Correctly set and up-to-date scheduling parameters are essential for an ERP system to provide any economic benefit for production, logistics and the supply chain. Continuous maintenance and optimisation of these parameters ensures that processes run efficiently and cost-effectively. Here are nine essential requirements to ensure that you achieve optimum scheduling parameters and maintain your new level in the long term.
1. regular review of parameters
A regular review of the planning parameters is crucial in order to be able to react quickly to changes in the market environment. Both internal and external influencing factors should be taken into account. Only through continuous monitoring can adjustments be made in good time.
The challenge here is that it cannot be done manually. The time required for manual data maintenance is too great.
The right way to achieve this: automation tools such as DISKOVER can make it much easier to maintain scheduling parameters. They reduce manual effort and minimise the risk of human error. Automation leaves more time for strategic tasks. Systems for the automatic maintenance of scheduling parameters are therefore indispensable for the regular maintenance of scheduling parameters.
2. broad classification of articles
The classification of items according to certain criteria simplifies the management of MRP parameters. Criteria such as life cycle, ABC/XYZ analysis or procurement indicators can be helpful here. A clear classification enables targeted optimisation and adjustments.
The challenge here is that in order to be able to set differentiated scheduling parameters, the articles must be classified according to several aspects. The item classification in ERP systems offers too little here. The articles in ERP systems are usually not classified for the purposes of controlling and sales prioritisation of articles. This means that even existing classifications, such as ABC, are sometimes not suitable for MRP parameter maintenance.
The right way to achieve your goal: software systems for dispensing parameter maintenance classify articles automatically and independently of the ERP system according to a whole range of criteria, specifically geared to the requirements of dispensing parameter optimisation.
3. consideration of seasonalities and life cycles
Seasonal factors and the life cycles of items must be taken into account when setting the replenishment parameters. It is usually more challenging to plan items correctly when demand is growing or falling in order to avoid excess stock and ensure delivery capability than it is to deal with live items.
The challenge: Incoming and outgoing items, even more so than seasonal items, require ongoing, differentiated adjustment of the replenishment parameters. Most software tools for maintaining MRP parameters are far too rigid for these challenges.
The way to the goal: Powerful tools for maintaining MRP parameters, such as DISKOVER, make it possible to set up an expert system for maintaining MRP parameters on the basis of decision tables.
4. call in specialist expertise
Regularly readjusted but incorrectly set scheduling parameters are useless. In order to set scheduling parameters correctly, a deep understanding of the calculation algorithms of ERP systems is required, as well as an understanding of the planning correlations.
The challenge here is that most medium-sized and many large companies lack experts who are familiar with the process algorithms in sufficient detail.
The right way to achieve this: External consultants can provide valuable support in optimising scheduling parameters, even where internal experts are available. They bring fresh perspectives and in-depth expertise. Working with experts can significantly speed up and improve the parameter optimisation process.
5. simulate the effect of MRP parameter settings
The dynamic interplay of market behaviour, supplier behaviour and scheduling decisions is so complex that theoretical considerations and experience alone will not lead to the desired result.
The challenge here is that existing ‘on-board resources’, such as the ERP system, cannot be used to simulate how different scheduling parameter settings affect business and logistics targets such as average stock levels, readiness to deliver and costs.
The right path to the goal: Digital twins, in which the entire supply chain is mapped with its planning and control behaviour and which are provided with empirical, historical data, play a decisive role in the optimisation of scheduling parameters today in order to develop truly economical scheduling strategies. A tool such as DISKOVER offers comprehensive functions that quickly pay for themselves.
6. train employees or purchase maintenance
A system for the automatic maintenance of scheduling parameters also requires maintenance itself, as the rules and regulations also need to be readjusted from time to time and checked using simulation.
The challenge here is that the employees responsible must be able to master the tools used to maintain the MRP parameters. This requires significantly more background knowledge than for operational materials planning and, above all, a passion for tuning logistics performance. Interested and sufficiently trained personnel are not always to be found in the company, especially not in medium-sized companies.
The right way to achieve your goal: optimising the scheduling parameters can be outsourced to external experts if you want to save the effort of training your own staff. This is often cheaper and involves less effort and less ongoing requalification due to staff turnover.
7. incorporate feedback mechanisms to sensitise dispatchers to the changed work profile
With properly maintained scheduling parameters, operational dispatchers have to correct forecast values or order proposals from the planning or ERP system much less frequently than before.
The challenge here is that operational planners are used to critically scrutinising forecasts or order suggestions from the system, which was essential without properly set planning parameters. For many users, however, it is challenging to get out of this mindset and follow the system’s suggestions. Occasionally, MRP controllers will still have to adjust order proposals because they have information that is not known to the ERP system. It would be fundamentally wrong to intervene in the system; just as wrong as adapting every order proposal again.
The right way to achieve the goal: A change programme should be carried out with the dispatchers and supervisors parallel to the introduction of automatic dispatch parameter optimisation. While dispatchers in the classic task profile are a cog in the wheel without whose intervention little works, it is now important to switch to the monitoring function and only intervene when this is absolutely necessary. This new understanding of the scheduling task must also reach superiors. They must also change their expectations.
A pragmatic way to achieve a new understanding is for the schedulers to meet regularly, initially at least weekly, and discuss all scheduling decisions in which they have intervened in the system. For each scheduling decision, the group discusses whether the intervention was necessary and, if so, whether this was because the scheduling parameters were not yet completely correct or because they had knowledge that the scheduling system did not have. This proven mechanism helps to develop a feeling for when an intervention is necessary and when it would be better to follow the system’s suggestions. In addition, this mechanism also helps to make further fine adjustments to the expert system for the dispatch parameter settings.
8. establishment of a controlling system
An effective controlling system monitors compliance with and the effectiveness of the scheduling parameters. It helps to recognise deviations at an early stage and initiate corrective measures. Good controlling is the basis for continuous improvement. The effectiveness of the MRP parameter settings can only be measured against business objectives such as readiness to deliver, stock levels and costs.
The challenge: In practice, it is precisely the important measurement of actual delivery readiness that fails, as the actual delivery readiness is determined for all items, including raw materials and semi-finished products, but for which there are no customer orders with delivery dates against which the delivery capability can be measured. It is also not sufficient to determine stock reduction or cost reduction per se. Instead, it must be known to what extent the existing potential is being utilised in the operational scheduling business.
The right way to achieve this: powerful systems for maintaining MRP parameters, such as DISKOVER, simulatively determine the stock reduction potential for each item and possibly also the cost reduction potential per item. These are important reference values with which the actual performance of materials planning must be compared. Furthermore, such systems are also able to measure an actual readiness to deliver for raw materials and semi-finished products by checking the planned requirements against the available material stocks on a daily basis and calculating an actual readiness to deliver from this.
Â
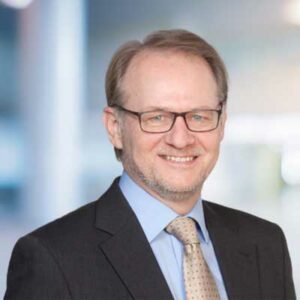