Possibilities and limits of batch size optimization
Dr. G.-A. Kemmner1
Batch-sizing processes for reducing the cost of warehousing and procuring a specific good are an important topic for decision-makers in logistics. However, in order to fully exploit the potential, users must also be aware of the limitations of lot-sizing methods and be aware that it is not possible to take all interdependencies across the entire company into account with these methods. Appropriate methodological expertise across the supply chain is therefore required for use in the strategically right place.
Lot-sizing methods are used to calculate an optimum between inventory costs and procurement costs in order to minimize the total costs of the supply chain. The problem here, however, is that a batch size decision, e.g. for a specific value-added step in production, does not necessarily have to be conducive to the overall optimum of the supply chain. It is therefore essential to analyze possible interdependencies between individual goods in advance.
Cost types for lot size optimization
The basis of all batch size calculations is consequently the determination of the relevant costs, whereby two opposing cost types must be taken into account: Inventory costs and procurement costs. Warehousing costs consist of interest on tied-up capital as well as costs for aging and wear, loss and breakage, transportation and handling within the warehouse, storage and depreciation as well as warehouse management and insurance.
Procurement costs for in-house or external production primarily include ordering costs, rebates, bonuses, discounts, additional costs for unfavorable order or production quantities, transport, insurance and packaging costs as well as order processing costs and set-up costs.

Larger batch sizes in procurement lead to higher inventories and therefore higher warehousing costs. These generally increase. proportional to the batch size, while the procurement costs fall degressively (Figure 1). In order to bring these different cost curves to an overall optimum, different procedures have been and are being developed, which are summarized under batch size procedures.
The most important batch size procedure
A distinction can be made between static and dynamic lot-sizing methods. Static methods (such as the Andler method) only focus on the complete quantity required within an observation period and are therefore only approximate calculation methods. In contrast, dynamic methods or periodic lot-sizing methods incorporate requirements over a certain period of time. This means that these processes are fundamentally more demand-oriented and can therefore adapt to changing requirements. This group of procedures includes
- The Wagner-Whitin process,
- the part-period method (piece-period equalization method),
- the unit cost method (sliding economic lot size method) and
- the Groff method and
- the Silver Meal process.
The number of different methods can be explained by the fact that no one has yet been able to accurately depict the complex reality in a formula. In this respect, all lot-sizing methods are only approximate solutions. However, some are closer to the optimum than others. It is therefore necessary to understand these processes very well in order to be able to use them effectively.
Andler is often too imprecise
The formula developed by Kurt Andler determines the minimum of the total cost curve (Figure 1), based on the assumption that the total quantity required of an item in a planning period, e.g. one year, is known. The formula derives an ideal batch size from the inventory costs and the procurement costs, which remains constant over the planning period.
The problem here is that, in practice, production or order requirements are not constant over a planning period, but follow each other irregularly and vary in amount (Fig. 2).
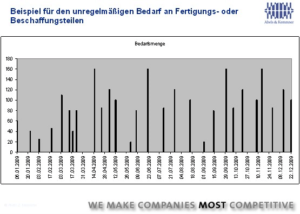
Wagner-Within is very precise
The Wagner-Within lot size calculation method takes into account the fact that the decision on a first lot size in the period under consideration automatically limits the scope for the design of subsequent lot sizes. The process determines a sequence of batches of different sizes and time intervals, which minimizes the total costs for single-stage, single-product production without capacity limits.
However, the Wagner-Whitin process becomes very complex for batch sizes for countless products. For this reason, approximation methods with simpler calculation methods were developed (part-period method, silver-meal method, Groff method), which make simplifications and thus determine the optimum cost even for different batch sizes. The deviations from the precisely calculated Wagner-Whitin method can be very significant (Figure 3).
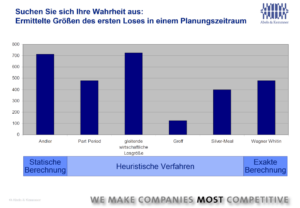
Many standard ERP systems do not use the Wagner-Whitin process. With the help of add-on solutions, however, the value chains can also be optimized with this method, which delivers very precise results.
Limited machine capacity influences formula
What all of these methods have in common is that they describe the interaction or counteraction of inventory costs and procurement costs in a single-stage, single-product production process without capacity limits. However, the question of a batch size only really arises when more than one product is manufactured. Even if several products are manufactured on one system, the formulas on which the process is based are correct, provided the batch sizes of the two products do not influence each other due to limited machine capacity. In practice, however, machine capacity is often limited. There are batch size optimization methods that take an entire process chain into account. However, if one realistically wants to include in the analyses the fact that capacities at the individual production stages are limited, reality can no longer be fully calculated with all the given interdependencies and limitations.
The situation is similar in procurement. Here, too, it is often not possible to make an isolated batch size analysis for a single product. On the one hand, several different products can “share” procurement costs: for example, a truck that can be loaded with several products. On the other hand, it is often a matter of utilizing the capacity of the truck loading area as fully as possible in order to minimize transport costs. Several products are therefore ordered together and thus influence each other with regard to their order quantities. The supposedly “optimal” order quantity for one product automatically limits the scope of order quantities for the other products.
Conclusion
In practice, a number of details need to be taken into account when calculating batch sizes. The person entrusted with the task of batch size optimization must therefore have a precise understanding of the individual processes and their characteristics. Lot size optimization is not simply supply chain optimization with the help of formulas calculated by a PC. Rather, batch size optimization is an activity for specialists who put the application of the method in the right context and carry out the cost calculations in such a way that the results are accurate.