Successfully restructuring PPS with business simulations
from Andreas Gillessen
Successful restructuring projects require a high degree of behavioral change among the employees concerned. Business simulation games are a useful tool for bringing about these changes, as this case study shows.
An industrial company needed to restructure its production planning and control. The aim was to improve delivery readiness, reduce inventories and shorten throughput times. At the start of the project, a logistics business simulation was used to run through various alternatives in the process flows and to analyze and evaluate the results. In addition, an awareness of and openness to the urgent need for changes in processes should be created right from the start of the project.
Round one begins. Today’s procedure is played out. There are bottlenecks in production. The production areas are not coordinated in terms of capacity. In addition, quality problems occur. At the end of the round, no customer receives their goods at the desired time. Some of the products delivered even had quality defects.
Business simulations
- create an understanding of interrelationships
- promote activity and willingness to implement
- improve cross-departmental cooperation
= Starting point for restructuring
In the next round, the capacities between the areas are equalized. In-process quality control is introduced. Because customers require deliveries at fixed intervals, production orders are scheduled according to this rhythm. The analysis of the second round already shows the first improvements. This allows production output to be increased by 63% and production quality to be improved by 43%. However, the basis for the improvements was still at a very low level.
Although the production orders have now been scheduled in line with market demand, only a completely unacceptable delivery readiness level of 20% can be achieved. In addition, inventories are only slightly lower and lead times are still far too long. The discussion begins. Why doesn’t one employee manufacture the entire product? Can’t individual production areas be merged? Why do stocks build up in front of the workstations even though the work content is balanced and the deliveries from external suppliers are coordinated with the order workload? Why are we still producing too much poor quality? Continuous utilization of production orders does not guarantee delivery/output at the same rate. We should pull instead of push! Only firmly defined quantities of containers may be located in the production areas. And, and, and, ….
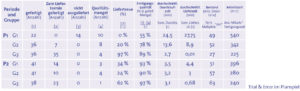
These and other measures will be implemented and tested in the third and subsequent rounds. The key figures can be successively increased until almost all targets are achieved in the final round: Delivery reliability 97%, production quality 88% (not yet sufficient), inventory reduction 54%, lead time reduction per product of 13.6 min. to 2.9 min. (-78 %).
The results presented show that the business game was extremely successful. But business games are also particularly effective as an aid to change processes. A&K is currently developing a business game in cooperation with the Cologne University of Applied Sciences and the Institute for Production Engineering and Organization (IPO) at the Cologne University of Applied Sciences, which is being carried out in a real “production company for action-oriented learning” (PHL). A simulation game on a “living object”.
Why simulation games are particularly efficient in change processes
Business simulations are a very useful tool for imparting knowledge and changing employee behavior. Such a tool can form the basis for successful project management and provide helpful services during the implementation phase, particularly for upcoming restructuring projects. This lays the foundation for sustainable and successful change. However, it must be emphasized that the actual work of restructuring lies in the detailed design and implementation of the concepts developed and that the simulation game can “only” be an auxiliary tool, albeit a very efficient one, for successful project management. At the heart of this is the fact that all theory is gray. A change in the way employees think and act can be achieved more quickly, cost-effectively and sustainably by gaining personal experience. However, everyday business life is not suitable for this. The costs for wrong decisions, the time required and the duration to achieve results would be many times higher than simulating different situations in a “model world” of a business simulation. As a kick-off event and for project support, business simulation games are therefore a useful tool for achieving motivation, willingness to change and an understanding of the interrelationships and interdependencies of process changes among employees.
The benefits in a specific project
The participants experienced the connections and effects of their own decisions quickly and memorably in a playful way. They had a different responsibility in each new game round. The understanding of the problems of the other company divisions was thus “physically” experienced within just one round of the game. The environment of the business simulation game playfully “forced” the employees to think holistically, namely in planning and decision-making
- Recognize and include all “relevant” data
- to “anticipate” the effects of their decisions as well as possible
- make balanced decisions in order to minimize any conflicts of objectives that may arise
In addition, aspects such as
- the selection, implementation and evaluation of improvement measures,
- analyzing the potential for improvement of the individual measures
- the reduction of prejudices and
- knowledge transfer, teamwork and motivation
addressed and improved by this workshop.
The game master
The successful use of a business simulation depends on many factors. However, the key to success clearly lies in the hands of the game master. An experienced leader will always achieve performance-motivating learning success.
The situation in which a participant confidentially informs the game master that they were against the group decision is a familiar one. It usually occurs when one or more plan runs are unsuccessful. In the real business situation, problems often only come to light slowly. In the world of business simulations, this usually happens very quickly. One wrong decision can already lead to conflict, hidden or open.
In such situations, the game master is called upon. It must be able to lead participants back into the group and deal with dominant participants who need to make a name for themselves. This requires a good dose of empathy and the ability to overcome conflict situations by motivating the participants.
He or she must also have a reliable command of the figures in the business simulation and be a proven expert in the areas of production organization and logistics. His ability to pass on knowledge and expertise is crucial to the learning success of the participants. They must be able to quickly understand business interrelationships and interdependencies, learn them easily and also make their decisions on the basis of sound business data.
In addition to the difficult selection of a suitable business simulation for a company’s specific situation, the implementation of the simulation and thus the simulation manager is crucial for the start of successful project management of operational restructuring measures.