation partners.
Customer service as the highlight of the service range
Now you might think that such a business is quite simple: create and distribute product ideas, manufacture and deliver and that’s it. However, this is not the case: MEDION provides a particularly important element of the overall service for retailers and manufacturers through its own after-sales service for the end consumer, so that the partners do not have to worry about this business. A 365-day hotline in the company’s own call center provides expert support for questions about the application, warranty processing and repeat orders. MEDION also carries out all necessary repairs and, if necessary, commissions an on-site service for special products within Germany, which visits the consumer to provide advice or carry out repairs. MEDION guarantees a high availability of spare parts in order to be able to satisfy the end customer with fast problem solving, thus underlining the quality of the brand even in the case of service.
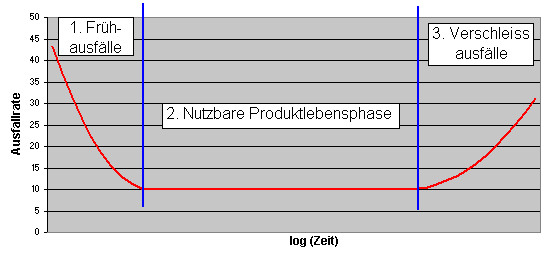
The warehouse for products without stock
This means that MEDION cannot manage entirely without a warehouse, as the correct stocking of replacement components is of particular importance. The particular challenge is that the spare parts cannot be procured for the entire warranty period. Manufacturers of the parts cancel these well before the end product’s warranty period expires. Motherboards for PCs are often only available in identical configurations for a few months, and plastic housings for notebooks, for example, are often only available during production itself. The appropriate hinge, should it be defective during the warranty period, must therefore also be ordered in good time. Finally, MEDION must ensure that spare parts are kept in stock for the remainder of the warranty period. At this point in time, however, there is hardly any information available on the demand for spare parts, as the products have not been in use at the customer for long. This harbors two dangers:
- If stocks are too low, spare parts run out and customer appliances can no longer be repaired.
- If stocks are too high, MEDION will be left with high inventories at the end of the warranty period, which will significantly increase costs.
As part of the investigations, the consumption series of the spare parts were analyzed and evaluated. Due to the very short consumption periods (< 6 to 12 months) and the very erratic demand, classic methods such as mean value, exponential smoothing and median were not suitable for forecasting or did not offer any advantages over the method used to date. For this reason, past projects were examined more closely and the consumption series were analyzed with regard to their failure behavior. Special types of failure patterns emerged: A total of five different types were identified and assigned to so-called norm curves. Depending on the failure rates at the beginning of product use, in the middle and at the end of the warranty period, the components could be assigned to the standard curves (see figure Standard curves). It was no surprise that failure patterns were not necessarily specific to a particular assembly. Electronic components, for example, were to be found in all areas, as were mechanical components. The application of the standard curves could therefore not simply be regulated via the product group. Separate rules and indicators had to be used for this.
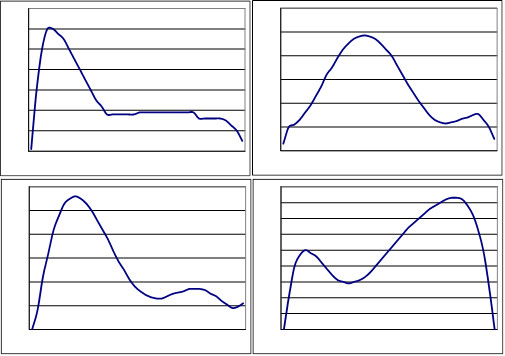
In the second step, methods were developed for using these standard curves to forecast spare parts requirements. As this was a very complex and computationally intensive task, a prototype of an analysis software tool was specially developed to process the failure data and determine forecasts based on the standard curves. By assessing the first phase of the consumption period, users can assign the most suitable failure pattern to the spare part and determine the requirement within the warranty period. The user also has options for manipulating the forecast. This makes it possible to map the user’s extensive experience via the tool. The forecast values are based on the standard curve. This can then be stretched or compressed with simple clicks or the consumption periods can be reweighted. The tool is very graphically oriented and provides very quick information about the consumption and demand situation.
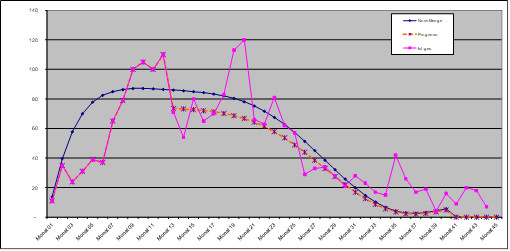
In the final step, the methodology was validated. Forecasts were determined at certain points in the past on the basis of the information available at that time and compared with the forecasts made using the method applied to date. The result was clear: The new methodology now makes it possible to make better predictions about spare parts requirements. In particular, it was possible to improve the coverage of residual requirements by a double-digit percentage, which has noticeably improved delivery readiness. at the same time as reducing stocks, making this project a double success.
In the next step, the new methodology will be implemented in the standard product DISKOVER SCO for forecasting and scheduling optimization, so that corresponding functionalities can already be used for spare parts management with the standard software. Further information on DISKOVER SCO is available on the Internet at www.diskover.eu